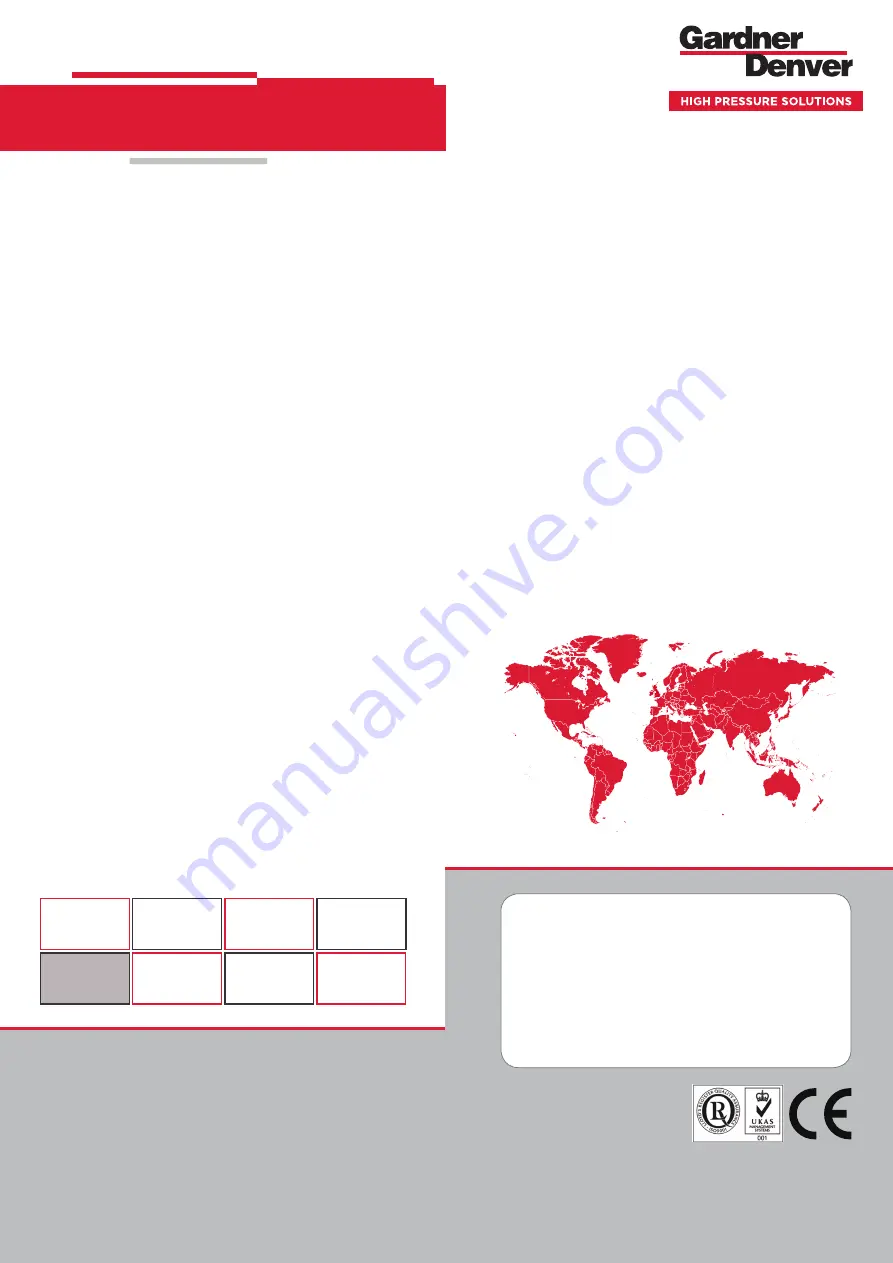
Contact us today:
Gardner Denver Ltd
Claybrook Drive, Redditch, Worcestershire, B98 0DS, UK
T: +44 (0) 1527 838 600, F: +44 (0) 1527 838 630
W: www.gdhighpressure.com
For additional information please contact
Gardner Denver or your local representative.
Specifications subject to change without notice.
Copyright 2017 Gardner Denver.
G7 75GB
BREATHING AIR
CNG + BIOGAS
BREATHING GAS
ENGINE START
INDUSTRIAL
AIR + GAS
OFFSHORE
DEFENCE
NITROGEN
BOOSTING
GARDNER DENVER REAVELL OFFER SOLUTIONS FOR:
Perfect With Pressure
Compact, maintainable, and designed for
integration. Perfect your start with Reavell
Compact Footprint
•
Best in class footprint and weight per
compressor flowrate
•
Greater air output from a 25% smaller
footprint than the closest competitor
Maximum Uptime
•
Easy maintenance built in
•
Single tool valve replacement
Industry Leading Expertise
•
ATEX certified, 3.1 Material certificates,
operation below 0
o
C ambient
•
Market leading 1,500 hour service intervals
Specialist Support
•
Bespoke training packages
The Perfect Start
Compact Air Start Compressors
Designed for Integration
Single Source Solutions
For more than 155 years, Gardner Denver has been a
leading global provider of compressors, blowers and
vacuum pumps. OEMs and end-users from every corner
of the world rely on us for their business solutions.
With global teamwork, strong customer focus, and vast
application knowledge, our brands provide reliable,
energy-efficient products that serve a wide range of
manufacturing and process industries.
Summary of Contents for Reavell 5236
Page 2: ......
Page 4: ......
Page 6: ......
Page 7: ...Section 1 General Information...
Page 8: ......
Page 21: ...Section 2 Compressor...
Page 22: ......
Page 36: ...P a g e 8 INTENTIONALLY BLANK...
Page 40: ...P a g e 12 INTENTIONALLY BLANK...
Page 44: ...P a g e 16 INTENTIONALLY BLANK...
Page 52: ...P a g e 24 INTENTIONALLY BLANK...
Page 62: ...P a g e 34 INTENTIONALLY BLANK...
Page 64: ...P a g e 36 INTENTIONALLY BLANK...
Page 65: ...P a g e 37 5236 MK2 COMPRESSOR V14 0 En 10 APPENDIX...
Page 67: ...REMARKS DATE REMARKS DATE...
Page 71: ......
Page 73: ...Section 3 Drawings...
Page 74: ......
Page 77: ......
Page 78: ......
Page 79: ...Section 4 Motor...
Page 80: ......
Page 86: ......
Page 87: ...Section 5 Starter Control...
Page 88: ......
Page 95: ...Section 6 Equipment Data Sheets APPs...
Page 96: ......
Page 133: ......