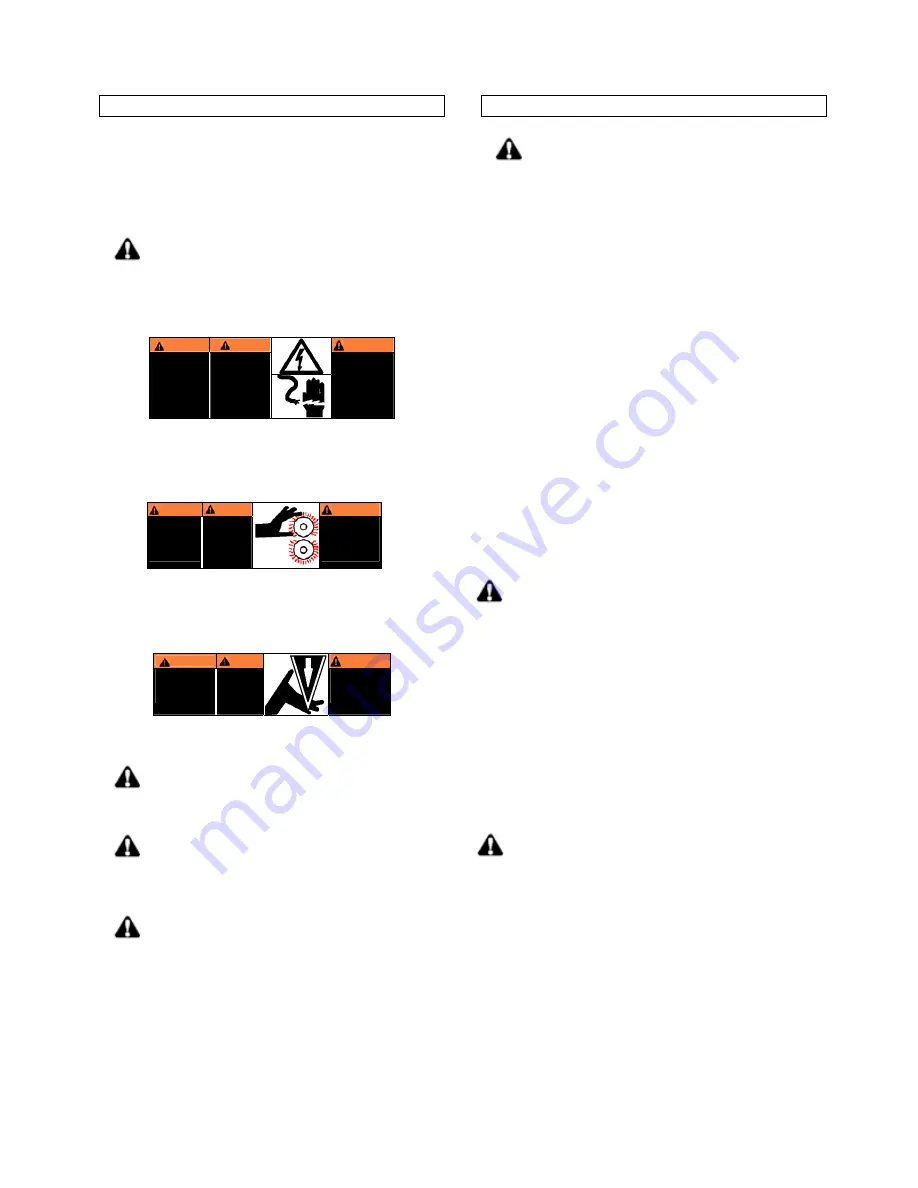
GBC 2064WF-1
Operation Manual
© 2009 General Binding Corporation an ACCO Brands CO. Page 4
IMPORTANT SAFETY INSTRUCTIONS
YOUR SAFETY AS WELL AS THE SAFETY OF OTHERS IS
IMPORTANT TO GBC. IN THIS INSTRUCTION MANUAL
AND ON THE PRODUCT, YOU WILL FIND IMPORTANT
SAFETY MESSAGES REGARDING THE PRODUCT. READ
THESE MESSAGES CAREFULLY. READ ALL OF THE
INSTRUCTIONS AND SAVE THESE INSTRUCTIONS FOR
LATER USE.
THE SAFETY ALERT SYMBOL PRECEDES
EACH SAFETY MESSAGE IN THIS
INSTRUCTION MANUAL. THE SYMBOL
INDICATES A POTENTIAL PERSONAL SAFETY
HAZARD TO YOU OR OTHERS. THE
FOLLOWING WARNINGS ARE FOUND UPON
THIS PRODUCT.
