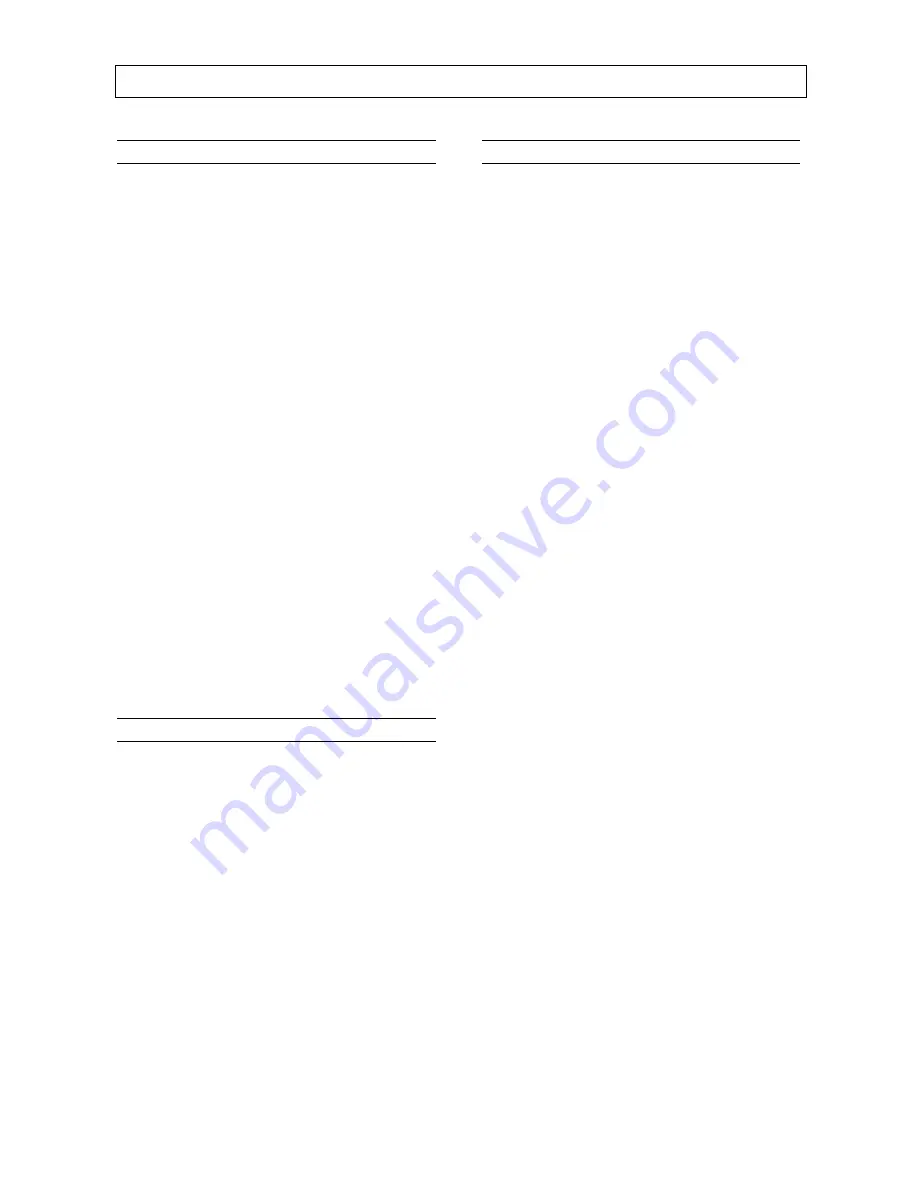
4. Design and functioning
23
4.3
Oil circuit
The oil flows from the pressure reservoir (- 6 - Fig. 3)
into the oil thermostat (- 22 - Fig. 3). With oil tempera-
tures < 55 °C/131 °F the oil flows via the by-pass of the
oil cooler directly into the oil filter (- 11 - Fig. 3) and is
then injected into the screw compressor (- 4 - Fig. 3).
With oil temperatures of between 55 °C/131 °F and
70 °C/ 158 °F the oil flow is divided and fed into the oil
cooler (- 12 - Fig. 3) and the by-pass.
With oil temperatures above 70 °C/158 °F the entire oil
flow is directed via the oil cooler through the oil filter into
the screw compressor.
The oil separated by the oil separator element
(- 7 - Fig. 3) is fed through an oil scavage line to the
screw compressor.
The entire oil circulation is based on a differential
pressure in the system. Considering the pressure
difference of approx. 2 bar/29 PSI within the oil circuit,
the oil is then injected into the screw compressor with
approx. 8 bar/116 PSI at a reservoir pressure of e.g.
10 bar/145 PSI.
When the screw compressor is in the off-load mode, a
sufficiently high pressure differential and thus the
required oil injection quantity is achieved owing to the
fact that when the intake regulator (- 2 - Fig. 3) is
closed, a vacuum pressure occurs in the intake
connection and at the place of injection, and an
overpressure of approx. 15. bar/22 PSI (residual
pressure) in the reservoir.
4.4
Air circuit
The intake air passes through the intake filter (-1- Fig.
3) and the intake regulator (- 2 - Fig. 3) into the screw
compressor (- 4 - Fig. 3). During the compression
process, the intake air is cooled via the injected oil, and
the developed air/oil mixture flows tangentially into the
pressure reservoir (oil reservoir) (- 6 - Fig. 3). After pre-
separation and subsequent fine separation by the
separator element (- 7 - Fig. 3), the compressed air with
a low oil content is fed via the minimum pressure valve
(- 15 - Fig. 3) and the air cooler (- 16 - Fig. 3) into the
consumer network.
4.5
System control
4.5.1
System control ESM 30 (Fig. 3 a)
(See also operating instructions for the compressor
control GD Pilot MK)
Standstill of the system
•
If the plant is shut down, the suction controller (-2-)
is closed by a pressure spring in the adjusting
cylinder.
•
The solenoid valve (- 30 - (Y1)) is deenergised.
•
The oil separator vessel (-6-) is released via valve
(-21-) to atmospheric pressure.
Starting the system
•
The motor starts up in the Y-mode.
•
The intake regulator is closed.
•
The compressor aspires a certain amount of air
through a bypass valve. Pressure builds up in the
reservoir.
•
The oil supply of the screw compressor takes place
through a drop in pressure between the oil separator
vessel and the injection spot in the screw
compressor.
•
If the drive motor is switched over to
Δ
operation,
the magnetic valve switches over (-30-(Y1) since it
is supplied with current.
•
The air circulated in the system streams over the
solenoid valve (-30- (Y1)) in the upper control area
of the operating cylinder (-2.1-). Valves (-31-) and
(-32-) are closed and the lower control space of the
adjusting cylinder is ventilated.
•
The pressure control valve (- 2.2 -) in the intake
regulator (- 2 -) opens.
•
At a reservoir pressure of approx. 4.5 bar/65 PSI the
pressure holding and check valve (- 15 -) opens.
•
Compressed air is now delivered into the consumer
network.
•
The system is now in load running mode.
Stopping the system
•
To de-energise the solenoid valve (- 30 - (Y1) and
press the OFF push-button on the keypad of the
compressor control GD Pilot MK.
•
The pressure valve (-2.2-) in the suction controller
(-2-) closes and the tank is relieved to atmospheric
pressure via the minimum pressure valve (-32-).
•
After 30 seconds, the drive motor (- 3 -) and the
cooling air ventilator motor (- 26 -) are shut down.