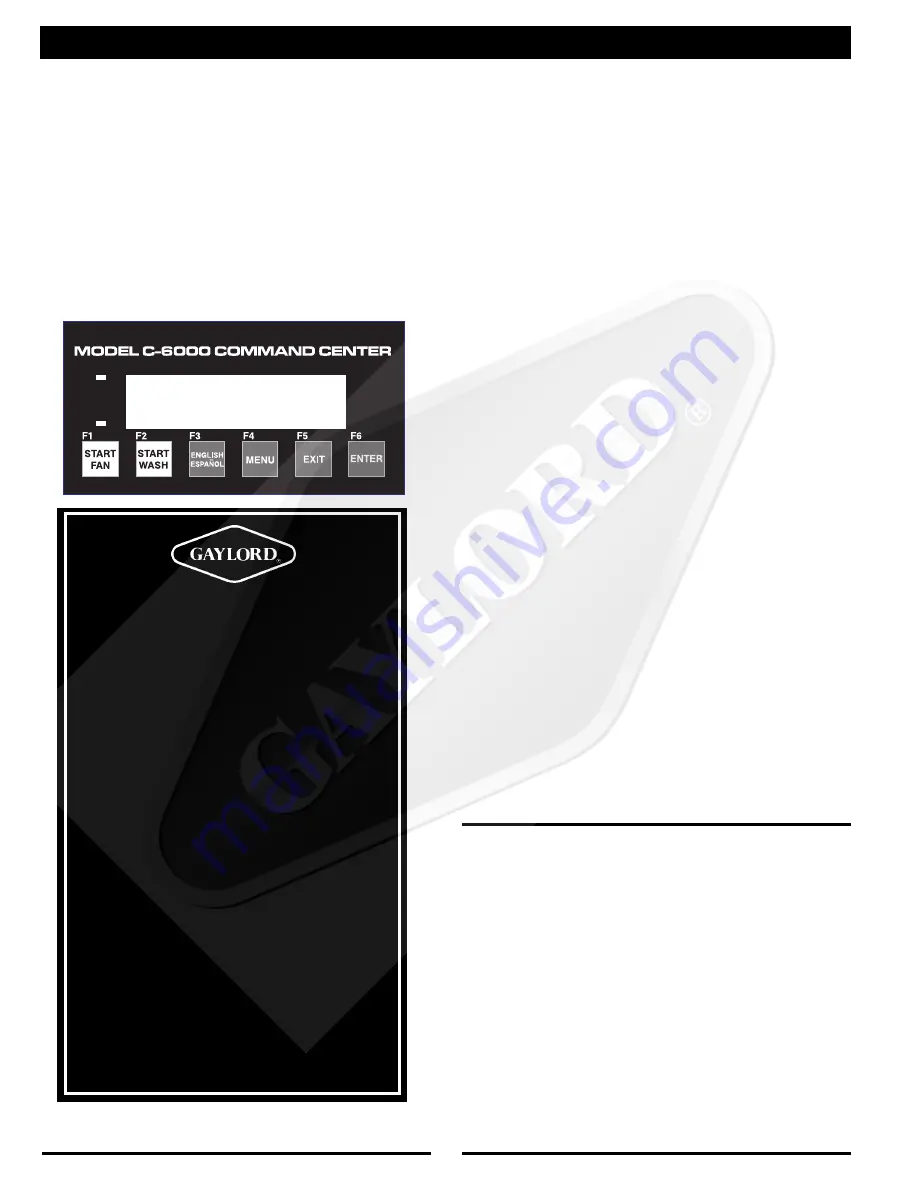
14
MODEL C-6000 SERIES COMMAND CENTER - INSTRUCTIONS
General Description:
The C-6000 Command Center is designed to start and stop the
exhaust fan and wash up to 5 groups of ventilators in sequence
with a delay period between each group. A sequence wash may
be necessary if the building’s hot water system is not capable
of supplying the required volume of water at one given time.
The exhaust fan and wash sequence may be started Manu-
ally by pushing the “Start Fan” or “Start Wash” buttons, or
may be programmed for Automatic operation.
Programmed operations may include:
1.
Starting the exhaust fan once within a 24-hour period.
2.
Stopping the exhaust fan and starting the wash cycle
sequence once within a 24-hour period
The C-6000 Command Center provides information and pro-
gramming for various functions by accessing nine different menu
catagories. An overview of the nine menu items are as follows:
1.
Service - Displays Gaylord's website address:
gaylordusa.com
2.
Detergent - Displays Toll-Free Number to order deter-
gent: 800-286-2010
3.
