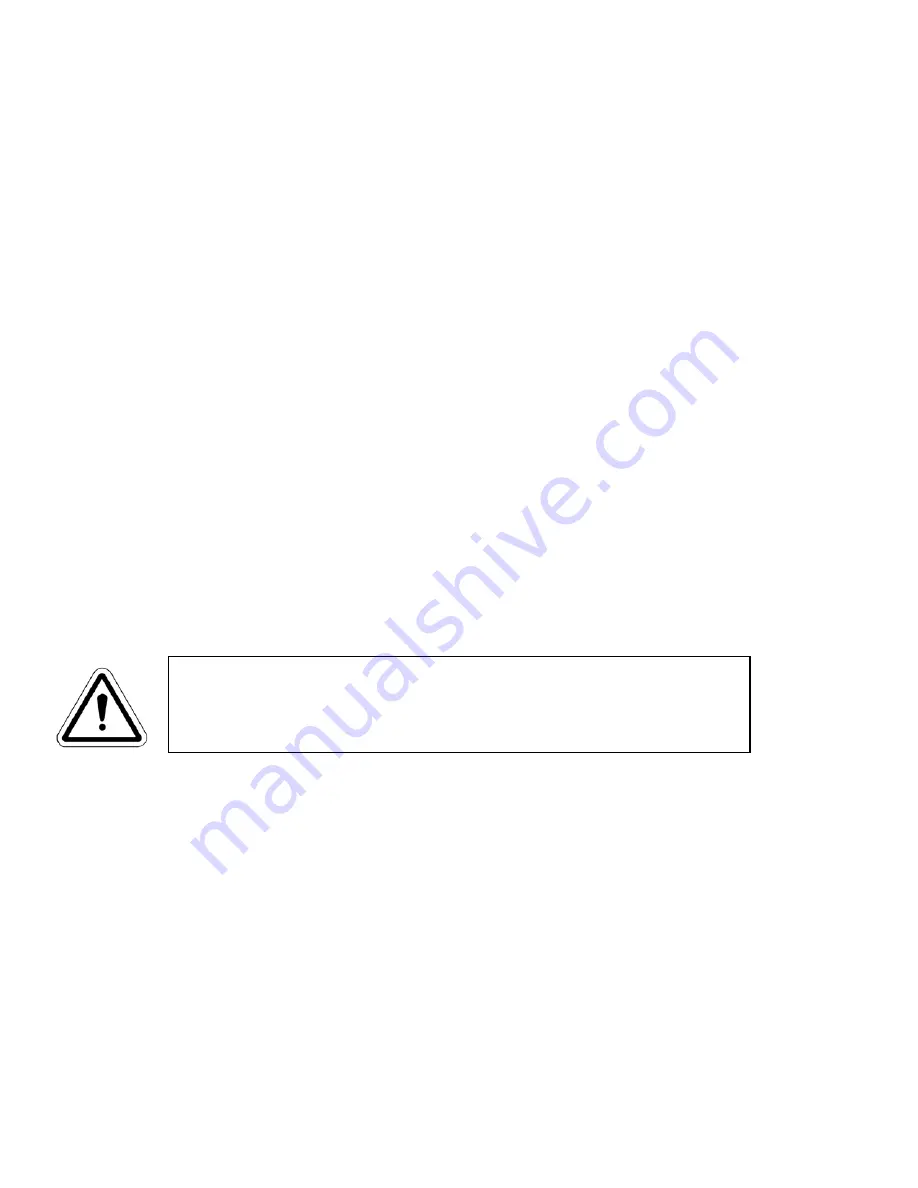
6
1.17 Traps (See Accessory section in the back of this manual.)
1.171 The need for a Trap
Where corrosive vapors or large quantities of condensable vapors are evolved from vacuum processing, a cold
trap may be used in the connecting line to the pump. It will help prevent damage to the pump mechanism and
reduce oil contamination. The cold trap, immersed in a suitable Dewar flask, is installed to that the vapors may
come in contact with the surfaces of the trap and condense. Commonly used refrigerants are liquid nitrogen or
dry ice and acetone. The refrigerant to be used depends upon the freezing point of the contaminations. A variety
of cold traps are available from Welch Vacuum, Thomas Industries, inc.
1.172 The care of a Trap
When using a cold trap the refrigerant should be maintained at a high level in the flask to keep the trap at a
uniformly low temperature. If the trap is re-warmed it may allow re-evaporation of the condensate. The
refrigerant add tube on the liquid nitrogen trap should not be obstructed as the refrigerant boil-off can produce
dangerously high pressures. If the trap becomes saturated it should be disconnected from the system, drained and
cleaned. An increase in pressure in the vacuum system will normally indicate that the trap has become saturated.
To clean the trap, remove the trap from the system, allow the trap to warm up and rinse off the condensate with a
suitable solvent in a fume hood. Thoroughly clean and dry the trap before reinstalling in the system.
Section 2: OPERATION
2.10 Starting Procedures
2.101 Starting a DUOSEAL Pump
Before attaching the pump to a system it is well to familiarize yourself with the function and action of the pump
which you have now required.Remove the intake and exhaust port plugs and temporarily provide a stopper for
the intake and a dust cap for the exhaustReview the power requirements as described in Section 1.4.
2.103 Cleanliness
Take every precaution to prevent foreign from entering the pump. A fine mesh screen is provided for this
purpose in the intake passage of all DUOSEAL pumps.
2.104 Oil Level Determination
The amount of oil suitable for efficient and satisfactory performance should be determined after the pump has
reached its operating temperature. Initially, however, the pump should be filled with fresh oil while the pump is
idle. Fill the pump until the oil level falls half way of the oil level window. If after a short period of operation the
level should fall, it is likely the result of oil entering some of the interior pockets of the pump. If the oil level
rises, this signifies oil has drained into the pump cavity while pump was idle. Shut off pump, then drain oil down
to proper level.
If a gurgling sound occurs, additional oil must be added. Mechanical pumps will gurgle in varying degrees under
four conditions of performance: [a] when operating at high pressure as in the beginning cycles of evacuation of a
chamber; [b] when the oil level in the pump reservoir is lower than required; [c] when a large leak is present in
the system; and [d] when the gas ballast is open. Awareness of the possibilities will save time in setting up a
system. Best performance of a mechanical pump is generally obtained after sufficient time has been allowed for
the pump to come to operating temperature.
CAUTION
Do not run this pump with the intake open directly to
the atmosphere. The pump will overheat, excessive oil mist will
be emitted from the exhaust and the pump will eventually seize.