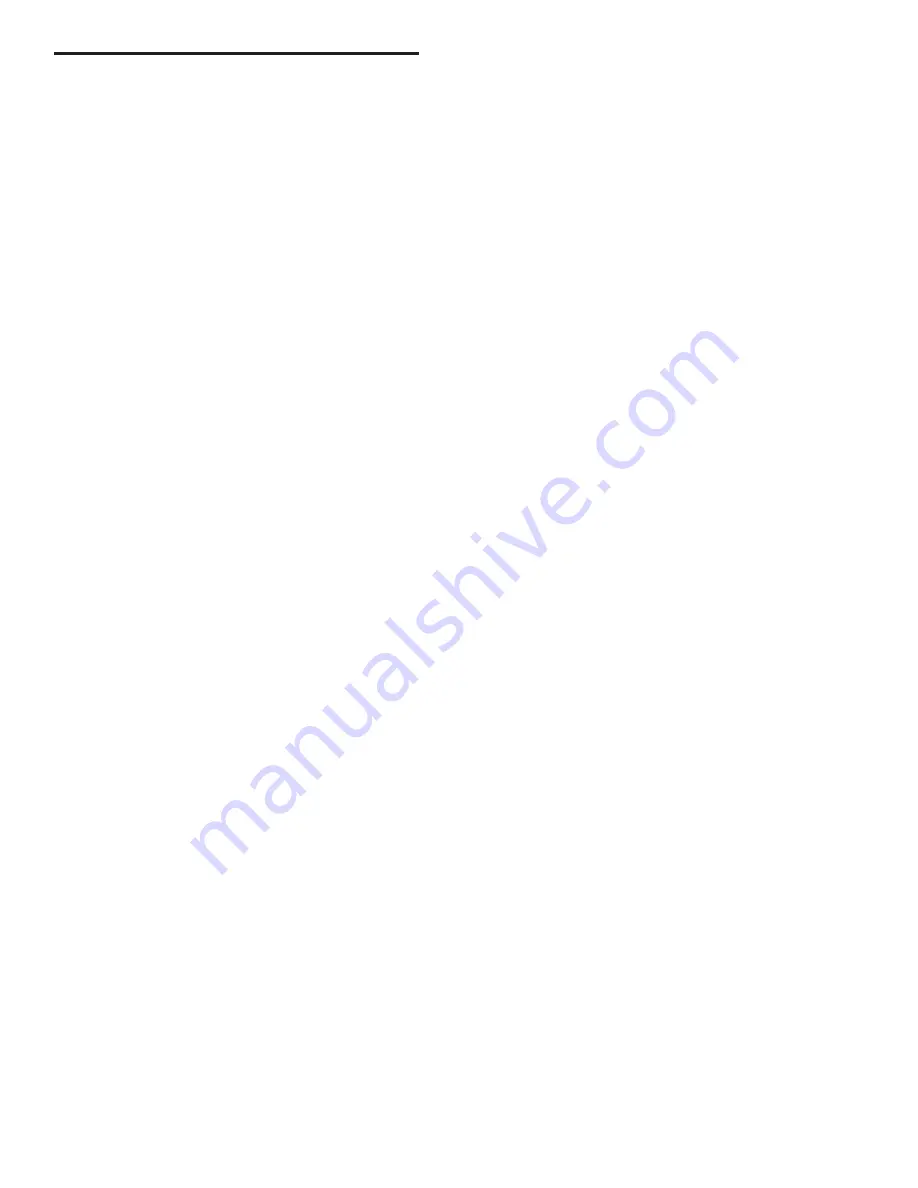
28
7.0 Maintenance
WARNING - This equipment is a pressure-containing
device. Depressurize before servicing.
NOTE
: The Dryer Controller is equipped with Service
Reminder functions for filters, desiccant and valves.
7.1 Desiccant Replacement
NOTE:
The use of the correct replacement desiccant
is necessary for proper dryer operation. Never use
hygroscopic salts of the type commonly used in
“deliquescent ” type dryers.
1. Frequency Of Desiccant Replacement
Desiccant should be replaced whenever the required
dew point cannot be maintained while the dryer is
being operated within its design conditions and there
are no mechanical malfunctions.
NOTE:
Desiccant life is determined by the quality of
the inlet air. Proper filtering of the inlet air will extend
the life of the desiccant. Typically desiccant life is 2
years.
2. Procedure for Desiccant Charge Replacement
a. Depressurize and de-energize the dryer.
b. Remove the fill and drain plugs or flanges (where
applicable) from the desiccant tower and drain the
spent desiccant. Place a container at the base of
the vessel to collect the desiccant. If necessary
tap the sides of the vessels with a rubber mallet
to loosen desiccant.
NOTE:
Use extreme care when inserting rods or
other tools through the desiccant fill or drain ports
to loosen packed desiccant. Internal flow diffusers
at the ends of the desiccant beds can be damaged
or punctured by sharp instruments. These diffusers
are necessary to distribute the airflow and keep the
desiccant beads within the tower. Desiccant beads in
exhaust mufflers, afterfilters, or the piping connected
to the desiccant towers may indicate a perforation of
a diffuser.
c. Replace the drain plug using Teflon tape or another
pipe thread sealant suitable for compressed air
service. Reinstall drain port flange cover (where
applicable) in each desiccant tower.
d. Refer to Table 1 (on page 5) for desiccant
quan-
tity per tower.
When using Table 1 you will find the desiccant
quantities listed in layers. Each layer will vary in
depth due to the type, quantity and purpose of the
desiccant. Layer 1 must be installed first at the
bottom of the vessel followed by layer number 2
etc., until the complete charge of desiccant has
been installed.
e. Utilizing an appropriate sized funnel, fill each
desiccant tower as follows:
1) Install the required quantity of tabular support
(model 4300 only) or activated alumina in
layer 1 of each tower.
2) Level layer 1 and each subsequent layer of
desiccant as added to each tower.
3) Finish filling each tower with desiccant until
all desiccant has been installed. LIGHT tap-
ping on the tower sides with a soft-face mallet
should yield additional free space to allow
installation of all desiccant required.
DO NOT
TAMP OR RAM DESICCANT
.
f. Clean the fill port closure. Replace the fill plug
using Teflon tape or another pipe thread sealant
suitable for compressed air service. Reinstall fill
port flange cover (where applicable) in desiccant
tower.
3. Insuring Desiccant Dryness
Replacement desiccant is shipped in airtight
containers. Keep the covers on these containers
tightly closed until use to avoid moisture
contamination. If desiccant is exposed to air it can
be heated in an oven at 400°F (204°C) for four hours
before use. Alternatively, if the dryer is not refilled
with dry desiccant, it may be necessary to operate
the unit with an inlet flow rate of less than 50% of
maximum rated inlet capacity until the desiccant has
regenerated fully.
7.2 Purge Mufflers
Purge mufflers should be checked regularly, changed
annually. Muffler disseminator elements become clogged
with desiccant dust over time, creating back pressure
and restricted purge flow.
7.3 Valves
1. Process and pilot valves should be checked fre-
quently for leaks and proper operation.
2. Purge pressure adjustment valve should be checked
frequently for proper adjustment.
7.4 Pilot Air Filter Element Replacement
1. Frequency of replacement
The pilot air filter contains a filter element that should
be changed yearly. Replacement may be required
sooner if pressure drop across cartridge prevents
valves from actuating properly.
WARNING
– The pilot air filter housing is a pressure-
containing device, depressurize before servicing.
Slowly open manual drain valve on bottom of filter
bowl by turning clockwise to verify that the housing
is depressurized before removing bowl.