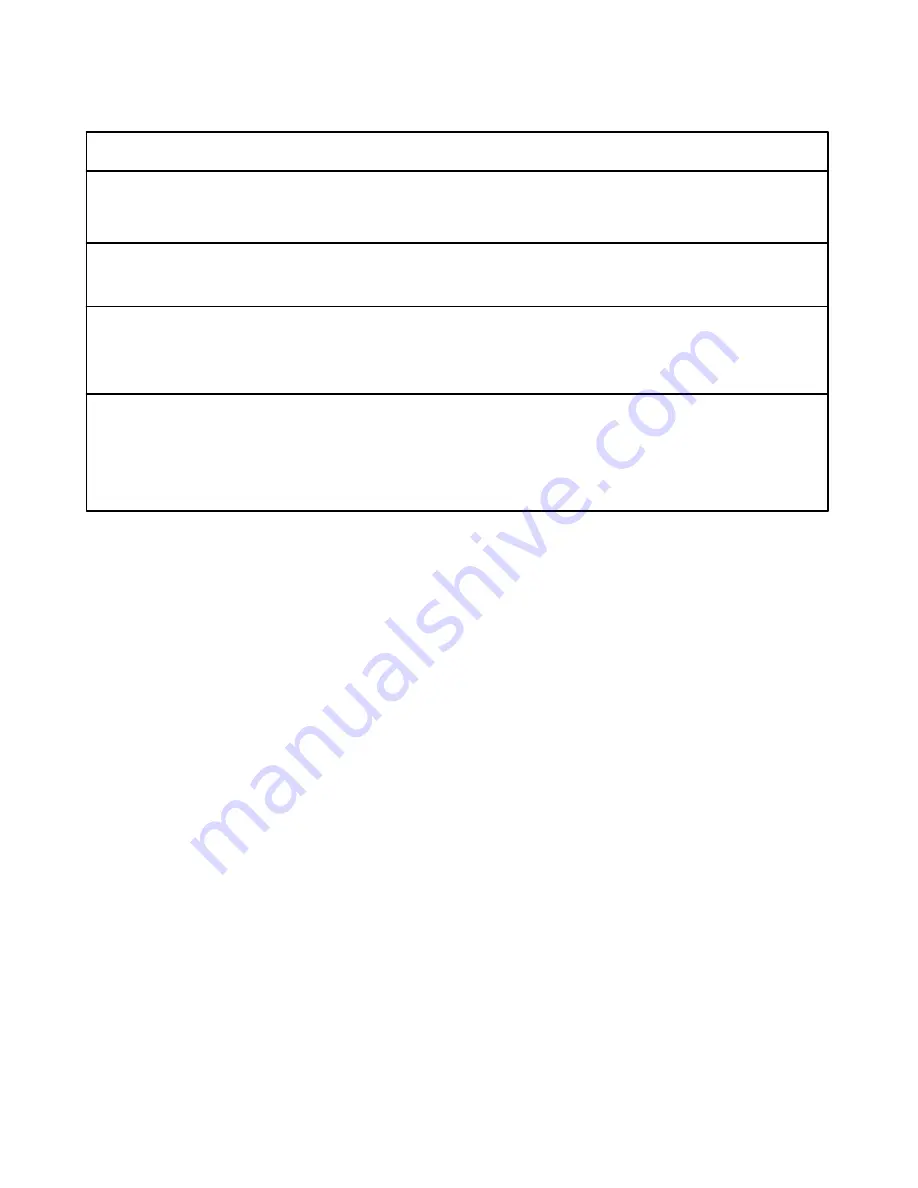
SB--7--627 Page 14
TROUBLE SHOOTING (Continued)
PROBLEM
POSSIBLE CAUSES
SOLUTION
Lack of volume.
1.
Slipping belts.
1
Tighten belts.
2.
Worn clearances.
2.
Re-establish proper clearances.
Excessive bearing
1.
Improper lubrication.
1.
Correct lubrication level. Replace
or gear wear.
dirty and/or improper oil.
1.
Headplate, gear case or
1.
Clean vents.
Loss of oil.
drive cover vents plugged.
2.
Worn seal.
2.
Replace seals.
Lack of oil pressure.
1.
Dirty suction screen.
1.
Clean suction screen.
2.
Leak in suction line.
2.
Repair leak.
3.
Lubrication pump losing its prime.
3.
Reprime, by removing pipe plug
and priming.