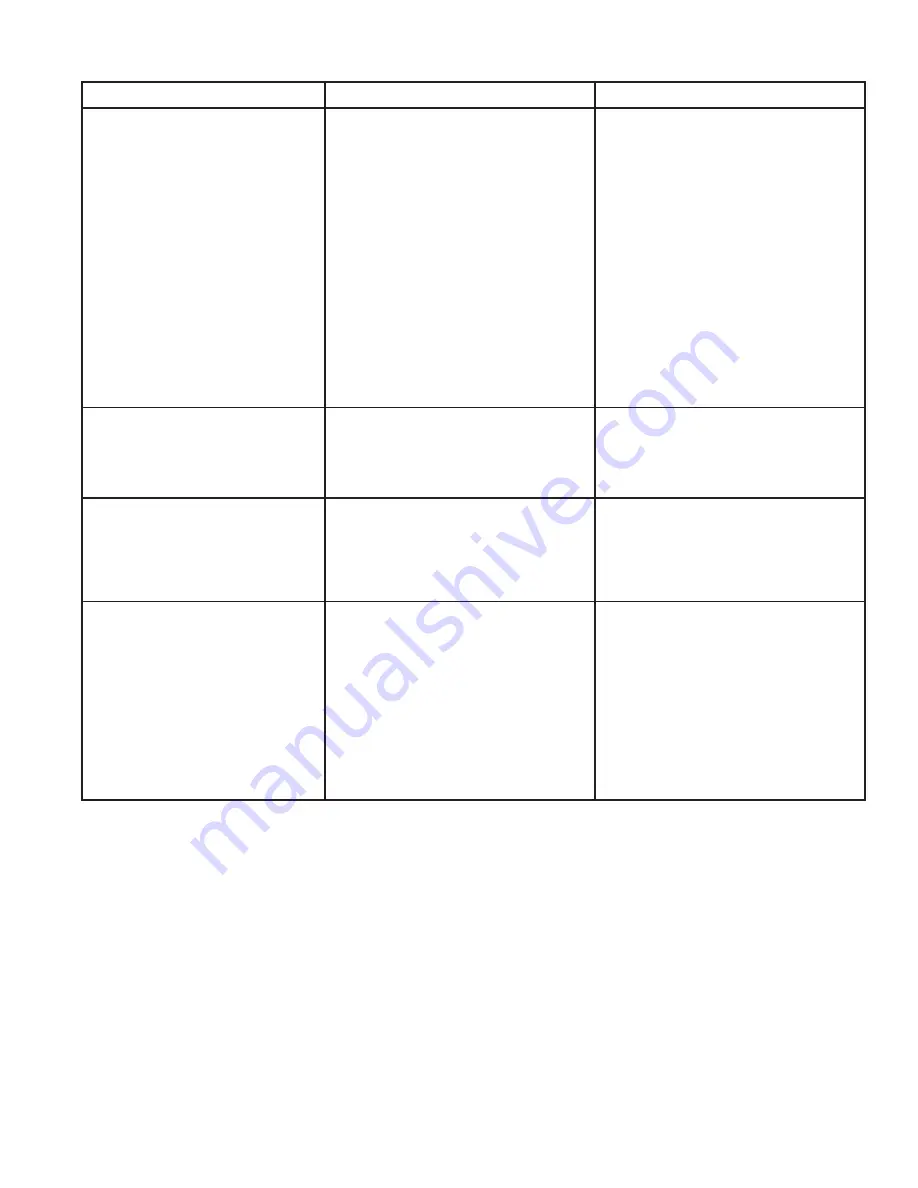
19
TROUBLESHOOTING GUIDE
SYMPTOM
POSSIBLE CAUSE(S)
CORRECTIVE ACTION
A) Water downstream of dryer.
1. Residual free moisture remaining in
downstream pipelines.
2. Air bypass system is open.
3. Inlet and Outlet connections are reversed.
4. Temperatures surrounding air lines
downstream of dryer have dropped below
dryers dew point rating.
5. Excessive free moisture (bulk liquid) at dryer
inlet.
6. Condensate not being automatically drained
Drain mechanism is clogged or inoperative.
Drain line is restricted or frozen.
Electric drains-timer not set to allow for
sufficient condensate removal.
7. Dryer overloaded resulting in elevated dew
point.
8. Refrigeration system not functioning.
Blow out system with dry air.
Check valve positions.
Check for correct connection.
Insulate or heat trace air lines exposed to low
ambients or dry air to lower dew point.
Install separator ahead of dryer.
Replace drain mechanism if inoperative.
Open drain line.
Electric drains-reset time so that all liquid is
discharged.
Check inlet air temperature and pressure, flow
rate (compressor capacity) and ambient air or
water temperature.
See D below.
B) High pressure drop across dryer.
1. Excessive air flow.
2. Freezing of moisture in evaporator because
of refrigeration system fault.
3. Separator or optional Oil Removal filter
element clogged.
Check flow rate.
See D below.
Replace filter element(s).
C) Dew point indicator in red area.
1. Dryer overloaded resulting in high air outlet
temperature.
2. Refrigeration system not functioning
properly resulting in high air outlet
temperature.
3. Dryer is running with no load.
See A 7.
See D below.
Light will go out when air flow is established.
D) Refrigeration system not
functioning properly.
1. Power on light off.
2. Compressor on light off.
3. Refrigeration compressor cycles on
and off.
a. Power failure.
a. ON/OFF switch is “OFF”.
b. Line disconnect switch open.
c. Blown fuses, open breaker.
d. Faulty wiring, loose terminals.
a. High or low ambient conditions.
b. Air-cooled models - Dirty, clogged
condenser fins, obstructed air flow across
condenser, or non functioning fan motor or
fan control switch.
Check power to unit.
Turn switch “ON”.
Close disconnect switch.
Check for continuity.
Have electrician check electrical connections.
Check min./max. temperature ranges.
Clean condenser and check for free air flow, if
problem persists contact qualified refrigeration
repairman or manufacturer’s service
department.
Summary of Contents for RNC Series
Page 22: ...22 NOTES...
Page 23: ...23 NOTES...