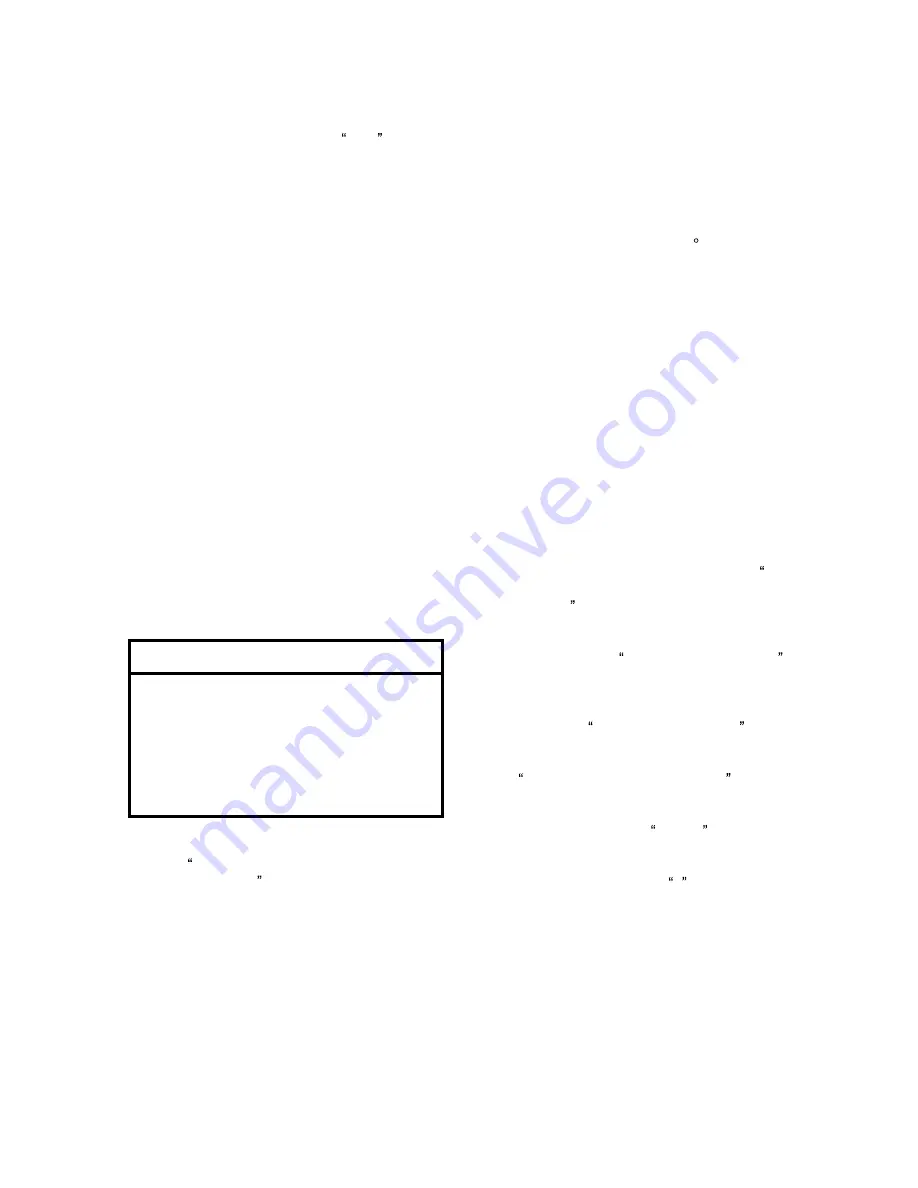
300FWF996 Page 26
Crosshead Guide and Stay Rods
1.
The crosshead guides or slide should
be replaced if excessively worn or
damaged. (See CLEARANCES pg. 35)
2.
If the crosshead guides must be
replaced, it is recommended that it be
done either by Gardner Denver or a
qualified machine shop.
3.
The stay rods are threaded into the
power frame.
They can be easily
replaced by unscrewing and re-torquing
new rods. (See Torque on pg. 36)
4.
Typically, when failures of stay rods do
occur, it is one of the outermost four.
5.
Check all stay rods for proper torque,
plus check for broken or cracked
threads.
6.
The stay rods need to be torqued to the
values shown on page 36 when they
are installed in the power end, as well
as when the nuts are torqued after
installing the fluid end.
Gear Reduction Components
NOTICE
This assembly is a timed gear set,
and should be changed as a gear set.
If one gear is changed, both should
be changed.
If one gear only is
changed, the gears must be timed.
This can be done with offset keys.
1.
Remove the gear covers as described
in Oil Stop Head Seal Retainer and
Gear Covers, page 24.
2.
Cut the safety wire (if used) and
remove the four screws.
3.
Remove the set screws on the square
keys and pull with puller.
4.
Connect a sling and overhead to one
gear. Pull gear off and lay on side for
safekeeping. Remove second gear.
5.
Remove capscrews retaining pinion
bearing housings.
Using jackscrew
holes, remove one housing.
6.
With one pinion bearing housing
removed, pull the corresponding pinion
bearing from the pinion, as the bearing
will not pass through the frame. Local
heat may (approx. 200 F) may be
required to remove the bearing from
the pinion.
7.
Pinion and other housing may now be
removed with the aid of a lift.
Crankshaft Assembly
1.
Remove the pump from the trailer and
move it to service area. (The pump
service area must have overhead-lift
capability.) Power end must be level.
2.
Remove the fluid end as described in
"Fluid End Removal and Installation,"
page 21.
3.
Remove the oil stop head seal retainer
and gear covers as described in Oil
Stop Head Seal Retainer and Gear
Covers, page 24.
4.
Remove the crosshead assemblies as
described in Crosshead Assembly,
page 25.
5.
Remove the connecting rods as
described Crosshead Assembly.
6.
Remove the bull gears as described in
Gear Reduction Components, on this
page.
7.
For best results, a special crankshaft
handling tool should be fabricated to fit
one of the crankshaft bosses where the
keyway is cut. This L shaped lifting
tool should come up and over the top
of the pump, out to the centerline for
easy, balanced lifting of the crankshaft.
This tool must be capable of lifting the
crankshaft in a horizontal position.
8.
From one end of the crankshaft,
remove the main bearing snap ring
from the outer groove cut in the frame.
9.
Using a bearing puller, remove the
outer main bearing race from the
frame. Local heat may be required to
HALLIBURTON EXHIBIT 1013, Page 32