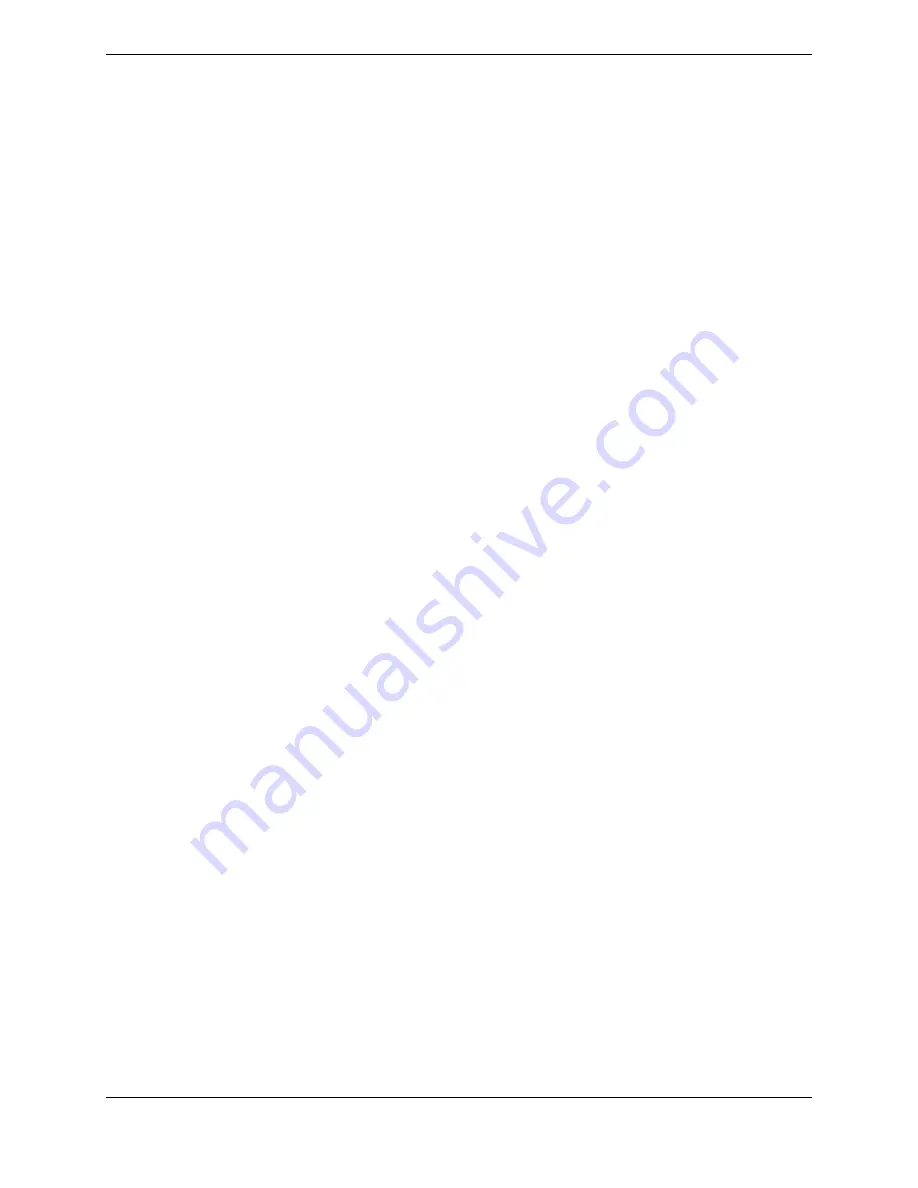
Page 3-6
GWX 68 Installation Manual
Preliminary Revision 1
190-00286-01
Secondary Method, Heat Shrink instead of Solder Sleeves:
Solder a Flat Braid (6) to the shield exposed through the window of the prepared cable assembly (4).
Ensure a solid electrical connection through the use of acceptable soldering practices. Use care to avoid
applying excessive heat that burns through the insulation of the center conductors and shorts the shield to
the signal wire. Slide a minimum 0.75” of Teflon heat shrinkable tubing (5) onto the prepared wire
assembly and shrink using a heat gun. The chosen size of heat shrinkage tubing must accommodate both
the number of conductors present in the cable and the Flat Braid (6) to be attached.
4.
At the same end of the shielded cable (4) and ahead of the previous shield termination, strip back
“Float Min” to “Float Max” (Table 3-5) length of jacket and shield to expose the insulated center
conductors. (See Figure 3-2). It may be best to build the “Ideal Float” length optimally.
Preferred Method:
The jacket and shield should be cut off at the same point so no shield is exposed. Slide 0.75” minimum of
Teflon heat shrinkable tubing (7) onto the cable and use a heat gun to shrink the tubing. The chosen size
of heat shrinkage tubing must accommodate the number of conductors present in the cable
Secondary Method:
Leave a max 0.35” of shield extending past the jacket. Fold this 0.35” of shield back over the jacket.
Slide a solder sleeve (7) over the end of the cable and use a heat gun approved for solder sleeves to secure
the connection. The chosen size of solder sleeve must accommodate the number of conductors present in
the cable.
5.
Strip back 1/8” of insulation and crimp a pin (8) to each of the conductors in the shielded cable.
6.
Insert newly crimped pins and wires into the appropriate connector housing location as specified by
the installation wiring diagrams.
7.
Cut the Flat Braid (6) to a length with the addition of a ring terminal that will reach one of the tapped
holes of the Shield Block (2). (See Figure 3-1). An appropriate amount of excess length without
looping should be given to the Flat Braid (6) to allow it to move freely with the wire bundle. Note
that the maximum distance from the backshell allowed for the window splice should keep the Flat
Braid (6) to a worst case length of approximately 4”.