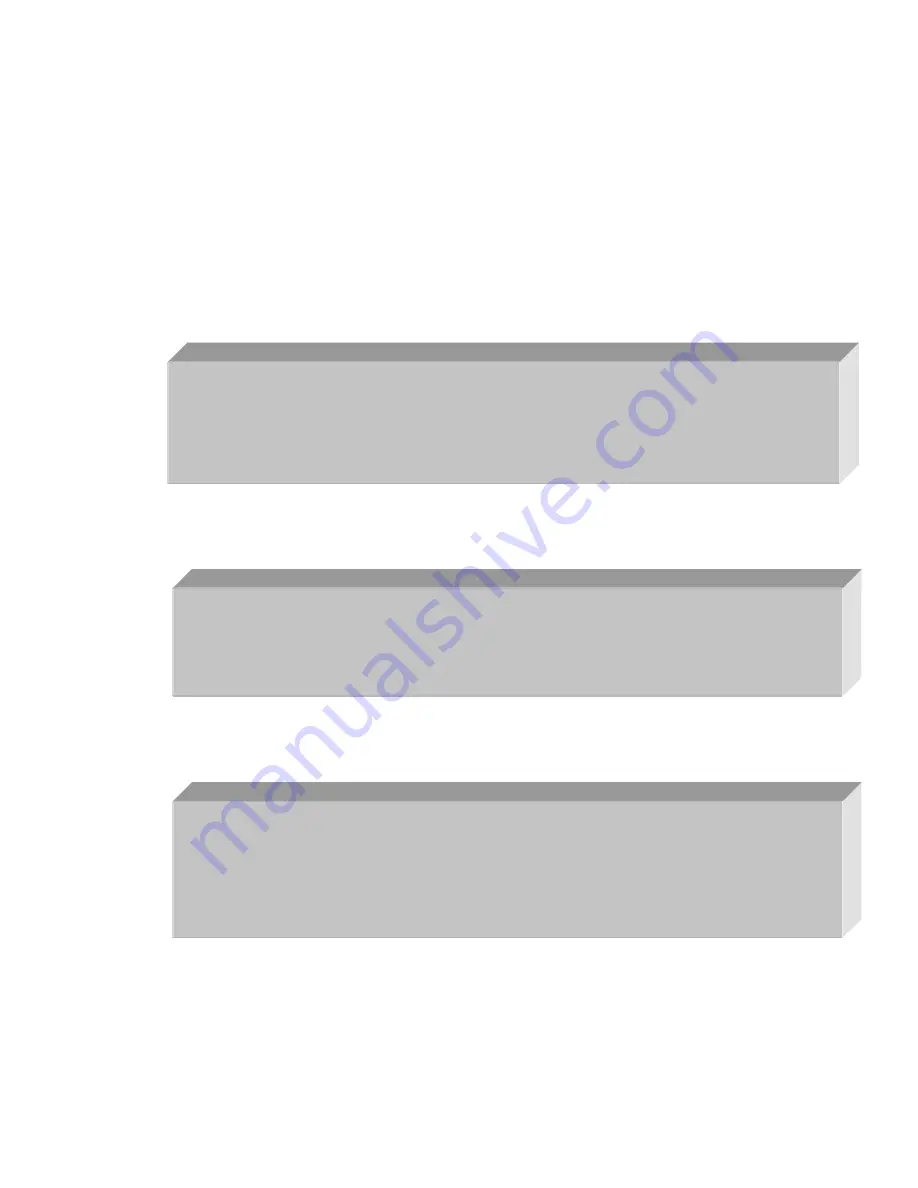
IOM GMI 2M & 2ML Nov 2010.doc
27
V: Power
Connection
¾
Inspect all wiring connections to the unit and ensure they comply with all
applicable local codes.
¾
Ensure that the appropriate power supply has been connected to the unit (please
refer to the electrical rating on the unit’s nameplate).
¾
Ensure the temporary jumpers have been removed from the unit’s control panel.
¾
If applicable, ensure the external control connections have been wired.
NOTE
¾
Start-up and commissioning MUST be carried out by a GMI
qualified technician.
WARNING
The field start-up report MUST be faxed to GMI at 604-574-9572
within 10 days of start-up. Failure to do so will result in cancellation
of all expressed and/or implied warranties.
WARNING
Ensure the manual gas valve is closed prior to power being supplied
to the boiler/water heater
Summary of Contents for GMI 2M
Page 6: ...IOM GMI 2M 2ML Nov 2010 doc 6 SECTION 1 INTRODUCTION...
Page 13: ...IOM GMI 2M 2ML Nov 2010 doc 13 SECTION 2 INSTALLATION...
Page 22: ...IOM GMI 2M 2ML Nov 2010 doc 22 SECTION 3 OPERATION...
Page 30: ...IOM GMI 2M 2ML Nov 2010 doc 30 SECTION 4 MAINTENANCE...
Page 34: ...IOM GMI 2M 2ML Nov 2010 doc 34...
Page 35: ...IOM GMI 2M 2ML Nov 2010 doc 35 START UP REPORT...