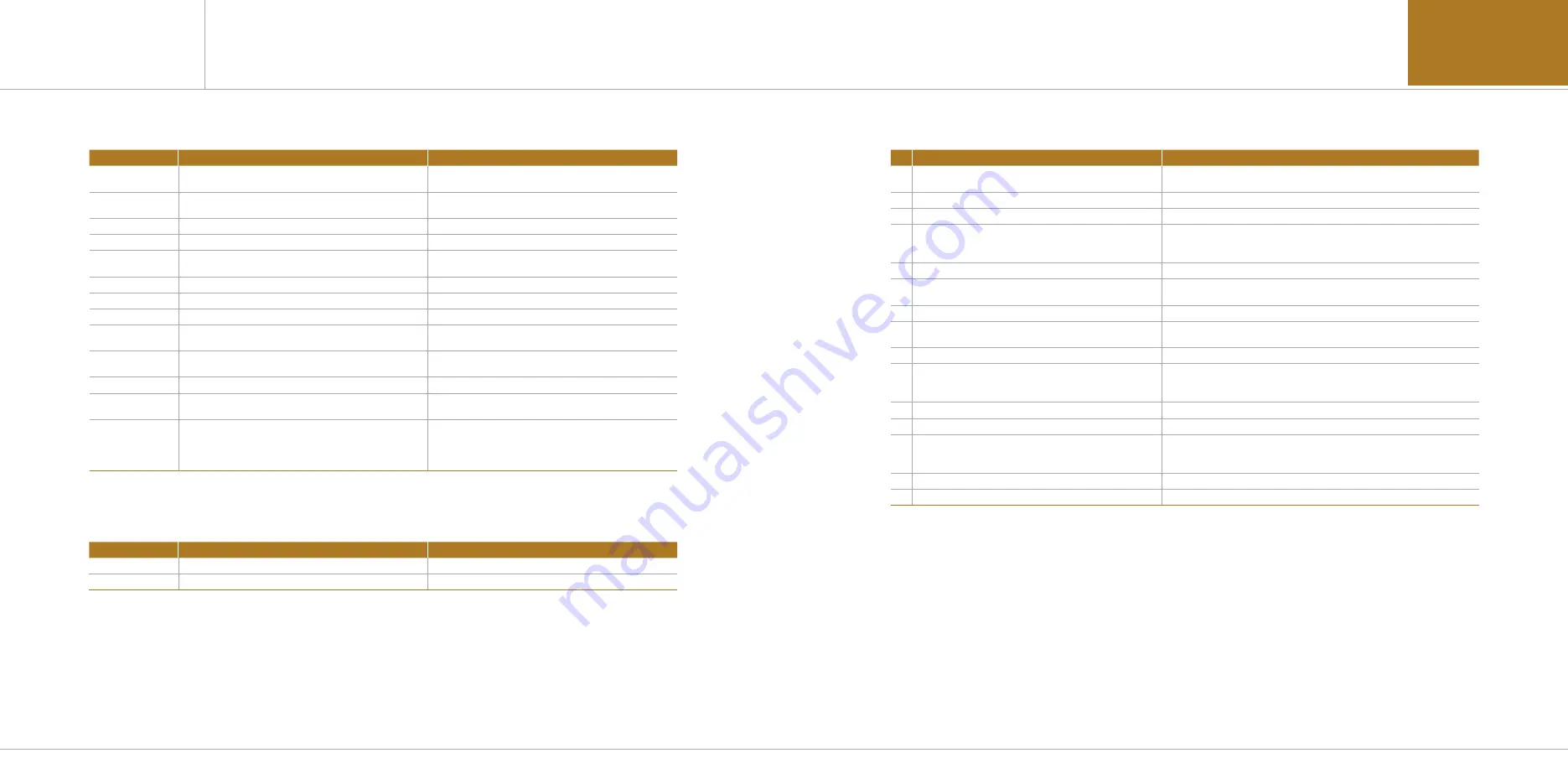
www.gastron.com
28
_
29
GTD-5100F
Instruction Manual
8. Troubleshooting
8. Troubleshooting
8.1. Fault List
FAULT
DESCRIPTION & CONDITION
CAUSE
E-10
When a sensor cartridge is not equipped in the
main body or it is defective.
1) Sensor cartridge connection fault
2) Sensor Cartridge Unit Fault
E-11
When there is no communication between the
main body and sensor cartridge.
1) Sensor Cartridge Unit Fault
2) Main Body Fault
E-12
When there is no gas sensor in Sensor Cartridge.
Sensor cartridge unit fault
E-13
When EEPROM of Sensor PCB is defective.
Sensor Cartridge EEPROM Fault
E-14
When sensor status is defective during self-test.
Fault in gas sensor function built in the sensor
cartridge.
E-20
When flow sensor does not run.
Flow sensor fault in Main Unit.
E-21
When flow rate of flow sensor is low.
When flow rate is measured to be below 0%.
E-22
When flow rate of flow sensor is high.
When flow rate is measured to be above 120%.
E-23
When flow rate at flow rate sensor is below the low
level (250 ml)
When flow rate is measured to be below the low level
(during L-FL on).
E-30
When pyrolyzer current is measured to be below
50mA.
1) Pyrolyzer connection fault
2) Pyrolyzer internal hot-wire fault
E-31
When EEPROM in the main unit is not detected.
EEPROM fault in Main Board.
E-32
When pyrolyzer current is measured to be above
900mA.
Pyrolyzer fault
E-34
When gas measurement is hunting continuously.
1) Check gas sensor measurement status.
2) Check noise input from input power.
3) Sensor cartridge unit fault
4) Main Body Fault
8.2. Warning List
[Table 6. Warning Code]
WARNING
DESCRIPTION & CONDITION
CAUSE
W-01
When calibration validation has passed.
Exceeded calibration validation period.
W-02
When manufacture data of sensor is not entered.
Sensor Manufacturing Date Error
8.3. Recovery List
[Table 7. Recovery List]
NO
CAUSE
SOLUTION
1
Sensor cartridge connection fault
1) Check status of sensor cartridge connector
2) Change sensor cartridge
2
Sensor cartridge unit fault
Change sensor cartridge
3
Gas sensor function failure
Change gas sensor
4
Sensor Cartridge EEPROM Fault
1) Perform Factory Initialization then correct parameter and
re-calibrate
2)Change sensor cartridge when the same problem occurs again
5
Flow rate sensor fault
Change main unit
6
When flow rate is measured to be below 0%.
1) Check flow rate at inlet and outlet.
2) Change the main unit if it is not from internal clogging.
7
When flow rate is measured to be above 120%.
Change main unit
8
Pyrolyzer connection fault
1) Check status of pyrolyzer connector
2) Change pyrolyzer if the connector is normal.
9
Pyrolyzer internal hot-wire fault
Change Pyrolyzer
10 EEPROM fault in Main Board.
1) Perform Factory Initialization then correct parameter and
re-calibrate
2) Change the main body when the same problem occurs again
11 Pyrolyzer fault
Change Pyrolyzer
12 Main Body Fault
Change main unit
13 Main unit time setting error
1) Reset time
2) Change Backup Battery
3) Change main unit
14 Exceeded calibration validation period.
Re-calibrate sensor or change sensor.
15 Sensor Manufacturing Date Error
Re-calibrate sensor or contact the manufacturer.
[Table 5. Fault List]