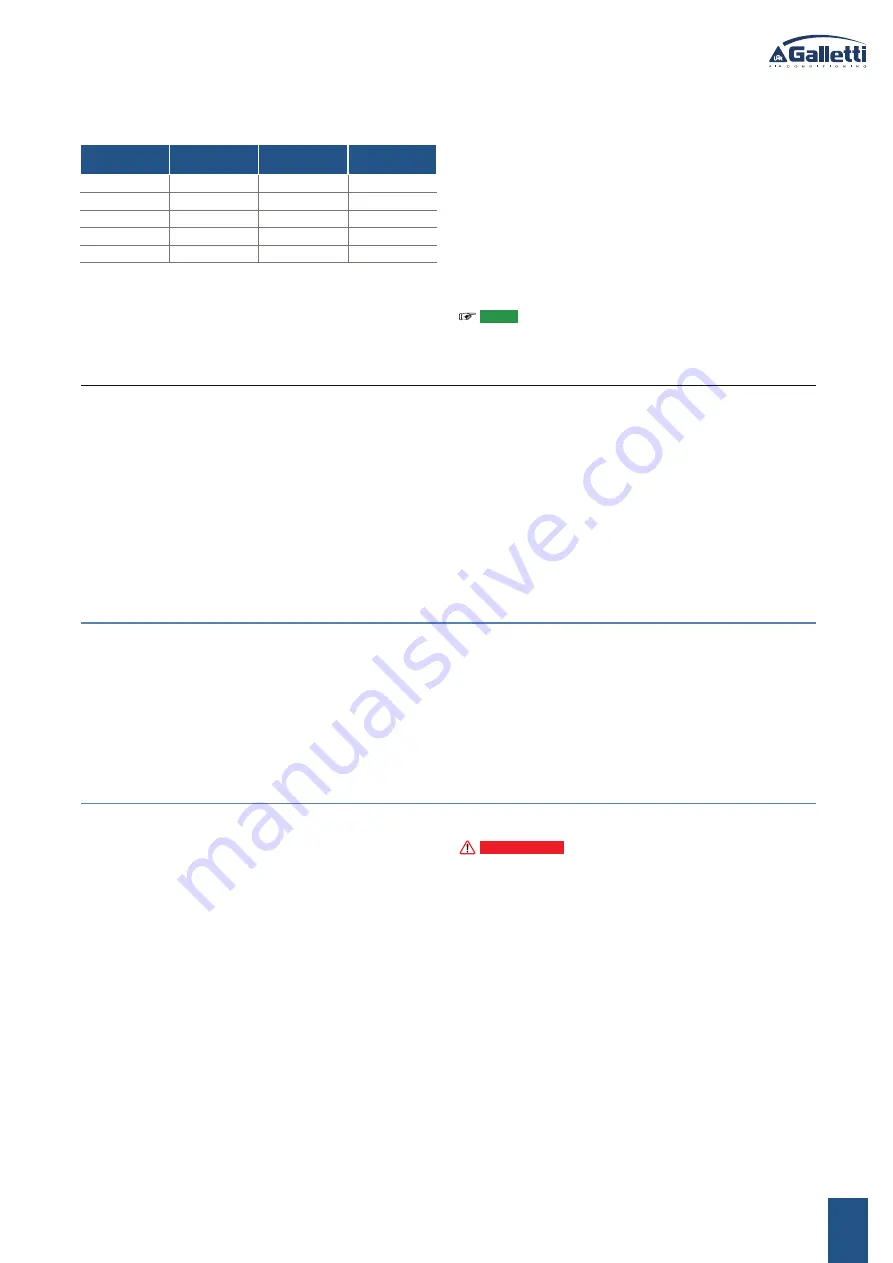
FC66005296
21
system, to prevent ice from forming. If anti-freeze solutions are
used, check for their freezing point using the table below.
% Glycol by weight
Freezing
temperature (°C)
Capacity
adjustment
Pressure drop
adjustment
0
0
1,00
1,00
10
-4
0,97
1,05
20
-10
0,92
1,10
30
-16
0,87
1,15
40
-24
0,82
1,20
Electrical connections
Make the electrical connections with the power supply dis-
connected, in accordance with current safety regulations,
and following the wiring diagrams in figure Base wiring dia-
gram p. 64 and pertinent legend.
Check that the mains electricity supply is compatible with the
voltage shown on the unit rating plate.
The electrical connections indicated must be made by the
installer.
For each fan coil a switch (IL) should be mounted on the power
supply, with opening contacts at a distance of at least 3 mm and
a suitable protection fuse (F).
For control electrical connections follow the wiring diagrams on
figures : p. 65 Wiring diagram EVO , p. 66 Wiring diagram
My Comfort Large e p. 67 TED10 Wiring diagram.
NOTE:
My Comfort Large control is available in wall-
mounted version only.
MOUNTING BASE UNIT AND COVER CABINET
Upon receipt of the unit, check the integrity of the package.
Leave the cabinet inside the packaging and proceed with the
installation of the base unit (which also includes the air outlet
grille, in the upper part) to the wall using the 4 slots provided
and the screw anchors suitable for the characteristics of the sup-
porting wall, keeping the bottom edge at least 100 mm above
the floor to ensure a correct intake of air and facilitate the filter
removal. See figure p. 68 Air filter .
Once the installation of the base unit (which also includes the
hydraulic and electrical connections) is completed, it is possible
to proceed with the assembly of the covering cabinet (front pan-
el and side panels)
In order to fix the cabinet, proceed with positioning it near the
base unit, so as to align the support pins with the slots on the
rear panel (see figure 11.11 Cabinet p. 69).
Then, lower the cabinet so as to obtain the locking of the pins
inside the appropriate seats.
To prevent the cabinet from disassembling it is necessary
to act on the lower locking screw, as shown in the figure
11.11 Cabinet p. 69.
6 CHECKS BEFORE STARTUP
— Check that the unit is properly levelled and that the drainage
outlet is not clogged (by masonry debris, etc.)
— Check that the unit is installed in such a way as to guarantee
the proper air flow.
— Check the tightness of the plumbing connections (to the ex-
changer and condensate drainage line).
— Make sure the electric wires are tightly connected (carry out
this check with the power supply OFF).
— Make sure that air has been eliminated from the heat ex-
changer.
— Reapply the cabinet and filter
— Power the fan coil and check its performance
7 USE
To use the fan coil refer to the instructions on the control panel
available as accessory.
The air flow may be directed as desired using the upper FLAP
(flow may be directed upward or downward) as well as the sec-
ond row of louvers (for directing air flow either to the left or
right) as shown in figure p. 61 Control view e p. 61 Con-
tinuous upper grill .
ATTENZIONE:
For safety reason, do not introduce your fin-
gers or other pointed objects in the air outlet grilles.
Summary of Contents for ART-U
Page 12: ......