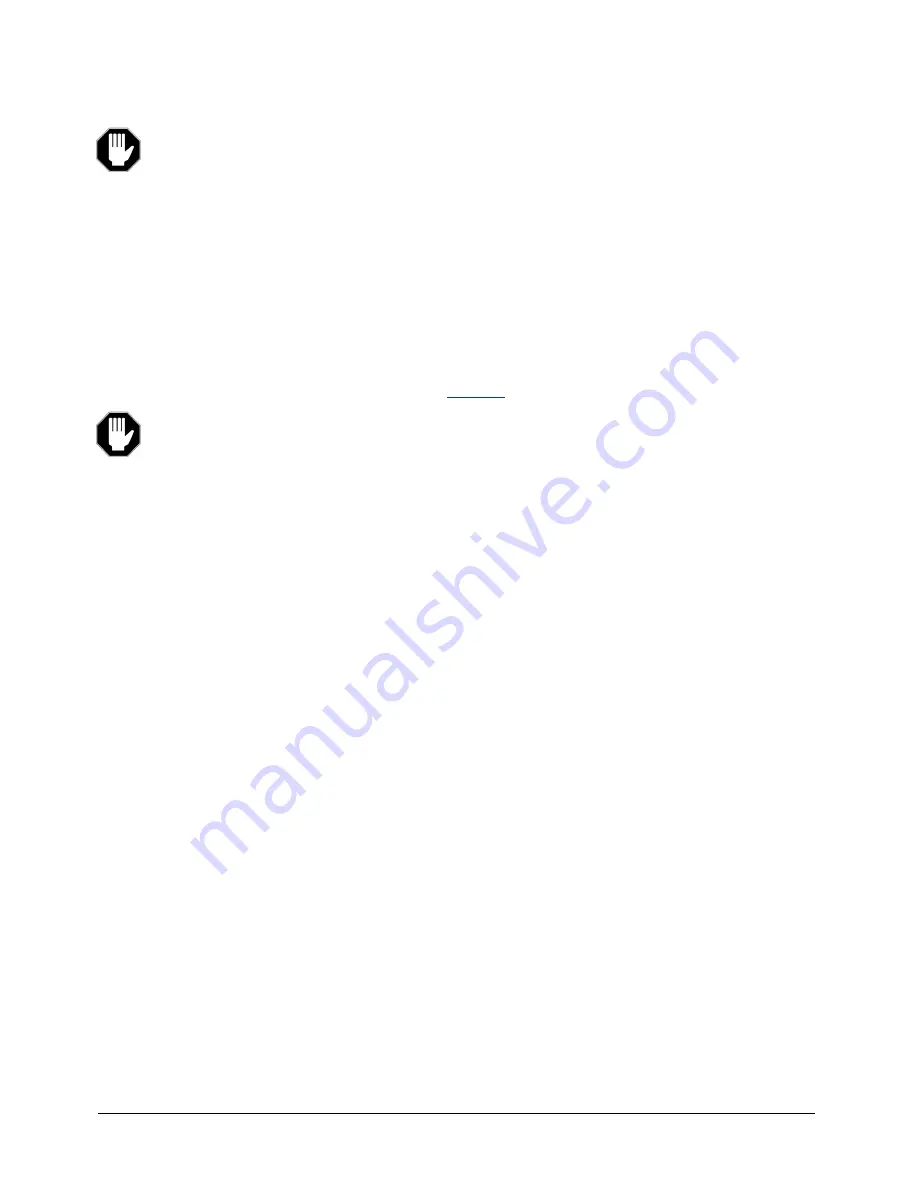
RFL-7-500 Page 23
7.4
Precautions for Long Standstill Periods
•
Clean the machine thoroughly.
If the machine is cleaned with a high pressure jet wash, there is a danger of water intrusion.
•
After wet cleaning, allow the machine to warm up for a few minutes to prevent the rotor vanes from sticking.
If the stoppage of the compressor/vacuum pump installed on the vehicle lasts longer than one month, we recommend operating
the machine for at least 15 minutes once a month. This ensures that all parts subject to corrosion are supplied with fresh oil.
7.5
Rinsing After Machine was Over-sucked
After over sucking (liquids or mud have come into the machine) proceed as follows:
•
Remove screws in the inlet flange,
•
Open the vehicle tank, so the machine can be operated without vacuum or pressure,
•
Switch machine on and with slightly reduced speed, put approximately half a litre of diesel into the inlet port,
•
Switch off the machine, perform pre-lubrication according to
section 6.2
before restarting the machine.
Turning the reverse flow valve partially is not allowed during the rinsing. The dirt leaving the machine through the
discharge port could get into the suction side again.
7.6
Procedure if Faults Occur
If a malfunction occurs, the following table may provide the cause and solution to the problem.
Fault
Possible cause
Elimination
Volume flow performance of
compressor/vacuum pump deteriorates
•
Vacuum filter or combination
filter contaminated
•
Clean filter, if necessary replace
filter element
•
Leaking suction pipe
•
Find and seal leaks
•
Leaking fittings
•
Replace fittings
•
Rotation speed too low
•
Adhere to range of rotation
speed
•
Worn rotor vanes; perhaps
contamination (water, dirt, etc.)
has got into the machine (e.g.
by excess suction)
•
Replace rotor vanes or have
machine overhauled in
authorised repair workshop
Abnormal noise level
•
Machine is poorly aligned
•
Align machine
•
Worn bearing
•
Replace bearing/have bearing
replaced
•
Insufficient lubricating oil
•
Add oil, clean oil tank and intake
filter
•
Incorrect lubricating oil
•
Add oil according to section 6.7
•
Rotor vanes knock due to lateral
wear
•
Replace rotor vanes
•
Machine bore has scores or
undulations due to intake of dirt
•
Have machine bore rebored and
honed in an authorised repair
shop - Install a fine filter if
suction air is highly
contaminated
•
Incorrect rotor speed
•
Adhere to rotation speed limits
•
Altered pressure
•
Adhere to nominal pressure
•
Altered vacuum
•
Adhere to nominal
vacuum/check exhaust system
and clean if necessary
•
Foreign object in the machine
•
Remove foreign object
immediately and flush the
machine
•
Rotor contact
•
Stop and repair the machine
Summary of Contents for RFL 102
Page 1: ...PD BLOWERS VACUUM PUMPS RFL SERIES Owner s Manual RFL 102 RFL 7 500 Version 03 April 11 2018...
Page 33: ...NOTES...
Page 34: ...NOTES...
Page 35: ...NOTES...
Page 36: ......