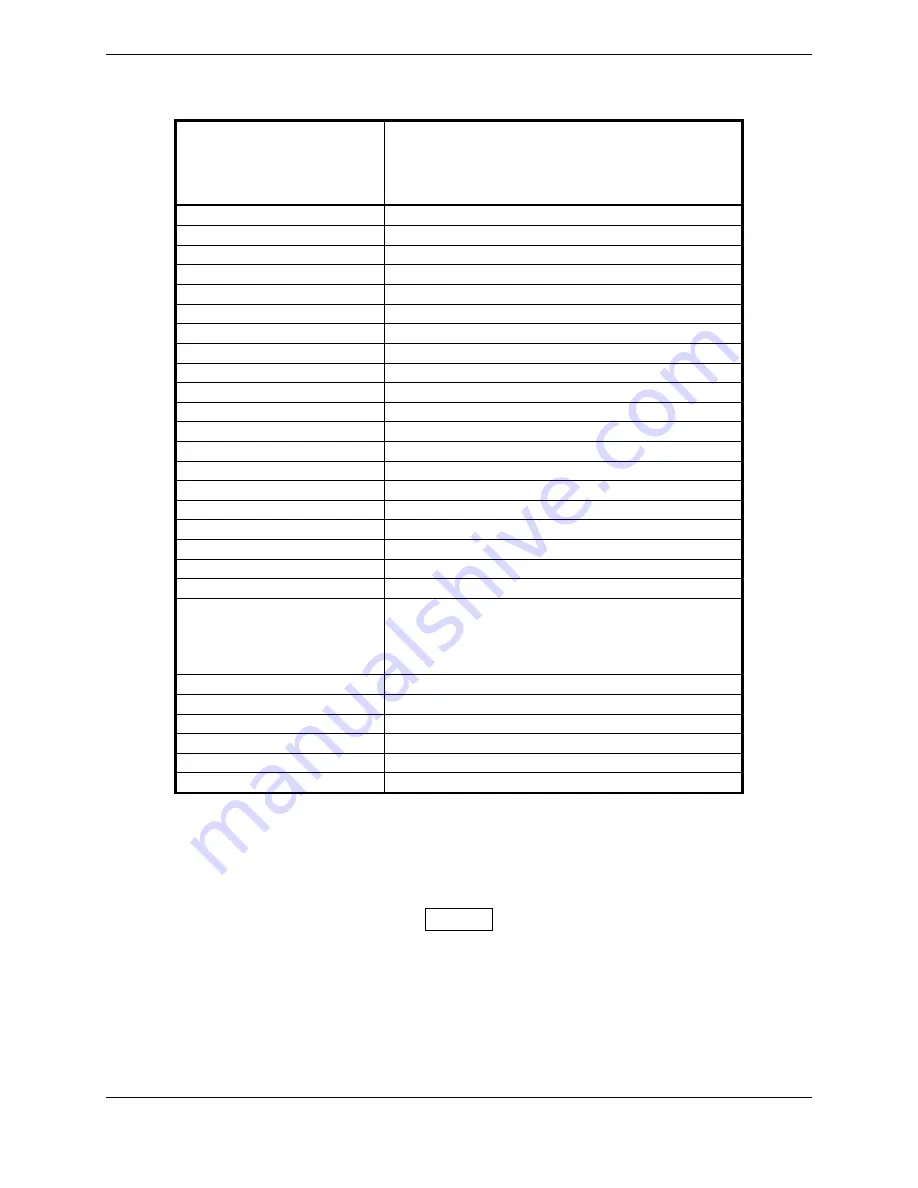
GRS 77/GMU 44 Installation Manual
Page 5-15
190-00303-10
Revision L
Table 5-3. Helicopter Magnetometer Interference Test Sequence Example
Elapsed Time
Since Start of Test
(min:secs)
A
ction
0:00
Test begins
0:20
Cyclic full right
0:30
Cyclic full left
0:40
Cyclic full forward
0:50
Cyclic full back
1:00 Cyclic
centered
1:10
Collective full negative
1:20
Collective full positive
1:30
Anti Torque full left
1:40
Anti Torque full right
1:50
Navigation lights on
2:00
Navigation lights off
2:10
Landing lights on (FWD Only)
2:20
Landing lights off (FWD Only)
2:30
Landing lights on (REAR Only)
2:40
Landing lights off (REAR Only)
2:50
Landing lights on (FWD+REAR)
3:00
Landing lights off (FWD+REAR)
3:10 Strobes
on
3:20 Strobes
off
3:30
Turn on all lights simultaneously
(typically will include navigation lights,
recognition lights and strobe)
3:40
Turn off all lights simultaneously
3:50
Pitot heat on
4:00
Pitot heat off
4:10
Air conditioning system on
4:20
Air conditioning system off
4:30
End of test
d)
When the CALIBRATE field is blinking, press the ENTER key to begin the procedure, and
have a stopwatch ready to begin recording the elapsed time.
NOTE
It is important that the “time equals zero” moment corresponds with the
moment the PFD first displays the blinking TEST COMPLETE message.
2.
The operator should carry out the actions called for in the prepared test sequence.