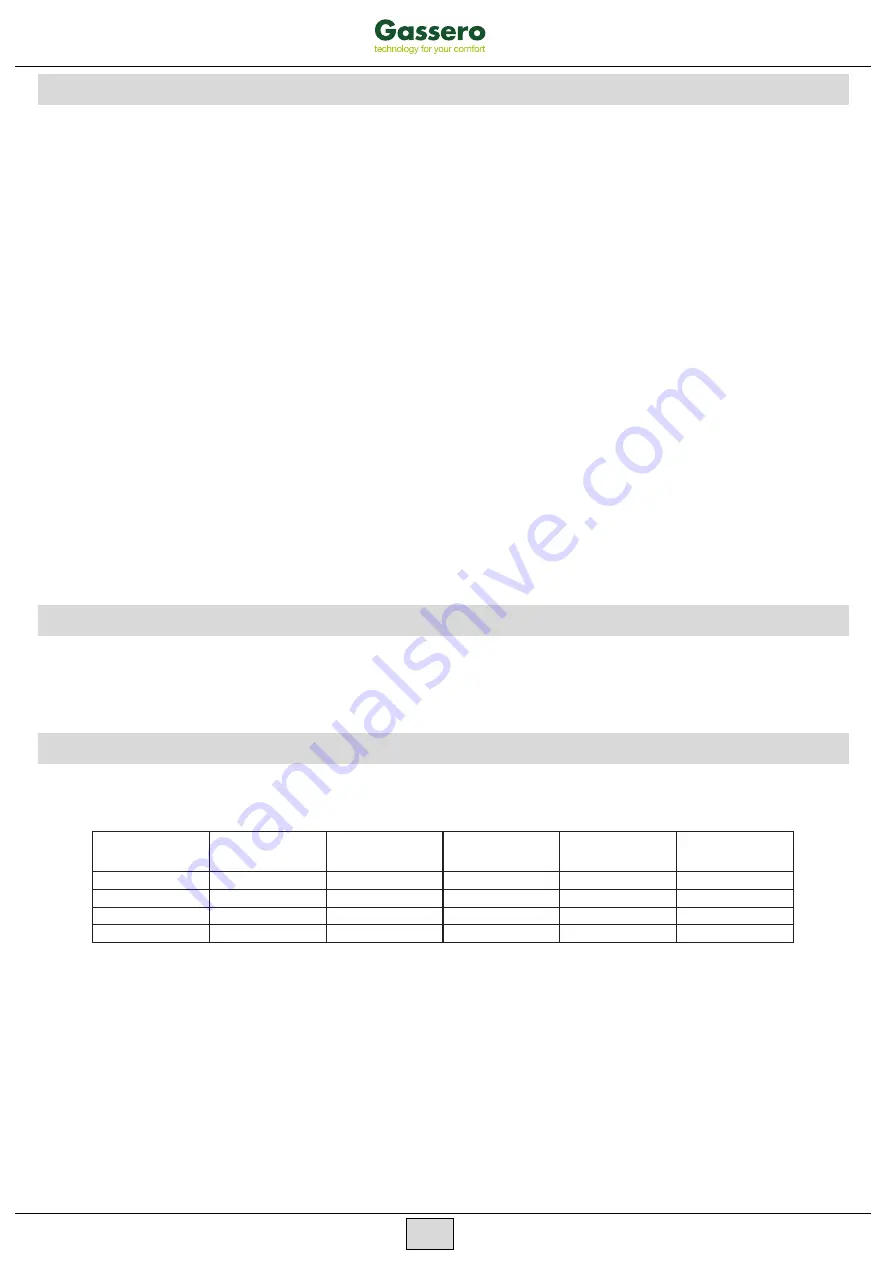
52
24.3.
Decommissioning
Before carrying out this procedure, it is essential that the technician is completely familiar with the equipment
and all its detail. It is recommended good practice that all refrigerants are recovered safely. Prior to the task
being carried out, an oil and refrigerant sample shall be taken in case analysis is required prior to re-use of
reclaimed refrigerant. It is essential that electrical power is available before the task is commenced.
a) Become familiar with the equipment and its operation.
b) Isolate system electrically.
c) Before attempting the procedure ensure that: mechanical handling equipment is available, if required, for
handling refrigerant cylinders; all personal protective equipment is available and being used correctly; the
recovery process is supervised at all times by a competent person; recovery equipment and cylinders
conform to the appropriate standards
d) Pump down refrigerant system, if possible.
e) If a vacuum is not possible, make a manifold so that refrigerant can be removed from various parts of the
system.
f) Make sure that cylinder is situated on the scales before recovery takes place.
g) Start the recovery machine and operate in accordance with manufacturer's instructions.
h) Do not overfill cylinders. (No more than 80 % volume liquid charge).
i) Do not exceed the maximum working pressure of the cylinder, even temporarily.
j) When the cylinders have been filled correctly and the process completed, make sure that the cylinders and
the
k) equipment are removed from site promptly and all isolation valves on the equipment are closed off.
l) Recovered refrigerant shall not be charged into another refrigeration system unless it has been cleaned
and checked.
24.4.
Notice before Seasonal Use
a) Check whether air inlets and air outlets of indoor and outdoor units are blocked
b) Check whether ground connection is reliable or not
c) If unit starts up after not operating for a long time, it should be power on 8 hours before operation starts so
as to preheat the outdoor compressor
24.5.
Precautions for Freeze Protection in Winter
Under subzero climatic conditions in winter, anti-freeze fluid must be added into the water cycle and external
water pipes should be properly insulated. Glycol solution is recommended as the anti-freeze fluid.
Note: “Concentration” listed in the table above indicates the mass concentration
Concentration
%
Freezing Temp
°C
Concentration
%
Freezing Temp
°C
Concentration
%
Freezing Temp
°C
4.6
-2
19.8
-10
35
-21
8.4
-4
23.6
-13
38.8
-26
12.2
-5
27.4
-15
42.6
-29
16
-7
31.2
-17
46.4
-33