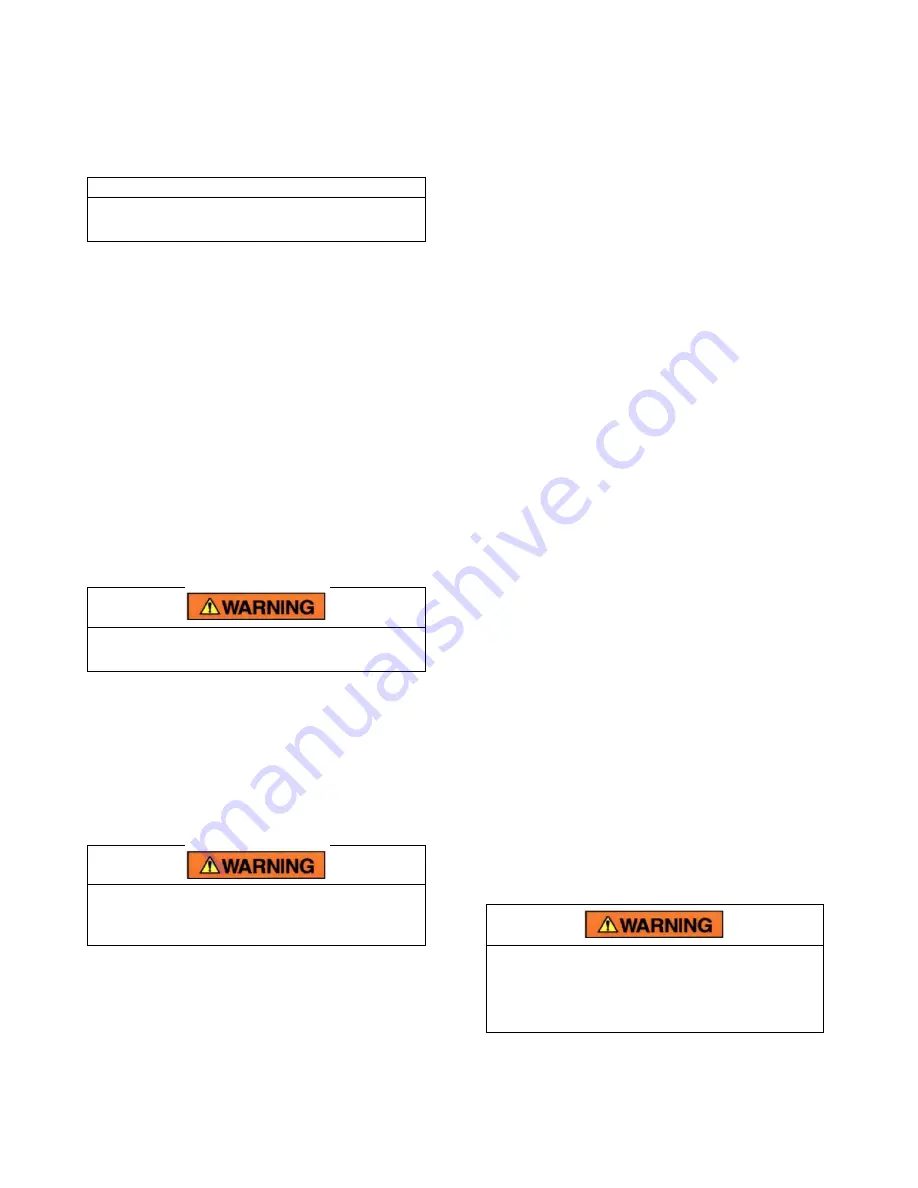
SB-7-622 Page 11
4. Secure the mounting feet capscrews to the torque
value in Figure 7-8, page 34.
NOTICE
Over tightening belts leads to heavy bearing
loads and premature failure.
NOTICE When changing mounting configuration, it
may be necessary to reposition vent plug (B), and
drain plug (A). Refer to Figure 3-1, page 17, for
correct location.
DRIVE INSTALLATION
When selecting a V-belt drive, check to be sure the
shaft overhung load limitation is not exceeded. Refer to
FIGURE 2- 2
, page 13, for overhung load calculations
and limitations.
Belt drives must be carefully aligned. Motor and blower
pulleys must be parallel to each other and in the same
plane within 1/32 inch. Belt tension should be carefully
adjusted to the belt manufacturer
’s recommendation
using a belt tension gauge. Check tension frequently
during the first day of operation.
Over tightening belts leads to heavy bearing
loads and premature failure.
On the direct connected units, alignment and lubrication
of couplings to specifications of the coupling
manufacturer is very important. When mounted drives
are supplied from the factory proper alignment has
been established before shipment. However, during
shipping, handling and installation, it is likely that the
alignment has been disturbed and final adjustment
must be made before startup.
Exceeding overhung load limitations leads
to unwarrantable premature bearing failure
and shaft breakage.
The location of the sheave on the blower shaft greatly
affects the stress in the shaft. The optimum blower
sheave positioning is as close as possible to the blower
drive cover, not to exceed dimension
“C” in Drive Shaft
Illustration, FIGURE 2-
2
, page 13
The calculated shaft moment must not exceed the
maximum allowable moment listed in Maximum
Allowable Moment Chart, FIGURE 2-
2
page 13. If the
calculated shaft moment exceed the maximum
allowable moment:
·
Increase Sheave Diameters to Reduce Belt Pull
·
Use Jackshaft Drive
·
Use Direct Coupled or Gearbox Drive
To calculate shaft moment for a given V-Belt Drive
Arrangement:
1. Use the formula for Calculation of Belt Pull,
FIGURE 2-
2
, page 13, to calculate belt pull. Refer
to Arc of Contact Factor Chart, Figure 2-2, page 15.
2. Insert the calculated belt pull into the formula for
Calculation of Shaft Moment, FIGURE 2-
2
,
page 13 to arrive at the calculated shaft moment.
PIPING
Inlet and discharge connections on all blowers are large
enough to handle maximum volume with minimum
friction loss. Reducing the pipe diameter on either inlet
or discharge will only create additional line loss and
increase the overall pressure differential.
Excessive weight of piping and fittings will cause
internal misalignment and premature wear. Never allow
the blower to carry the weight of the pipe. If possible, a
spool or sleeve-type expansion joint should be installed
between the unit and the piping. Where a flexible
connection is not practical, the weight of the rigid
connection must be separately supported.
All system piping must be cleaned internally before
connecting to the blower.
Sutorbilt blowers are shipped dry from the
factory. Do not attempt to operate the
blower before following proper lubrication
instructions. Permanent damage to the
gears, bearings and seals will occur.
Summary of Contents for GAF P Series
Page 19: ...SB 7 622 Page 18 SECTION 5 MAINTENANCE FIGURE 5 1 PULLER PLATE SK2154...
Page 20: ...SB 7 622 Page 19 FIGURE 5 2 GEAR DRIVEN SK2150...
Page 21: ...SB 7 622 Page 20 FIGURE 5 3 MECHANICAL SEAL INSTALLATION TOOL SK2152...
Page 22: ...SB 7 622 Page 21 FIGURE 5 1 BEARING PRESS TOOL MECHANCIAL SEAL UNITS SK2156 FIGURE 5 4...
Page 33: ...SB 7 622 Page 32 SECTION 8 PARTS LIST 300GAF810 B Ref Drawing...
Page 35: ...SB 7 622 Page 34 300GAG810 A Ref Drawing...
Page 37: ...SB 7 622 Page 36 300GAH810 A Ref Drawing...
Page 39: ...SB 7 622 Page 38...