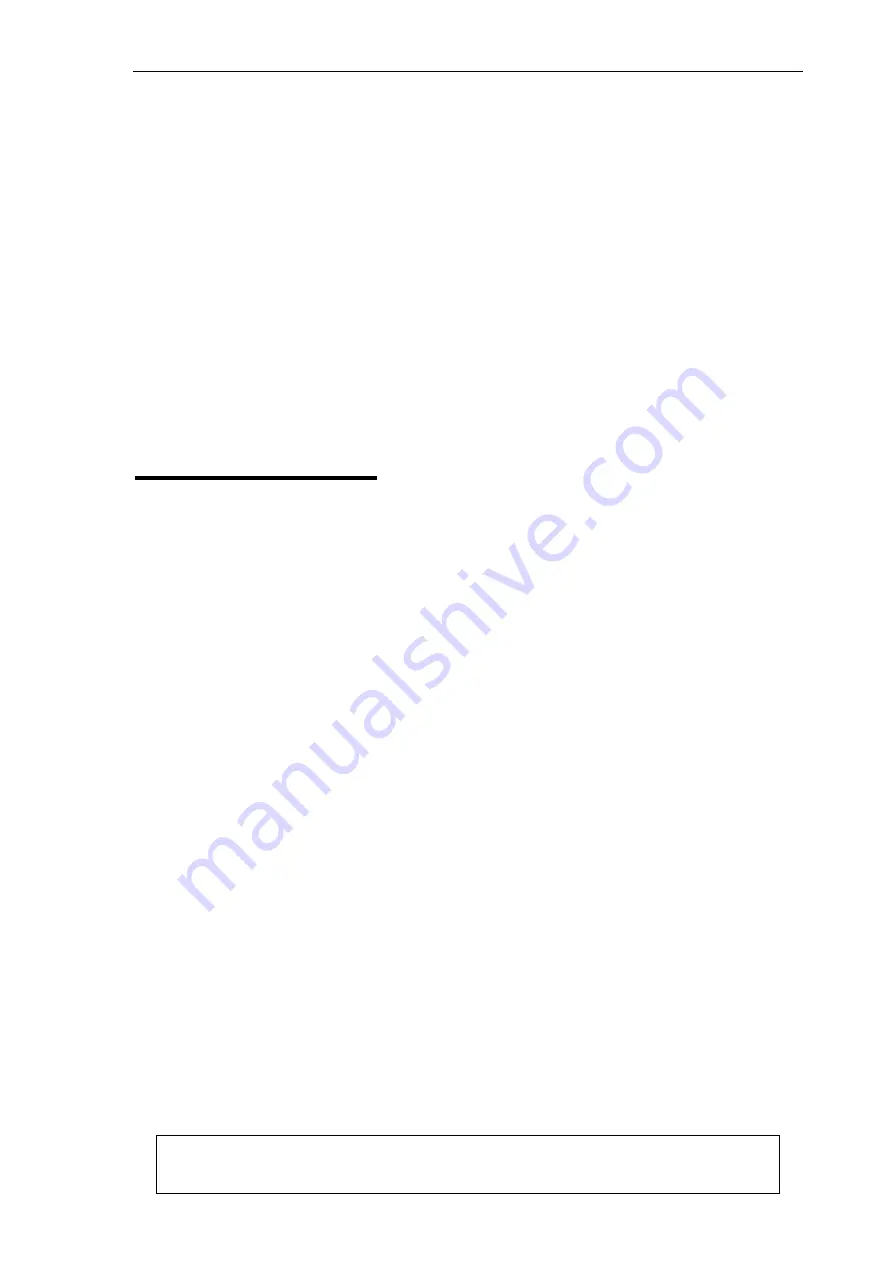
DRILL PRESS MANUAL
We reserve the right of the amendment addition and deletion of the
specifications, explanatory wording, etc. printed in this manual
8
WORKING CLEARANCES
Working clearances can be thought of as the distances between machines and obstacles
that allow safe operation of every machine without limitation. Consider existing and
anticipated machine needs, size of material to be processed through each machine, and
space for auxiliary stands and/or work tables. Also consider the relative position of each
machine to one another for efficient material handling. Be sure to allow yourself sufficient
room to safely run your machines in any foreseeable operation.
LIGHTING AND OUTLETS
Lighting should be bright enough to eliminate shadow and prevent eye strain. Electrical
circuits should be dedicated or large enough to handle combined motor amp loads. Outlets
should be located near each machine so power or extension cords are not obstructing
high-traffic areas. Be sure to observe local electrical codes for proper installation of new
lighting, outlets, or circuits.
3: ASSEMBLY
Beginning Assembly
Most of your Drill Press has been assembled at the factory, but some parts must be
assembled or installed after delivery. We have organized the assembly process into steps.
Please follow along in the order presented here.
Column/Base
Drill press must be secured to the floor using anchor bolts, or the base should be secured
to a piece of plywood.
1. Unplug machine before assembly.
2. Secure the base to the floor using the appropriate anchor bolts.
3. Place the column on the base and line up the mounting holes. Insert and tighten the
M10-1.5 hex head bolts with a wrench.
Table Support
1. Thread the 12mm table lock handle 3 turns into the table support bracket as shown in
Figure 3.
2. Insert the pinion gear into the hole on the side of the table support bracket from the
inside, starting with the pinion shaft as shown in
Figure 3.
Align setscrew in crank
handle with flat on pinion gear shaft and secure using the 3mm Allen
®
wrench provided
as shown in
Figure 4
.
3. Examine the rack and note that the gear teeth extend farther on one end than the other.
The end of the rack where the gear teeth are closest to the end should be positioned
down. Insert the rack into the table support bracket and align it with the pocket as
shown in
Figure 4
. The gear teeth on the rack must also face out.