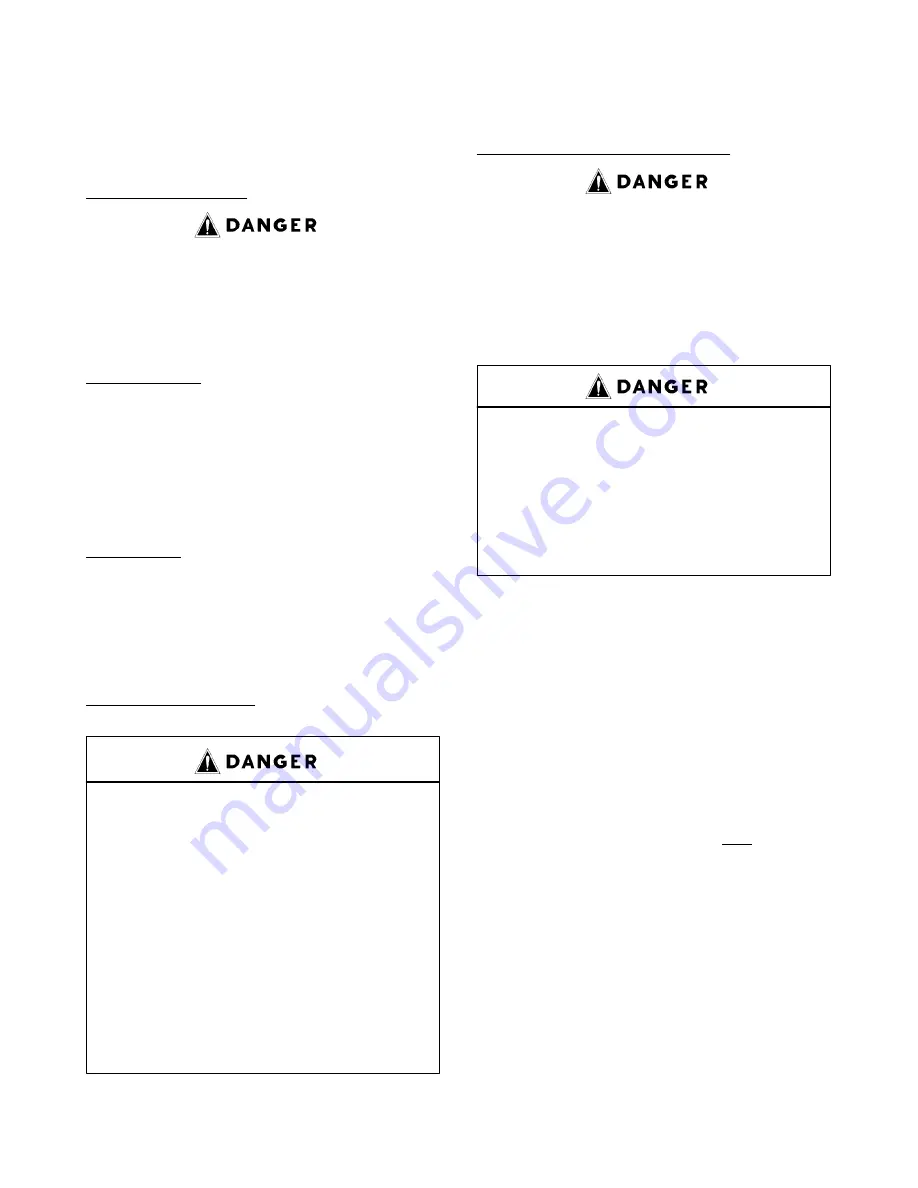
3–600 Page 2
S
Carefully swing the hammer to avoid striking
themselves, another person and objects other
than the targeted lugs or hammer bar.
S
Avoid swinging the hammer above shoulder
height.
VALVE SEAT PULLING
The following precautions must be observed by opera-
tors and maintenance personnel to avoid personal inju-
ry, death and/or equipment damage from contact with
the puller, hammer, wedge or broken parts from these
components when using either a hydraulic or wedge
valve seat puller:
Hydraulic Puller
S
Wear safety shoes and goggles.
S
Chain or tie the jack down as it will jump violently
when the valve seat disengages from the valve
deck.
S
Check to insure the pressure applied by the hy-
draulic pump does not exceed the hydraulic
ram maximum pressure rating.
Wedge Puller
S
Grind off any mushroomed material from the
wedge before use.
S
Follow the danger notices listed above in the
hammer lug section, but substitute the term
wedge for hammer lug and hammer bar.
COVERS AND GUARDS
All pump covers must be securely
fastened in proper position at all
times when the pump is operating to
avoid personal injury or death from
moving parts. In addition, all moving
parts on the entire pump package, in-
cluding but not limited to engine or
motors, drive shafts, belts, chains,
pulleys, gears, etc., must be equipped
with guards or covers, which must
also be securely fastened in proper
position at all times when the equip-
ment is operating.
Covers and guards are intended to not only protect
against personal injury or death, but to also protect the
equipment from damage from foreign objects.
EQUIPMENT MOVING AND LIFTING
Heavy equipment including pumps, pump package
units and components should only be moved or lifted
by trained, experienced operators, who are physically
and mentally prepared to devote full attention and alert-
ness to the moving and lifting operations. An operator
should be fully aware of the use, capabilities, and
condition of both the equipment being moved and the
equipment being used to move it.
Failure to follow safe and proper
pump, pump package or component
lifting or moving procedures can lead
to personal injury, death and/or
equipment damage from shifting, fal-
ling or other unexpected or uncon-
trolled equipment movements.
Make sure the hoist, lift truck, ropes, slings, spreader,
or other lifting equipment you are using is in good condi-
tion and has a rated lifting capacity equal to or greater
than the weight being lifted. Lifting devices must be
checked frequently for condition and continued confor-
mance to rated load capacity. They should then be
tagged with the inspected capacity together with the
date of inspection.
Fully assembled pumps and pump package units are
heavy and should only be moved using the specified
lifting lugs or attachments. Many individual compo-
nents have lifting eyes or lugs which must not be
used to lift assemblies, as they are designed to
bear the weight of the component only. Before lift-
ing the individual component check to insure the lifting
attachment is firmly secured to the component with un-
damaged, properly torqued fasteners, sound welds, or
other secure attachments. Examine the lifting eyes,
lugs, slots, holes or other projections to insure they are
not cracked, otherwise damaged or badly worn. The
repair of existing or addition of new welded lifting eyes,
lugs or other projections should only be performed by
experienced, qualified welders.
Package units should be lifted with spreaders con-
nected to the lifting attachments normally built into the
package unit support skid. Packages too large to lift ful-
ly assembled should be separated into smaller loads.