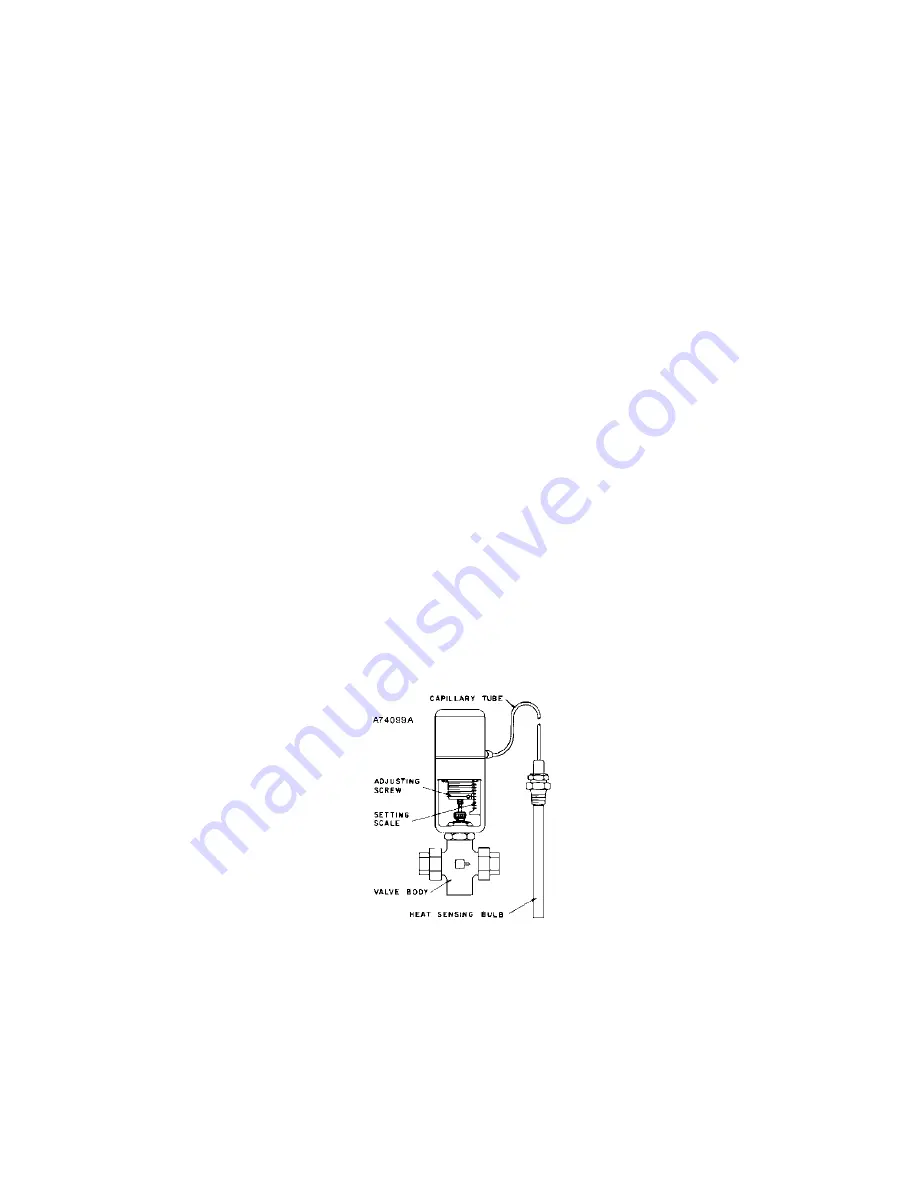
13-18-612 Page 59
6-4
The water supply shall be capable of delivering the flow/temperature combinations shown in Figure 6-2,
page 58, at a minimum pressure of 40 psig (2.8 bar) - the water flow rates shown are approximate and a
guide to sizing of piping, cooling tower and other water system equipment.
