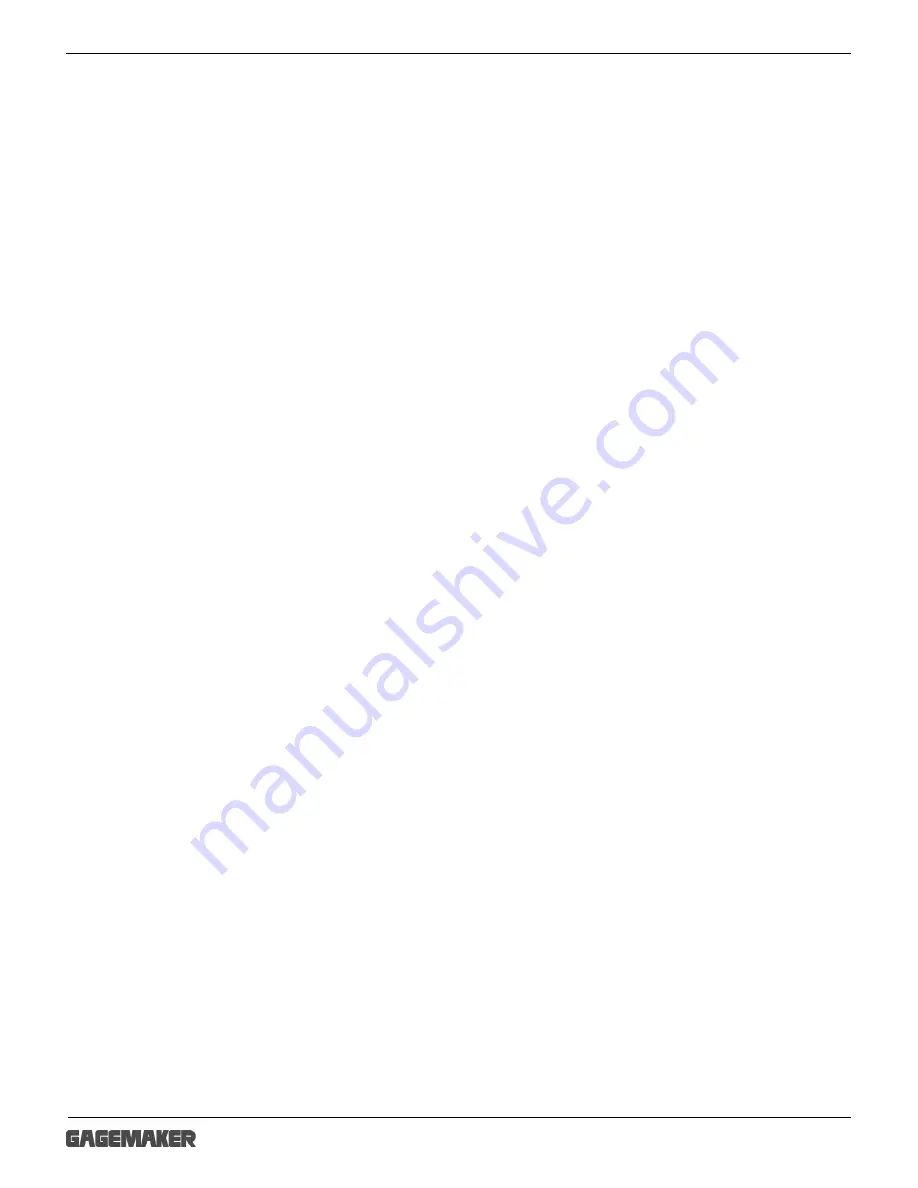
B
B
X
X
/
/
B
B
X
X
G
G
-
-
1
1
0
0
0
0
0
0
S
S
e
e
r
r
i
i
e
e
s
s
G
G
r
r
o
o
o
o
v
v
e
e
M
M
e
e
a
a
s
s
u
u
r
r
e
e
m
m
e
e
n
n
t
t
G
G
a
a
g
g
e
e
O
O
p
p
e
e
r
r
a
a
t
t
i
i
o
o
n
n
M
M
a
a
n
n
u
u
a
a
l
l
7
Introduction
The BX-1000 and BXG-1000 gages measure face groove diameters and widths. These gages adjust to
cover all sizes of R, RX, and BX ring grooves. The standard BX-1000 gage measures groove diameters
from 2.6” – 13”. Optional rails extend the range of diameters from 13” – 36”. The BXG-1000 inspects
groove widths from .34” – 1.5”.
The BX-1000 can be used to measure straight or tapered groove diameters, shallow bores, and hole
locations. The gage ships standard with .188” diameter contact points. The BXG-1000 measures widths
of straight or tapered grooves and includes .072” diameter contact points.
The BX and BXG gages use precision contact points for accurate measurement of the ring groove
diameter and width at the critical sealing point of the face groove.
Before inspecting parts, the BX and BXG gages require presetting to a nominal predetermined
dimension. The Groove Inspection Tolerances and Setting Dimension tables in this manual determine
the gage’s setting dimensions and gauging tolerances. The BX-1000 gages can be preset using
micrometers, gage blocks, or the MIC TRAC MT-3000 measurement center.
To inspect parts, place the contact points in the groove of the part and the gage is positioned by
sweeping to obtain an indicator reading. Gage indicators show actual deviation from the preset master
dimension. Taking measurements in several different locations along the groove will provide an
average groove diameter or groove width. In addition, we recommend that the gage be zeroed
periodically during use to maintain accurate readings.
Technical Support
Phone: 713-472-7360
Hours: Monday – Friday 8AM – 5PM (CST)
Product Information and Updates
Visit our web site: www.gagemaker.com