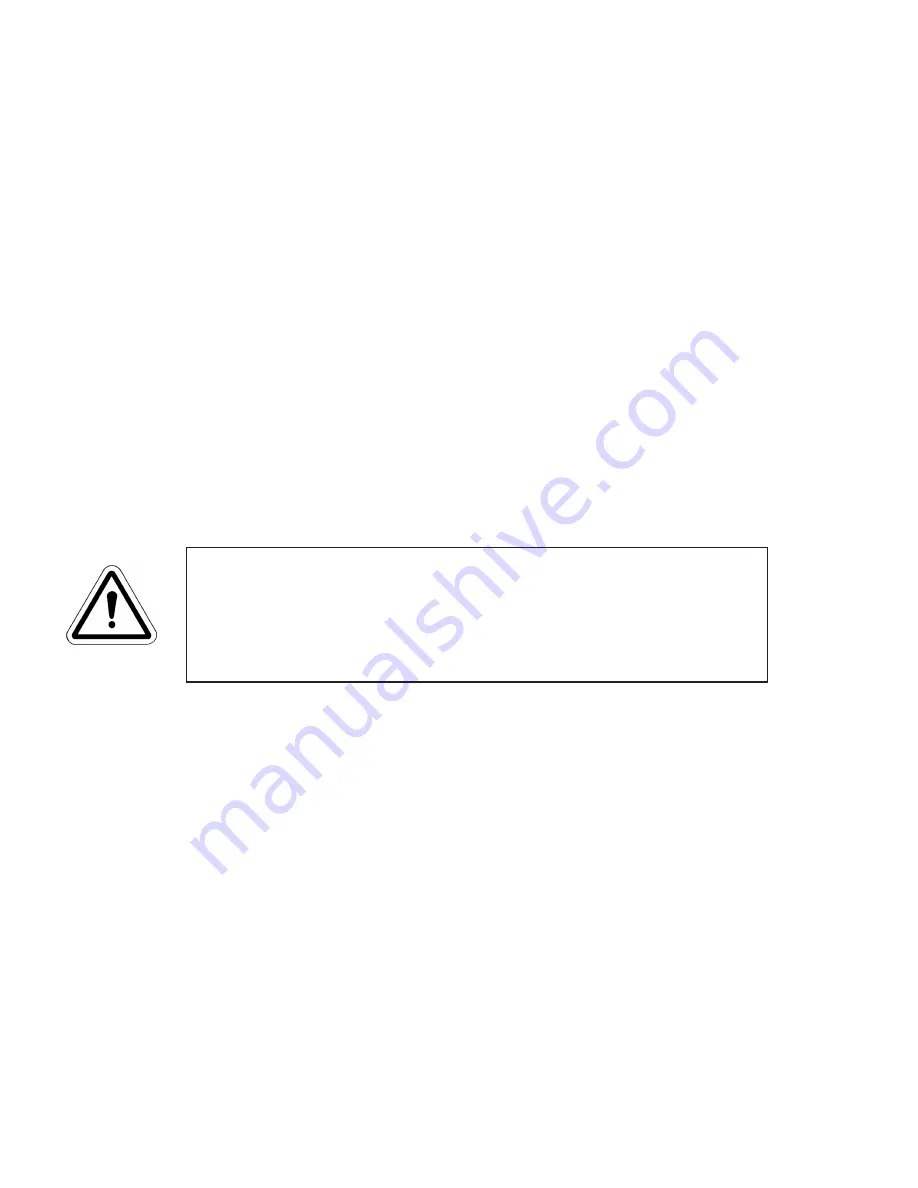
9
WARNING
Solvents, such as acetone, used to clean different pumps
are extremely hazardous. Inhalation may be fatal
or harmful. Acetone is also extremely flammable.
Never use acetone near heat or open flame.
Use only in a well ventilated area.
3.20 Oil Changes and Oil Level
3.201 Developing a Maintenance Schedule
After studying many examples of pump failure, Welch has found the most common reason is poor condition of
the oil. This is why a regular maintenance schedule for the oil is critical to obtain the longest service life out of
your DUOSEAL pump. Welch recommends that you examine the condition of the oil on a daily basis in the early
days of a new process or experiment. You want to look for discoloration of the oil and whether the oil level is
rising. The discoloration can indicate deterioration of the oil and a rising oil level can indicate condensation of
vapors is occurring in the pump. When changes occur, the oil needs to be change. If no changes in the oil level
or color are observed, extended pump service life is obtained if the oil is changed every three to four months.
3.202 Forced Oil Flushing
When you drain oil through the drain valve, you are not removing the oil and contaminants that are inside the
pumping mechanism. You are removing oil only from the oil case. Welch recommends a forced oil flush of
DUOSEAL pumps be performed at the regular maintenance oil change.
The procedure for the forced oil flush is given below.
Section 3: MAINTENANCE
3.10 Vacuum Problems
3.101 Pressure Determinations
Leakage, contamination and unusual outgassing are the general causes of problems associated with poor vacuum.
To operate at maximum efficiency a system must be thoroughly clean. If the system is completely clean and free
from leaks, and unwarranted vacuum problems still exist, the pump should be checked. A simple criterion for the
condition of a mechanical pump is a determination of its ultimate pressure capability. This can be accomplished
by attaching a gauge directly to the pump. The gauge may be any suitable type provided consideration if given
to the limitations of the gauge being used. Refer to Paragraph 1-8 for further suggestions. If the pressure is
unusually high, the pump may be badly contaminated, low on oil or malfunctioning. On the other hand, if the
pressure is only slightly higher than the guaranteed pressure of the pump, an oil change may be all that is required.
3.102 Oil Contamination
The most common cause of a loss in efficiency in a mechanical pump is contamination of oil. It is caused by
condensation of vapors and by foreign particles. The undesirable condensate emulsifies with the oil which is
recirculated and subject to re-evaporation during the normal cycle of pump activity thus reducing the ultimate
vacuum attainable. Some foreign particles and vapors may form a sludge with the oil, impair sealing and
lubrication and cause eventual seizure. A gas ballast calve is helpful in removing vapors, especially water, but it
is not equally effective on all foreign substances; therefore, periodic oil changes are necessary to maintain
efficient operation of the system. The required frequency of changes will vary with the particular system,.
Experiences with the process will help you determine the normal period of operation before an
oil change is required.
3.103 Oil Overheating
This pump is designed to operate continuously below 10 Torr. Continuous operation of this pump above 10 Torr
will lead to overheating and eventual pump failure. See Section 2.21, High Pressure Operation.