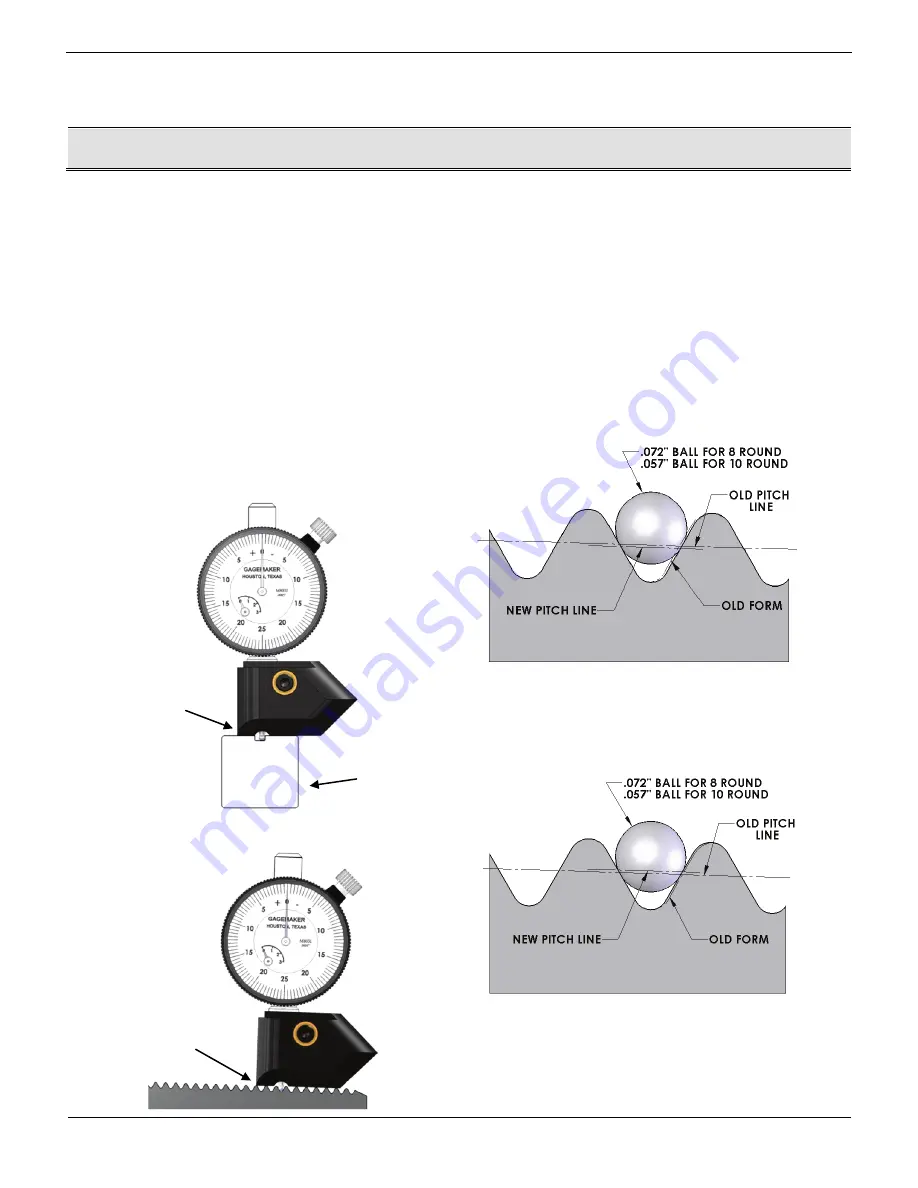
Pitch Diameter Gage Operation Manual
Models MRP 1500/2500/3500
Copyright © 2018 Gagemaker. All rights reserved
56
MRP Accuracy Measurement Factors
Thread Addendum Measurements
Accurate MRP measurements are based on positioning the pivot shoe on the crest cone of the
thread at a prescribed distance from the face of the connector. If the distance from the pitch line
to the crest cone is accurate, then readings taken from at the crest cone directly reflect the
accuracy of the pitch diameter.
Problems occur when the threading process pushes a thread flank back, to decrease standoff of
a ring or plug. When the flanks are relocated, the distance from the pitch line to the crest is
changed.
Thread Addendum
is the change in the distance from the pitch line to the crest cone.
Changes in thread addendum affect the relationship of measurements taken with the MRP gage
and measurements taken with ring and plug gages.
The diagrams below describe how plus and minus addendum is detected and how to compensate
for its effect on the readings of the MRP gage.
Plus Addendum – Wide Groove – Large Reading
Mating part will have less standoff
P.D. Correction for Plus Addendum:
Pin = Subtract 2 times deviation from P.D.
Box = Add 2 times deviation to P.D.
Minus Addendum – Narrow Groove – Small Reading
Mating part will have more standoff
P.D. Correction for Minus Addendum:
Pin = Add 2 times deviation to P.D.
Box = Subtract 2 times deviation from P.D.
Setting Standard
Seat the contact point into
the standard’s groove
Rest the gage on
the thread crests
Zero the indicator while the gage (TA-3002) is
on the standard (TAS-1014)
TAS-1014