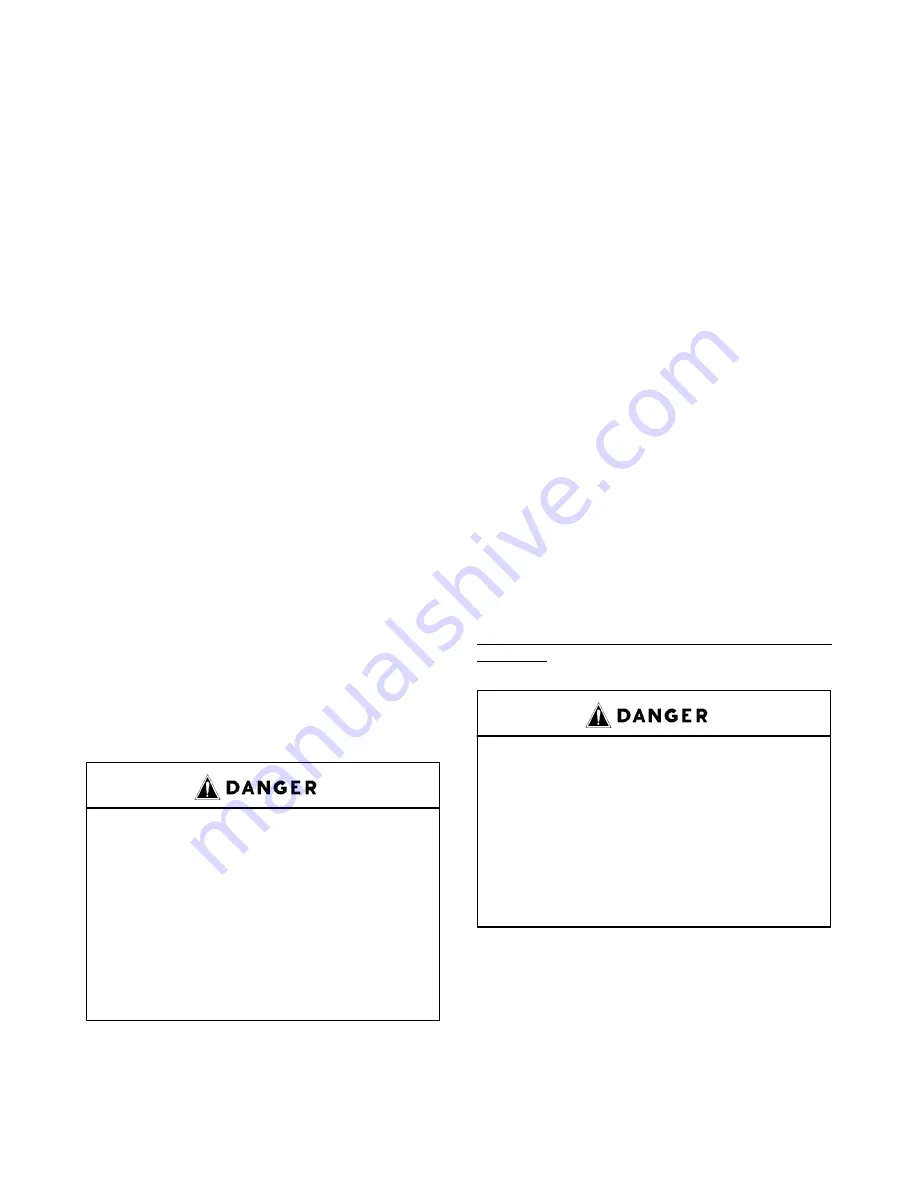
3–600 Page 4
Worn or damaged hose assemblies should be re-
placed immediately. At least every six months ex-
amine hose assemblies internally for cut or bulged
tube, obstructions and cleanliness. For segment style
fittings, be sure that the hose butts up against the nipple
shoulder, the band and retaining ring are properly set
and tight and the segments are properly spaced.
Check for proper gap between nut and socket or hex
and socket. Nuts should swivel freely. Check the lay-
line of the hose to be sure that the assembly is not
twisted. Cap the ends of the hose with plastic covers
to keep them clean until they are tested or reinstalled
on the pump unit. Following this visual examination,
the hose assembly should be hydrostatically tested, on
test stands having adequate guards to protect the oper-
ator, per the hose manufacturer’s proof test procedure.
Fluid end component inspections should be per-
formed more frequently than every six months if
pressures above 2500 psi are used in the dis-
charge system or if corrosive, flammable or hot
(over 110
_
F) fluids are being pumped.
Proper stuffing box packing selection is important for
safe pump operation. Contact a Gardner Denver Ma-
chinery service representative for assistance in select-
ing the proper packing before beginning operation.
Before starting the pump for the first time and periodi-
cally thereafter check the pump, suction and discharge
system fastener torques versus the values listed in the
Operating and Service Manual tables to insure proper
tightness. Over and under torquing can damage
threaded pipes, connections and fasteners, which may
lead to component damage and/or failure. Replace all
components found to be damaged or defective. On
pumps equipped with stuffing boxes, the gland must be
engaged by at least three (3) threads to hold the dis-
charge pressure of the pump.
Do not attempt to service, repair, ad-
just the plunger packing or otherwise
work on the pump while the unit is op-
erating. Shut off the pump drive mo-
tor or engine and relieve the fluid
pressure in the pump suction and dis-
charge systems before any work or
investigation is performed on the
pump or pump systems.
Block the crankshaft from turning and make certain that
all pump drive motor or engine start switches or starter
controls are clearly tagged with warnings not to start
the pump while repair work is in process.
Whenever the pump is operating, continually monitor
the entire suction, discharge and pump lubricating sys-
tems for leaks. Thoroughly investigate the cause for
leakage and do not operate the pump until the cause
of the leak has been corrected. Replace any parts
which are found to be damaged or defective. When a
gasketed joint is disassembled for any reason, discard
the used gasket and replace it with a new, genuine Gar-
dner Denver gasket before reassembling the joint.
Due to the high working pressures contained by the
fluid cylinder, discharge manifold and discharge piping,
welding on these components is not recommended. If
welding on the discharge system cannot be avoided,
only experienced, qualified welders should be used. In
addition, the welded part should be hydrostatically
proof tested in the shop with water or hydraulic fluid to
one and one half times maximum discharge system
working pressure, with no observable fluid leakage, be-
fore the part is reinstalled in the pump system.
In summary, high pressure fluid streams can possess
sufficient energy to cause personal injury, death and/or
equipment damage. These results can occur either
through direct contact with the fluid stream or by con-
tact with loose objects the fluid stream has propelled,
if the pump system is improperly used, or if the fluid is
misdirected, or allowed to escape from defective or im-
properly maintained equipment.
FLAMMABLE, HOT, COLD OR CORROSIVE FLUID
PUMPING
Extreme caution must be exercised
by trained and experienced operators
when flammable, hot, cold or corro-
sive fluids are being pumped, in order
to avoid personal injury, death and/or
equipment damage due to explosion,
fire, burn, extreme cold or chemical
attack.
Never operate a pump which is pumping hydrocarbons
or other flammable, hot, cold, or corrosive fluids when
any part of the pump, suction system or discharge sys-
tem is leaking. Stop the pump immediately if any leak-
age, other than a few drops per minute of packing
weepage, is observed. Keep all flame, sparks, or hot
objects away from any part of the pump, suction sys-
tem, or discharge system. Shield the pump, suction