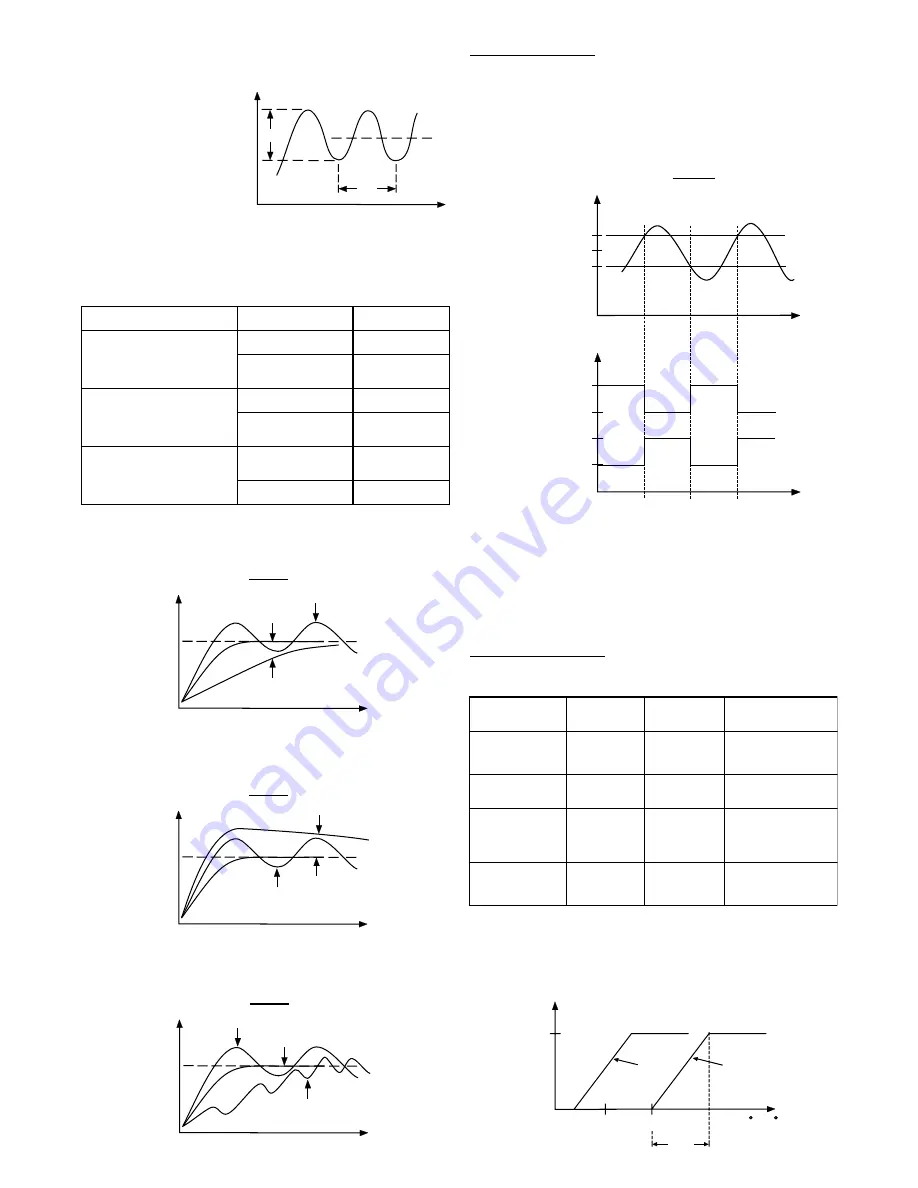
5.9 COOLING CONTROL
Cooling Control Options:
Functions of CPB and DB:
The cooling P band CPB and dead band DB are measured in degree.
(2) The cycle time (T) of this oscillation in seconds (see following Figure).
* The control setting should then be adjusted as follows:
PB = P (°C or °F)
TI = T (seconds)
TD = T/4 (seconds)
The PID parameters determined by the above procedures are just rough
values. If the control results by using above values are unsatisfactory, the
following rules may be used to further adjust the PID parameters:
5.8 ON-OFF CONTROL
The alarm output if configured as alarm function performs an ON-OFF
control basically. Adjust the P band to PB = 0, an additional channel of
ON-OFF control with variable hysteresis is obtained. Hysteresis is
measured with degree. It is also named differentials or deadband
sometimes. Refer to following Figure for the description of ON-OFF control.
ON-OFF control may introduce excessive process variation even if the
hysteresis is minimized to the smallest. If the ON-OFF control is set,
parameters TI, TD and CCT will have no effect on the system, nor can the
manual mode and the auto-tune program be executed.
PV
Time
D action
Perfect
TD too high
TD too low
SP
PV
Time
Time
P action
SP
100%
0%
100%
0%
Reverse
Action
Action
(CONA=REVR)
(CONA=DIR)
Direct
OUTPUT
SP+HYST/2
SP-HYST/2
SV+DB
CPB
SV
DB
Negative
DB
Positive
100%
0%
Cooling
Output
PV( C or F)
P
T
SV
PV
Time
PV
Time
P action
Perfect
PB too high
PB too low
SP
PV
Time
I action
Perfect
TI too low
TI too high
SP
Effect of PID adjustment on process response:
ADJUSTMENT SEQUENCE
SYMPTON
SOLUTION
(1) Proportional Band (P)
Slow Response
Decrease PB
PB
High overshoot or
Oscillations
Increase PB
(2) Integral Time (I)
Slow Response
Decrease TI
TI
Instability or
Oscillations
Increase TI
(3) Derivative Time (D)
Slow Response or
Oscillations
Decrease TD
TD
High Overshoot
Increase TD
Output
Configurations
Heating Output
Cooling Output
Adjustment of
Parameters
ON-OFF Cooling
( No Heating)
None
OUT1
CONA = DIRT
HYST
SV
Proportional Cooling
( No Heating)
None
OUT1
CONA = DIRT
PB, TI, TD, CYC, SV
H
ON-OFF Cooling
OUT1
ALM2
CONA = REVR
A2SF = NONE
A2MD = DVHI (or FSHI)
AHY2, SV (or ASP2)
H
Proportional Cooling
OUT1
ALM2
CONA = REVR
A2SF = COOL
CPB, DB, CCYC, SV
Page 9