Wash Length - Sets length of each wash cycle from 3 to
9 minutes
4.
Delay Time (for sequence wash units only) - Sets delay
between washes from 1 minute to 99 minutes
5.
Set Clock - Day, hour and minutes
6.
AutoMode [M or A] - Sets the C-6000 to Manual or
Automatic modes. In Automatic mode, the C-6000 will
start the Fan and Wash at the preset times that were set
using the Set Wash Times option.
A = Automatic / M = Manual
Also allows individual days (Mon, Tues., etc.) to be set ON
or OFF when Automatic mode is selected.
7.
Set Wash Times - Sets Start Times for Automatic start
of Fan and wash when C-6000 is set to Automatic mode.
8.
Wash Test - Runs through a complete Wash Cycle with
decresed times
Damper Closing Time = 10 sec.
Wash Times = 10 sec.
Water Heating Time = 10 sec.
Exits menu when finished.
9. Number of Washes - Preset at factory and protected with
a password. Allows the number of washes to be changed
from 1 to 5 (S1 to S5).
Spanish (Español) Instructions:
The C-6000 Command Center has the ability to display its
commands and messages in either English or Spanish
(Español).
Press the "ENGLISH / ESPAÑOL" [F3] button to toggle the
language displayed from English to Spanish (Español) or from
Spanish (Español) to English.
NOTE: All messages displayed by pressing the "MENU"
[F4]button only appear in English. They will not appear in
Spanish (Español).
Using the Menu:
To Enter the Menu, press the MENU button [F4].
To navigate the Menu:
• Press [F1] to go to the Next menu item
• Press [F2] to go to the Previous menu item
FIGURE 9
C-6000 COMMAND CENTER
3.
Programming the length of the wash cycles and delay
periods between the wash cycles. The maximum length
of a wash cycle is 9 minutes. The maximum length of the
delay period is 99 minutes.
4.
Skipping a day so the exhaust fan and wash cycle do not
operate for holidays or specific days within a 7-day week
when the kitchen is not operating.
OPERATING INSTRUCTIONS
1. Push "Start Fan" before turning on cooking equipment.
Note: There is a 45 second delay after pushing the button
before the fan starts to allow the damper to open to the
"Exhaust" position.
2. At the end of the day, or whenever cooking is completed,
push "Start Wash". This will turn off the exhaust fan and
close the damper forward to the "Wash" position.
Note:
There is a 45 second delay after pushing the button
before the wash cycle starts, to allow the damper, if so
equipped, to close to the "Wash" position. After closing, the
timed wash cycle begins. Damper stays closed until "Start
Fan" is pushed.
Note:
24 hour kitchens must push "Start Wash"
at least once a day, or as needed for proper cleaning.
3. To set the length of the time for the wash cycle, press
"Menu", then press [F1] until "Wash Length" appears on the
display. Follow the instructions on the display to edit the
length of washes as necessary.
Note:
Refer to the programming instructions on the inside of
this cabinet for more information on programming the
C-6000 Command Center.
LOW DETERGENT
The green light will flash and
"Low Detergent"
will be displayed
on the C-6000 Command Center indicating the detergent
is low.
FIRE CONDITION
1. A flashing red light and the message
"Ext. Fire Active"
indicates the control is in an
External Fire Mode
- exhaust
fan on, damper open, and water wash nozzles on.
2. A continuous red light and the message
"Fire In Hood"
indicates the control is in an
Internal Fire Mode
- exhaust
fan off, damper closed, and water wash nozzles on.
MODEL C-6000 COMMAND CENTER
Summary of Contents for C-6000 Series
Page 5: ...5 CG3 VENTILATOR DESCRIPTIONS ...
Page 40: ...40 DETERGENT PUMP ...
Page 42: ...42 WIRING DIAGRAM FOR MODEL C 6000 10 120 VOLT ...
Page 43: ...43 WIRING DIAGRAM FOR MODEL C 6000 10 220 VOLT ...
Page 44: ...44 WIRING DIAGRAM FOR MODEL C 6000 10 A 120 VOLT ...
Page 45: ...45 WIRING DIAGRAM FOR MODEL C 6000 10 A 220 VOLT ...
Page 46: ...46 WIRING DIAGRAM FOR MODEL C 6000 10 B 120 VOLT ...
Page 47: ...47 WIRING DIAGRAM FOR MODEL C 6000 20 B 120 VOLT ...
Page 48: ...48 WIRING DIAGRAM FOR MODEL C 6000 10 B 220 VOLT ...
Page 49: ...49 WIRING DIAGRAM FOR MODEL C 6000 20 B 220 VOLT ...