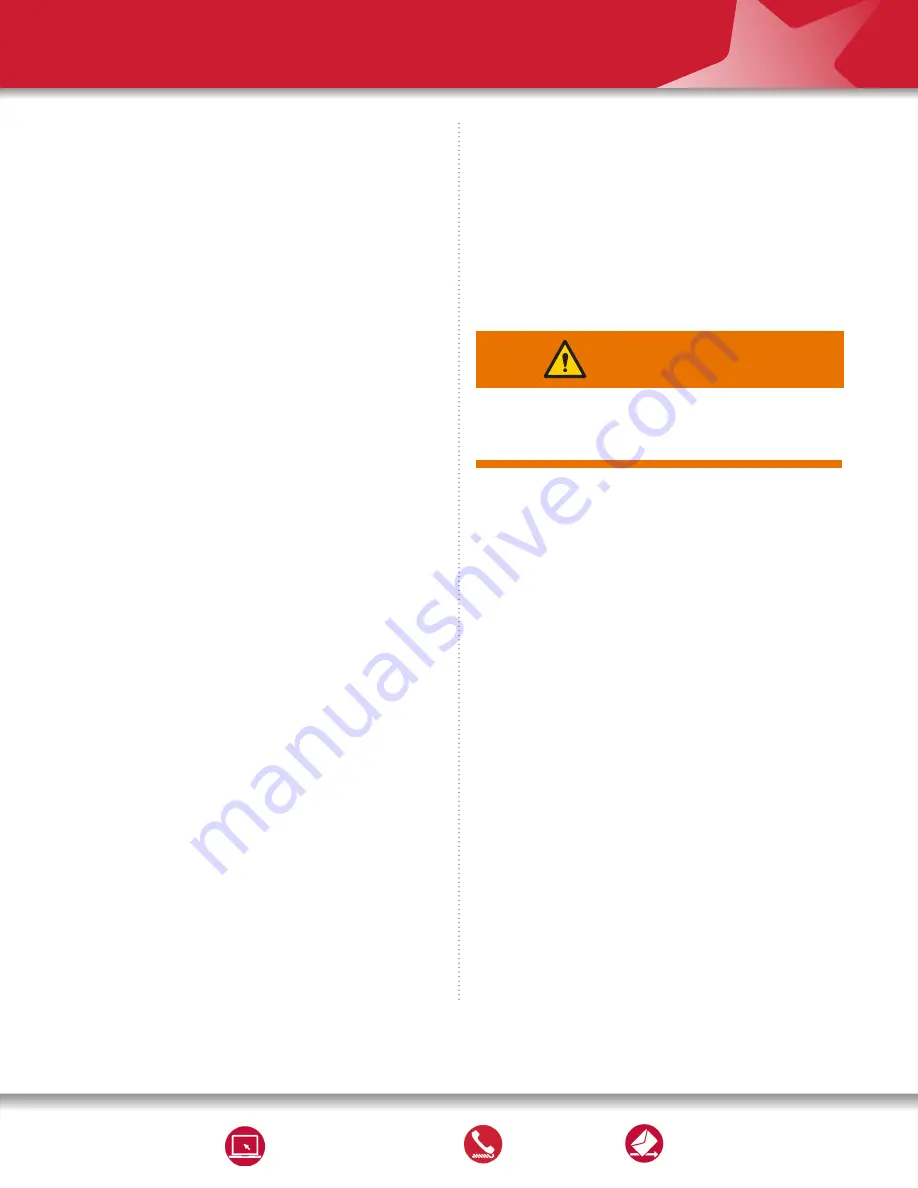
7
Questions?
www.galbreathproducts.com
1-800-285-0666
Failure to comply with the lockout procedure may result
in severe injury or death and/or damage to equipment.
LOCKOUT GUIDELINE
(Required By Safety Standards)
The purpose of a Lockout Procedure is to recognize,
isolate, and render safe all types of energy sources.
The Lockout Procedure should establish performance
habits which protect all personnel from injury while
they are in, on, or around the equipment during repair,
maintenance, and other associated activities.
Compliance and enforcement of a Lockout Procedure
is the responsibility of the owner and operator. The
following information provides a guideline for creating
a Lockout Procedure. A detailed documented program
must be established to fit each situation and condition.
1. Observe and review all conditions of the
equipment. All sources of stored energy must be
recognized, managed, and cautiously released by
qualified personnel. Examples:
• Shut down truck engines and any auxiliary
engines.
• Disengage power take-off systems.
• Relieve stored hydraulic or pneumatic pressure
after installing any blocking devices.
• Relieve all entrapped hydraulic pressure.
2. Remove the key from the vehicle ignition.
3. Notify all affected individuals that they must
comply with the Lockout Procedure.
4. Tag all controls to inform personnel that the
equipment is “under repair,” “do not operate,”
or whatever the situation dictates. All affected
personnel must be informed of the meaning and
appearance of the Lockout Tag.
MINIMUM REQUIREMENTS FOR LOCKOUT TAG:
• Tags must be made of a material capable of
withstanding the environment to which they are
exposed. Examples: oil, grease, fuel, etc.
• Tags must be easily recognizable and clearly
visible at the location of the operating controls.
• Tags must be standardized using one or more
of the following criteria: color, shape, size, and/
or format.
5. Only authorized individuals should release the
equipment for use after repairs have been made.
6. Periodic inspections should be done by the owner
to verify the correct use and compliance with the
Lockout Procedure.
NOTE: Other procedures and responsibilities may be
associated with the Lockout Procedure as dictated by
the uniqueness of each situation and any applicable
standards and/or codes.
Please note that the guidelines listed above are
intended to create an awareness of the necessity for a
“Lockout/Tagout Procedure.” The owner should obtain
a current copy of the following references:
• ANSI Z244.1
• Federal Code Of Regulations Title 29 Part 1910
Section 1910.147
The Federal Code Of Regulations may be accessed
via the Internet at the National Archives and Records
Administration website at:
http://www.access.gpo.gov/nara/cfr/
It is ultimately the owner’s responsibility to establish,
train for, and oversee the implementation of all lockout/
tagout procedures.
WARNING