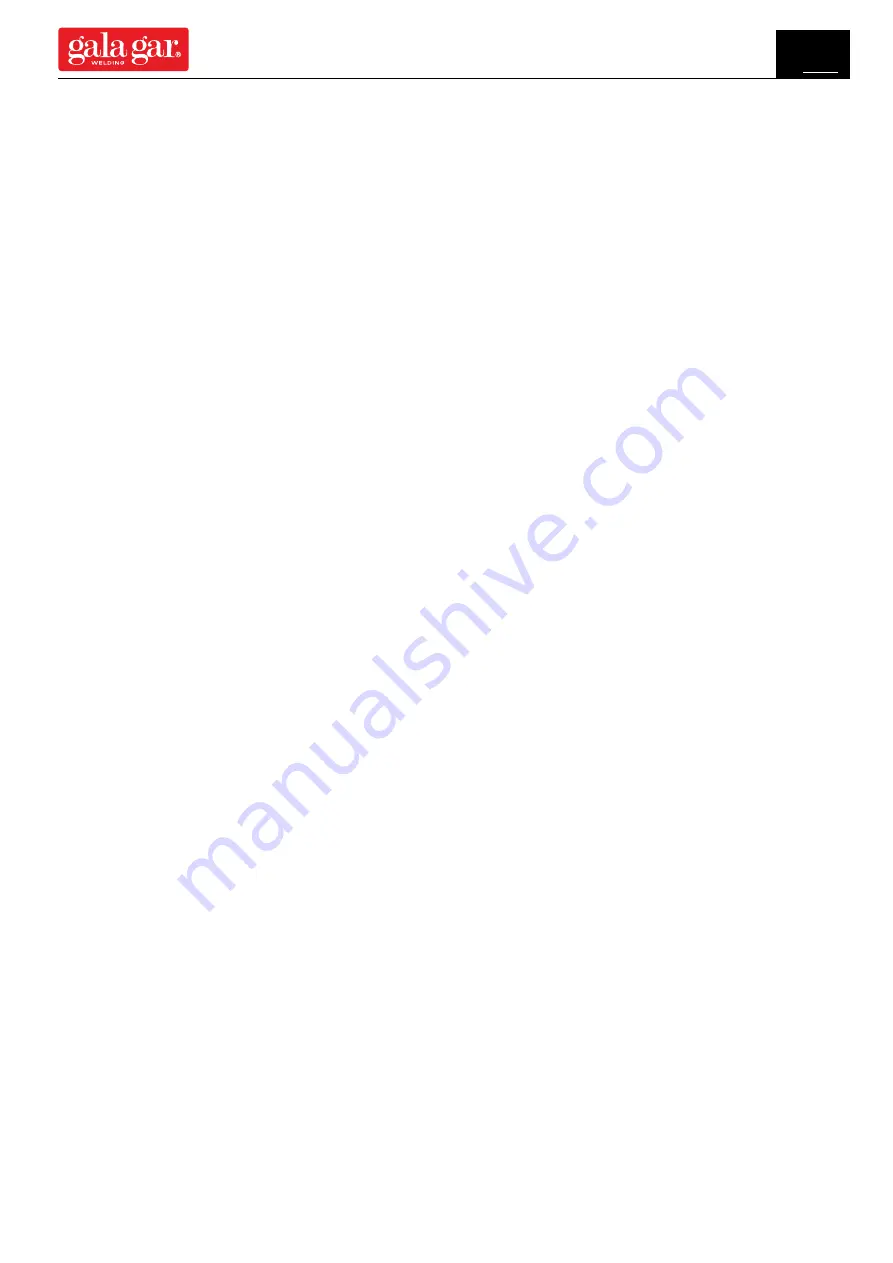
GALA ELECTRONICS 300 T
GALA ELECTRONICS 300 T
GALA ELECTRONICS 300 T
GALA ELECTRONICS 300 T
E
E
E
E
GB
GB
GB
GB
0
34
−
Increase of heat-affected zone.
Peak time
Time for which the current pulse is at the maximum value.
Consequences of a higher value:
−
Greater weld penetration.
−
Facility to make deeper cuts.
Consequences of a lower value:
−
Reduction of heat-affected zone.
−
Difficult to create a weld pool.
Base time
Time during which current output is at the base value.
Consequences of a higher value:
−
The filler material is spread more evenly.
−
Increase of heat-affected zone.
Pulse frequency
Consequences of a higher value:
−
Slower melt speed.
−
Reduction of heat-affected zone.
Slope down
Time during which the current changes from the welding value to the
end value by means of a slope.
Final current
During electrode welding the parameter makes it possible to obtain a
uniform deposit of filler material from the start to the end of the
welding process, closing the deposition crater with a current such as
to deposit a final droplet of filler material.
By keeping the torch trigger pressed during the 3rd time, the crater
filler current is maintained thereby ensuring optimal crater filling, until
the POST GAS time is started by releasing the torch trigger (4Th
time).
Post-gas
Time of post gas delivery when the welding arc is extinguished.
Consequences of a higher value:
−
More effective pickling (improved appearance of workpiece at the
end of the welding pass).
−
Higher gas consumption.
Consequences of a lower value:
−
Lower gas consumption.
−
Oxidation of electrode tip (more difficult arc strike).
Pre-gas
Time of gas delivery before the arc strike.
Consequences of a higher value:
−
This parameter allows a shielded environment to be created,
thereby eliminating contaminants at the start of the welding pass.
Start current
Unit current output value immediately after the arc strike.
Slope up
Time during which the current changes from the starting value to the
welding value by means of a slope.
Spot TIG time
When the torch trigger is pressed the welding arc persists for the time
set in the parameter.
Press the torch trigger again to resume the welding process.
The arc strike procedure is as follows:
Positioning of the torch with the electrode on the workpiece.
Press the torch trigger and keep it pressed.
Lift the torch slightly.
As soon as the electrode is lifted then the HF ignition starts.
The arc ignites for few hundredths of a second (time can be set up).
The result of this is a very precise, not oxidized welding spot without
any plastic deformation of the sheet.
HF arc start
This parameter enables the arc strike in the TIG welding procedure by
means of a high frequency (HF) current discharge.
The parameter prevents the inclusion of impurities at the start of the
weld pass.
This parameter can harm electronic boards when welding is
performed on equipment that incorporates such devices.
Minimum pedal current
Minimum output current value with foot pedal controller external
reference.
The current is set as a percentage with respect to the "maximum foot
pedal current" parameter.
Q-start
This parameter allows the unit to start in synergic pulsed TIG mode
for the preset time interval, before switching automatically to the
welding procedure selected on the interface panel.
The parameter creates a weld pool faster with respect to the standard
starting procedure.
This parameter is useful when spot welding thin gauge sheet.
Multi-tack
This parameter allows thin gauge sheet to be welded without
deformation.
Consequences of a higher value:
−
Welding of thinner gauge sheet without deformation.
−
Less melting of material, slower welding process.