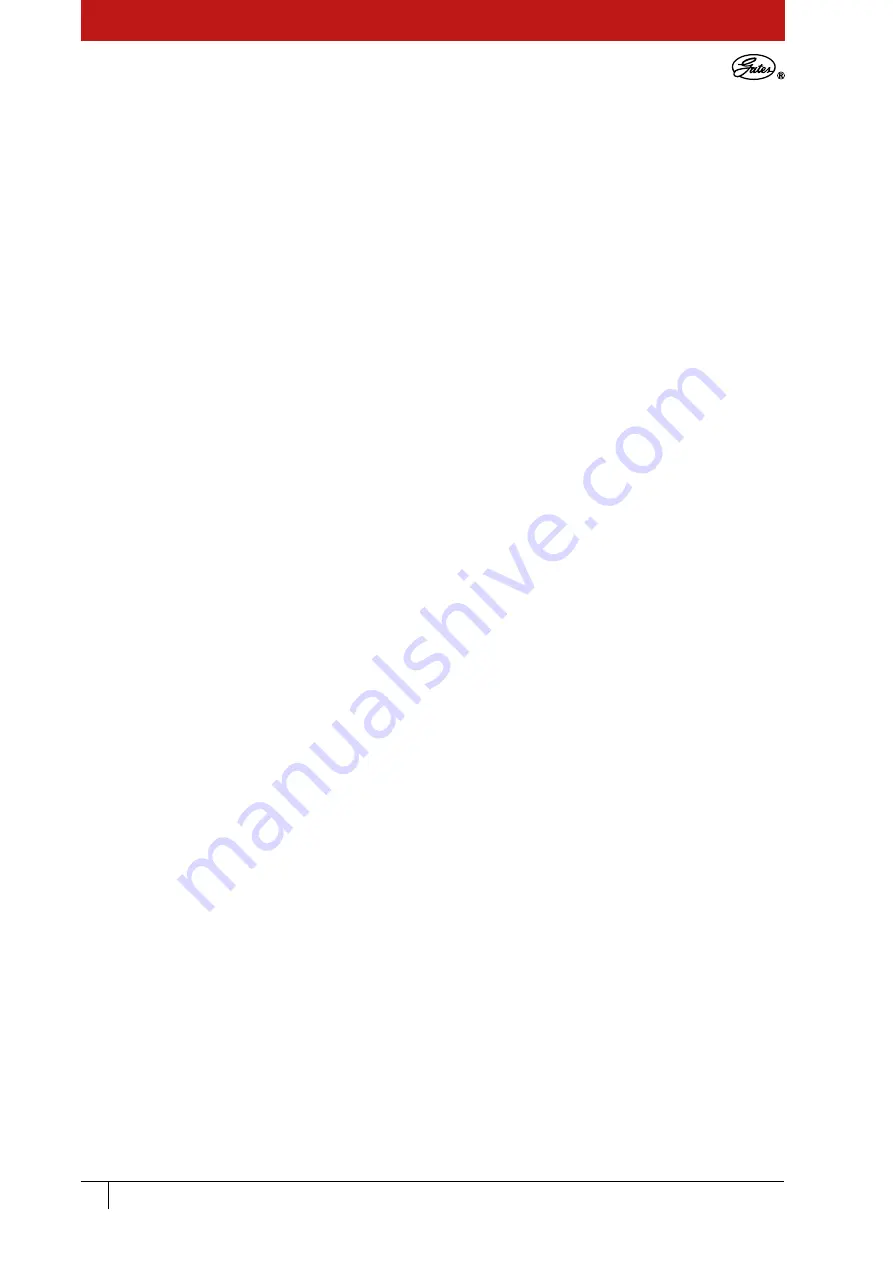
4
GATES.COM
UNIPRESS 4 (UP4)
OPERATION MANUAL
1 GENERAL DESCRIPTION
In this chapter, you will find information for using the operation manual and general safety instructions
for handling the machine.
1.1 NOTES ON THE OPERATION MANUAL (OM)
This Operation Manual is part of the product:
UNIPRESS 4
(universal drive unit for pipe presetting)
As a central part of the operator’s reference material, this Operation Manual is of special importance.
Heeding the instructions, data and regulations of the OM will help you to operate the machine safely and
efficiently.
In reference to the illustrations and details of this Operation Manual, the machine is subject to technical
alterations if these serve the purpose of improvement.
This Operation Manual may describe special equipment which is not part of your machine.
1.1.1 DESIGN OF THE OPERATION MANUAL
Safety precautions are indicated by corresponding symbols and printed in
bold italics.
Summary of Contents for UNIPRESS 4
Page 1: ...OPERATION MANUAL UNIPRESS 4 UP4 GATES TUBE FITTINGS GMBH...
Page 37: ...37 GATES COM UNIPRESS 4 UP4 OPERATION MANUAL 7 SPARE PARTS 7 1 HOUSING...
Page 40: ...40 GATES COM UNIPRESS 4 UP4 OPERATION MANUAL 7 4 HYDRAULIC DRIVE...
Page 49: ...49 GATES COM UNIPRESS 4 UP4 OPERATION MANUAL 8 APPENDIX 8 1 ELECTRIC CIRCUIT DIAGRAM...
Page 50: ...50 GATES COM UNIPRESS 4 UP4 OPERATION MANUAL ELECTRIC CIRCUIT DIAGRAM...
Page 51: ...51 GATES COM UNIPRESS 4 UP4 OPERATION MANUAL ELECTRIC CIRCUIT DIAGRAM...
Page 52: ...52 GATES COM UNIPRESS 4 UP4 OPERATION MANUAL 8 2 HYDRAULIC CIRCUIT DIAGRAM...
Page 53: ......