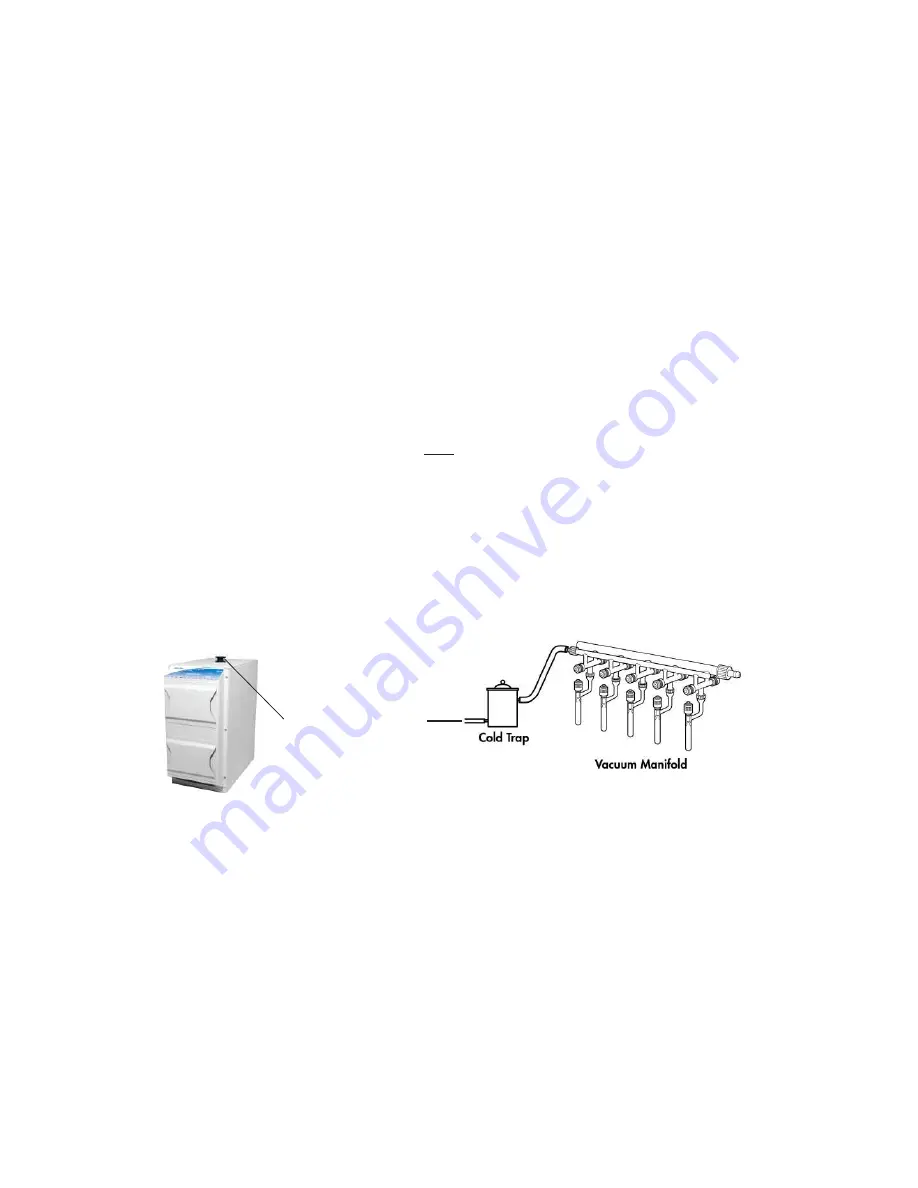
8
Section 3: OPERATION
3.10 Starting
Before attaching the pump to a system it is well to familiarize yourself with the function
and action of the pressure vacuum pump which you have acquired. Review the power
requirements as described in Section 2.16. Welch recommends running the pump for a few
minutes to warm it up before use. The warm-up improves the pumps ability to pass water and
organic vapor. A warm pump will handle more vapor without liquefying it than a cold pump.
3.11 Cleanliness
Take every precaution to prevent foreign particulates, liquid and harmful vapors from entering
the pump. Ingestion of particulates and liquid can damage the pump. A simple trap can be
made out of a fi ltering fl ask placed between the pump and the vacuum chamber. The use of
a cold trap is also recommended to maintain effi
cient vacuum performance and for removing
harmful condensable vapors.
Do not use fl exible PVC hose or silicone rubber hose for vacuum connections when pumping
on organic solvent vapors. Solvent such as Methylene Chloride (DCM) eff ectively leaches out
plasticizers from the PVC and silicone hose which carry over to the vacuum pump causing
contamination and vacuum mechanism failure. Using natural thick walled gum rubber vacuum
hose gives better resistance to organic solvents such as Methylene Chloride (DCM) and
protects vacuum pump against early failure.
Use of a cold trap recommended on applications with high vapor loads such as;
•
Flash Evaporation
•
Concentrators
•
Processing Natural Plant Extracted Oils
.
To system intake
Chemstar Dry
3.12 Leak Detection
Eliminating all leaks in a vacuum system is a key to obtaining maximum vacuum. The pump
must remove this added volume of leaked gas to maintain the desired vacuum. Leaks can be
located by slightly pressuring the system and painting the suspected area with a thick soap
solution. Escaping air will produce soap bubbles.
3.13 Operating Pressure Range
Vacuum pumps are designed to be run from slightly below atmospheric to their maximum
vacuum level on the intake side. Consult the Specifi cation Table in the back of this manual for
the ratings for your specifi c model.