The maximum allowable supply water pressure is 150 psig (10.3 bar) and the maximum allowed
(package) outlet water temperature is 110
F (43
C). If a water supply with a temperature lower than 60
F
(16
C) is used, heat transfer areas of the coolers may be fouled due to low water flow velocities, resulting
in poor cooler performance and shortened operational life.
All the required hardware, mechanical and electrical connections have been made at the Gardner Denver
factory. Regular maintenance is required to keep the interior core areas free from dirt and other fowling
agents. In order to protect package components that are in contact with the cooling water from attack by
corrosive or fouling agents, we recommend that the cooling water meet the following quality standards:
Total Dissolved Solids (TDS) ..................... <500 ppm
Iron ............................................................. <2 ppm
Total Hardness .......................................... <60 ppm
Silica .......................................................... <25 ppm
Oil and Grease ........................................... <5 ppm
Sulfate ........................................................ <50 ppm
Chloride ...................................................... <50 ppm
Nitrate ........................................................ <2 ppm
Corrosivity .................................................. Langelier Index between 0 to1
It is strongly recommended that a reputable, local firm be contracted to evaluate the quality of water
available and recommend corrective and/or preventive steps to meet our requirements.
WATER FLOW REGULATING VALVE (Optional Hardware)
. This device is used to adjust the flow of
cooling water in proportion to its temperature. It’s a normally closed (two-way) valve which opens once
the thermostatic bulb senses a predetermined water temperature level and then continues to modulate
water flow to maintain water temperature
– within a 2
F to 5
F span. The package piping provides a
permanent bypass line (1/4” tube) around the flow regulating valve to ensure a small amount of water
flows around the sensing bulb when the valve is in the closed position
– it does not provide a complete
shutoff of water flow.
Figure 6- 3
– WATER CONTROL VALVE
Adjustments
–
The regulator valve shall be adjusted so that it closes when the cooling water entering
and exiting the package are at the same temperature
– a condition that is present after the compressors
have stopped and the heat exchangers have cooled down. Note that the bypass line allows a small
amount of water flow when the valve closes. Adjustment to the regulator valve can be made as follows:
To decrease water flow (e.g., increase exiting cooling water temperature) turn the adjusting screw
from left to right, increasing spring tension. (The groove at the lower edge of the adjusting screw is
an index line for use with the index scale 0 to 8 in obtaining a desired setting).
Summary of Contents for AirSmart VS80-110B
Page 33: ...13 18 612 Page 32 4 7 300CGE546 04 Ref Drawing Page 2 of 4...
Page 34: ...13 18 612 Page 33 4 8 300CGE546 04 Ref Drawing Page 3 of 4...
Page 35: ...13 18 612 Page 34 4 9 300CGE546 04 Ref Drawing Page 4 of 4...
Page 37: ...13 18 612 Page 36 4 11 301CGE546 B Ref Drawing Page 2 of 4...
Page 38: ...13 18 612 Page 37 4 12 301CGE546 B Ref Drawing Page 3 of 4...
Page 39: ...13 18 612 Page 38 4 13 301CGE546 B Ref Drawing Page 4 of 4...
Page 41: ...13 18 612 Page 40 4 15 302CGE546 05 Ref Drawing Page 2 of 4...
Page 42: ...13 18 612 Page 41 4 16 302CGE546 05 Ref Drawing Page 3 of 4...
Page 43: ...13 18 612 Page 42 4 17 302CGE546 05 Ref Drawing Page 4 of 4...
Page 45: ...13 18 612 Page 44 4 19 303CGE546 B Ref Drawing Page 2 of 4...
Page 46: ...13 18 612 Page 45 4 20 303CGE546 B Ref Drawing Page 3 of 4...
Page 47: ...13 18 612 Page 46 4 21 303CGE546 B Ref Drawing Page 4 of 4...
Page 70: ...13 18 612 Page 69 9 2 Figure 9 1 MINIMUM DISCHARGE PRESSURE CHECK VALVE...
Page 86: ...NOTES...
Page 87: ...NOTES...