ADVERTENCIA
Attention
Avertissement
Riesgo de choque
eléctrico
No abra:
Adentro no hay
piezas reparables
por el usuario.
Mantenimiento
solamente por
personal calificado
Risque de
Secousseélectrique.
Ne pas ouvrir.
Pas de pièces
réparables par
l'utilisateur.
Entretien
seulement par
personnel qualifié.
Electrical shock
hazard.
Do not open.
No user serviceable
parts inside.
Refer servicing to
qualified service
personnel.
THIS SAFETY MESSAGE MEANS THAT YOU COULD BE
SERIOUSLY HURT OR KILLED IF YOU OPEN THE
PRODUCT AND EXPOSE YOURSELF TO HAZARDOUS
VOLTAGE.
THIS SAFETY MESSAGE MEANS THAT YOU COULD BE
BURNED AND YOUR FINGERS COULD BE TRAPPED
AND CRUSHED IN THE HOT ROLLERS. CLOTHING,
JEWELRY AND LONG HAIR COULD BE CAUGHT IN THE
ROLLERS AND PULL YOU INTO THEM.
ADVERTENCIA
Attention
Avertissement
NAVAJA FILOSA.
Mantener manos y
dedos a distancia.
LAME
COUPANTE.
Tenir mains et
doigts à l'écart.
SHARP BLADE.
Keep hands and
clothing away.
THIS SAFETY MESSAGE MEANS THAT YOU COULD
CUT YOURSELF IF YOU ARE NOT CAREFUL.
WARNING: THIS SAFETY ALERT SYMBOL
PRECEDES EACH SAFETY MESSAGE IN THIS
INSTRUCTION MANUAL. THE SYMBOL
INDICATES A POTENTAL PERSONAL SAFETY
HAZARD TO YOU OR OTHERS.
WARNING: DO NOT ATTEMPT TO SERVICE OR
REPAIR THE 3064 WF LAMINATOR.
WARNING: DO NOT CONNECT THE
LAMINATOR TO AN ELECTRICAL SUPPLY OR
ATTEMPT TO OPERATE THE LAMINATOR
UNTIL YOU HAVE COMPLETELY READ THESE
INSTRUCTIONS. MAINTAIN THESE
INSTRUCTIONS IN A CONVENIENT LOCATION
FOR FUTURE REFERENCE.
IMPORTANT SAFEGUARDS
WARNING: TO GUARD AGAINST INJURY THE
FOLLOWING SAFETY PRECAUTIONS MUST BE
OBSERVED IN INSTALLATION AND USE OF
THE LAMINATOR.
General:
Keep hands, long hair, loose clothing, and articles such as
necklaces or ties away from the front of the heat and pull
rollers to avoid entanglement and entrapment.
The heat rollers can reach temperatures over 300˚F (150°C).
Avoid contact with the heat rollers during operation or shortly
after power has been removed from the laminator.
Keep hands and fingers away from the path of the sharp film
cutter blade located at the film exit.
Do not use the laminator for other than its intended purpose.
Avoid moving the Laminator on uneven floor surfaces. Never
tilt the laminator.
Do not defeat or remove electrical and mechanical safety
equipment such as interlocks, shields and guards.
Do not insert objects unsuitable for laminating or expose the
equipment to liquids.
Electrical:
The Laminator should be connected only to a source of power
as indicated in these instructions and on the serial plate located
on the rear of the laminator. Contact an electrician should the
attachment plug provided with the Laminator not match the
receptacles at your location.
WARNING: THE RECEPTACLE MUST BE
LOCATED NEAR THE EQUIPMENT AND EASILY
ACCESSIBLE.
Do not operate the Laminator with a damaged power supply
cord or attachment plug, upon occurrence of a malfunction, or
after the laminator has been damaged. Contact GBC’s
Technical Service Department or your dealer/distributor for
assistance.
Service:
Perform only the routine maintenance procedures referred to in
these instructions
WARNING: DO NOT ATTEMPT TO SERVICE OR
REPAIR THE LAMINATOR
Disconnect the plug from the receptacle and contact GBC’s
Technical Department or your dealer/distributor when one or
more of the following has occurred.
•
The power supply cord or attachment plug is damaged.
•
Liquid has been spilled into the laminator.
•
The laminator is malfunctioning after being mishandled.
•
The laminator does not operate as described in these
instructions.
ADVERTENCIA
Attention
Avertissement
RODILLOS
CALIENTES.
PUNTO DE
PINCHAMIENTO.
Mantener manos y
ropa a distancia.
ROULEAUX
CHAUDS.
POINT DE
PINCEMENT.
Tenir mains et
vêtements à
l'écart.
HOT ROLLS.
PINCH POINT.
Keep hands and
clothing away.