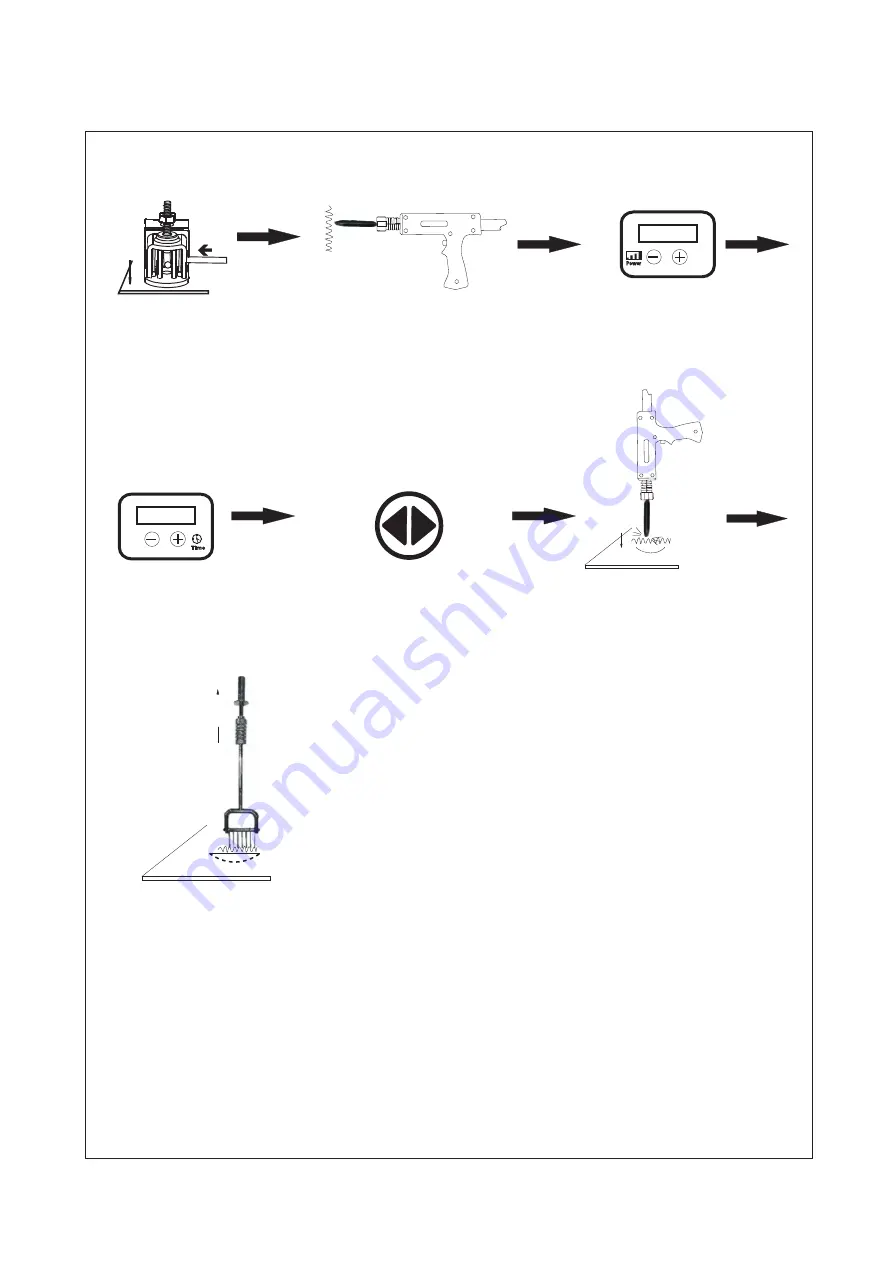
e 、
3 、 Operation
Wriggle
Form
Wire
Welding
Page.15
Connect wave form wire electrode
tip with welding gun.
Set correct time.
Remark:
1 、 Setting amperage too high or time too long can cause workpiece surface (vehicle body)damage .
Please weld other workpieces for practice before actual operations.
2 、 Setting correct amperage and time according to the workpiece thickness.
3 、 Continuing another operation is applicable after these procedures finished .If not ,please
shut off the main power supply and switch off the unit.
Select welding function
Connect negative outside wire
to a clean,paint-free location
on metal workpiece,as close to
welding area as possible.
Connect hook puller with pull hammer.
Hook wave form wire and slide the
hammer to pull out the dent.
Place a wave form wire
horizontally on the dent.
Approximately a 90°angle
to wave form wire.Put on
pressure andpress trigger.
(Position A is recommend).
Set correct power
Summary of Contents for GI12117
Page 1: ...USER MANUAL GI12117 ...