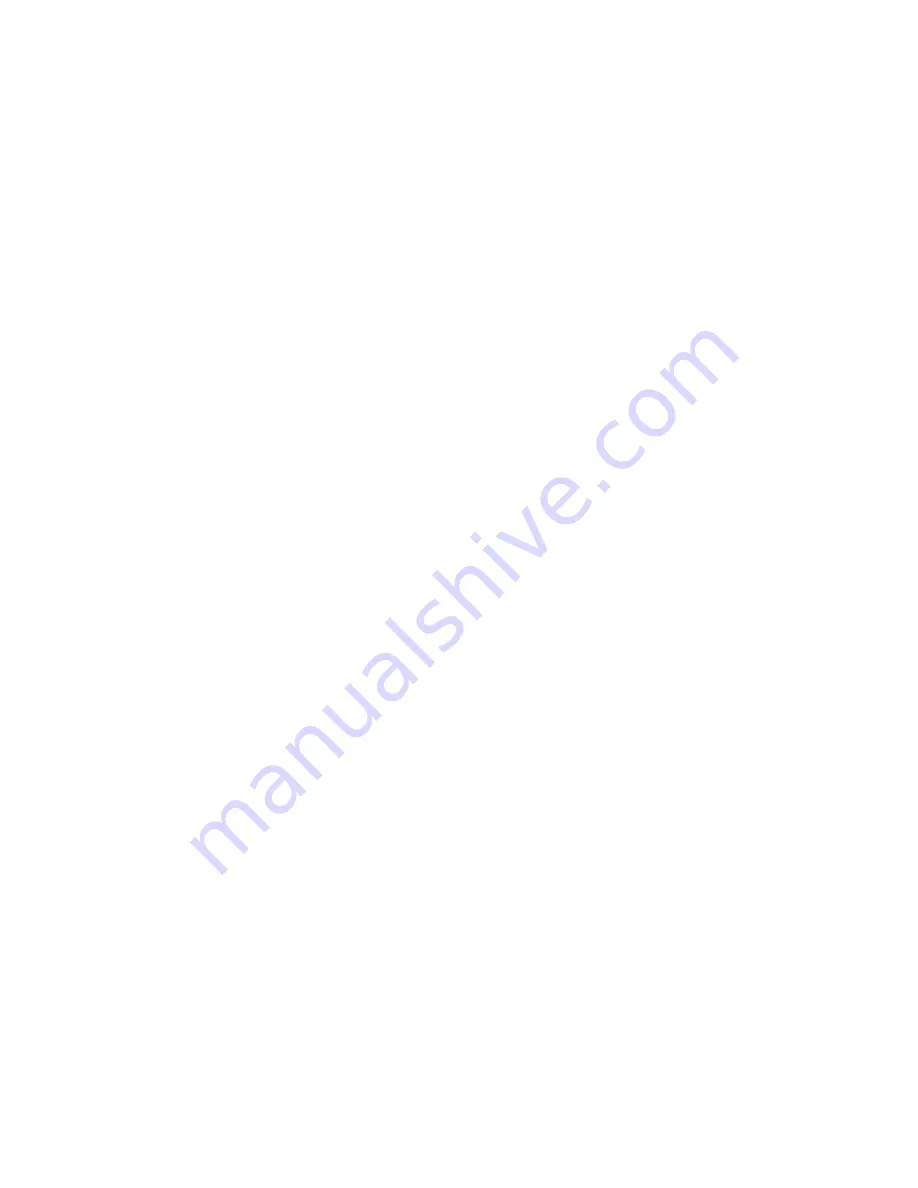
2.30 Traps
2.31 When To Use A Trap
The Self-Cleaning Dry Vacuum System is constructed of PTFE or fluorinated plastics on all wetted surfaces to
resists chemical attack from aggressive solvent, base and acid vapors. A totally oil free diaphragm mechanism
removes the need for lubricating and sealing fluids for pulling a vacuum. When pumping gases or low vapor
loads, a trap is not necessary unless you want to capture vapors evolved from the process.
When a heavy load of water or organic vapor is evolved from the vacuum process, condensation of vapor in the
pump mechanism may occur. The reason is the pump is compressing the vapor as it passes through the pump. If
the vapor is dense enough, the compression will cause condensation of the vapor in the pump mechanism. The
valve system in the pump mechanism is designed to pass the small quantity of liquefied vapor formed when
pumping heavy vapor loads. The liquid formed will be ejected from the outlet port. The self-cleaning purge
feature of the Self-Cleaning Dry Vacuum System is designed to eject condensed vapors left in the pump upon
shut-done.
The advantage of a cold trap when pumping heavy vapor loads is that it will increase the effective pumping speed
of the Self-Cleaning Dry Vacuum System. The trap acts as an additional pumping mechanism, increasing the
effective pumping speed. This higher effective pumping speed will shorten the time needed to strip solvent. The
time savings will depend on such factors as the solvent stripped, solvent temperature and operating temperature of
the cold trap.
The cold trap is installed between the pump and the vacuum chamber. The water or organic vapors evolved from
the vacuum process entering the cold trap will come in contact with the cold surfaces of the trap and condense.
Commonly used refrigerants are liquid nitrogen or dry ice with alcohol slurry. Dry ice provides sufficient
cooling to freeze out most heavy water vapor loads. A variety of cold traps are available from Welch. Contact
your closest Gardner Denver Welch Vacuum Technology sales office. See country directory on back cover,
or visit the Welch Web-Site at www.welchvacuum.com.
2.32 The Care of a Liquid Trap
A liquid trap needs no refrigerant. The key maintenance issue when pumping high vapor loads is to regularly
drain the trap of liquid ejected from the dry vacuum pump.
2.33 The Care of a Cold Trap
When using a cold trap the refrigerant should be maintained at a high level in the flask to keep the trap at a
uniformly low temperature. If the trap is rewarmed it may allow re-evaporation of the condensate. If the trap
becomes saturated it should be disconnected from the system, drained and cleaned. An increase in pressure in the
vacuum system will normally indicate that the trap has become saturated. To clean the trap, remove the trap from
the system and allow the trap to warm up and rinse off the condensate with a suitable solvent in a fume hood.
Thoroughly clean and dry the trap before reinstalling the system.
If a liquid nitrogen trap is used, the refrigerant add tube on the liquid nitrogen trap should not be obstructed as the
refrigerant boil-off can produce dangerously high pressures.
2.34 Application Note for Cold Trap
Cold traps employing a dry ice slurry or liquid nitrogen are effective as long as the refrigerant level is maintained.
If the trap warms up while the pump is running, all of the traped condensables will be ingested by the vacuum
pump. Cold traps must be cleaned out at the end of each day. If the pump is run overnight, the trapped
condensables will ultimately be ingested by the pump as the trap warms up. Cleaning a Dry Ice Slurry/Liquid
Nitrogen trap is easy. The steps are:
1. Turn off the pump.
2. Leak air into the trap.
3. Remove the center well and plexiglas ring to a hood. The center well can be washed off into a
beaker or the condensables can be allowed to evaporate in the hood.
10
Artisan Technology Group - Quality Instrumentation ... Guaranteed | (888) 88-SOURCE | www.artisantg.com