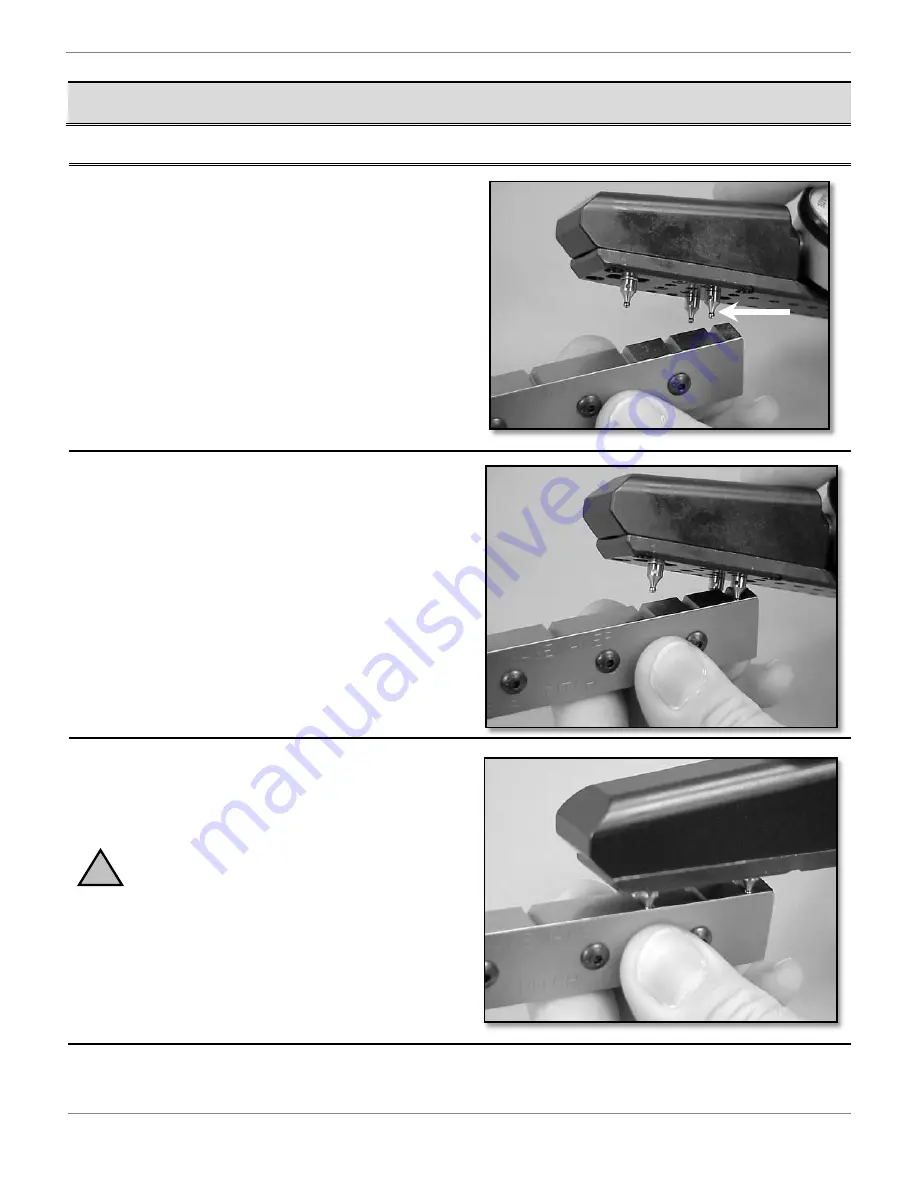
Lead Gage Operation Manual
Model LG-5003
10
Copyright © 2014 Gagemaker. All rights reserved
Zeroing the Lead Gage (continued)
1. Loosen the indicator clamp and place fixed
contact point in the first groove of standard.
2. Slide the gage over until the fixed contact point
seats against the fence.
3. Place moveable contact point into the groove
of setting.
For Non-V threads, pull the lead gage
toward the load flank of the groove in the
standard.
For V threads, be sure the contact points
touch both flanks of the groove in the
standard.
!