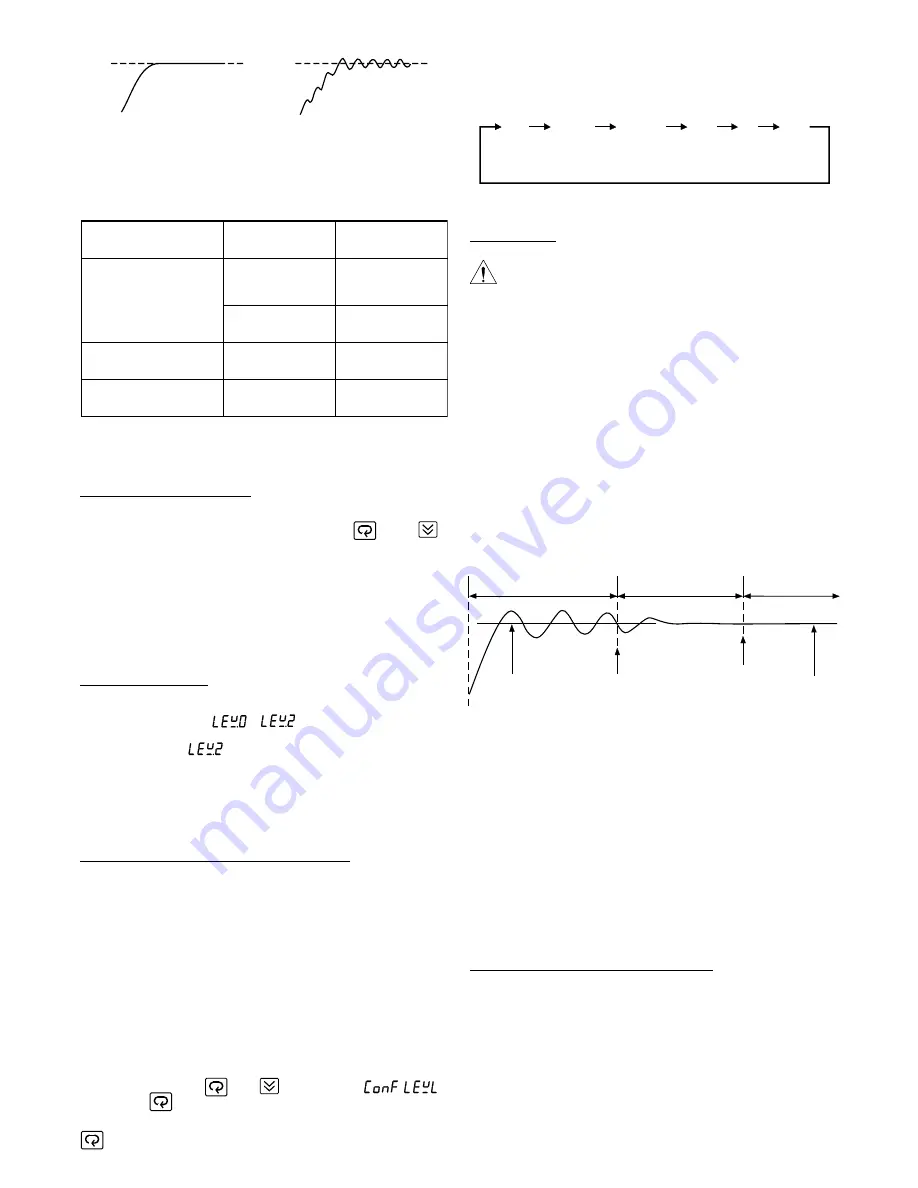
5.6 AUTO-TUNE
The process is tuned at setpoint. The process will oscillate about
the setpoint during auto-tune. Set a setpoint to a lower value if overshoot
beyond the normal process value is likely to cause damage.
The auto-tune program is applied during:
* Initial set-up
* The setpoint is changed substantially from the previous auto-tune
* The control result is unsatsifactory
The auto-tune procedures:
* To ensure that all parameters are configured correctly.
* To ensure that PB is not zero because that ON-OFF control is not allowable
to perform auto-tune.
* Set the setpoint to the normal operating process value ( or to a lower
value if overshoot beyond the normal process value is likely to cause
damage) and use normal load conditions.
* Press and hold both up and down keys for 3.2 seconds then release
together. The display is flashing during execution of auto-tune
program.
Auto-tune " teaches " the controller the main characteristics of the process.
It " learns" by cycling the output on and off. The results are measured and
used to calculate optimum PID values which are automatically entered in
nonvolatile memory.
During the second period of auto-tune the controller performs PID control
to verify the results and finally an OFST value is obtained and entered in
the memory.
To stop the auto-tune, press both up and down key then release together,
the display will stop to flash. But if the controller has entered in the
verifying period, the display will continue to flash until auto-tune is finished.
5.5.5 Configure Security Levels of Parameters
The user of the controller may often complain that the operation is so
complicated, most of parameters are unused for them and it takes long time
to get a parameter to access. You will no longer worry about this. One of
the versatile functions of this controller is that the security level for each
parameter can be redefined arbitrarily. One of four levels (Level 0, Level
1, Level 2 and Level 3) can be assigned to any parameter. The parameters
with lower level will be displayed before those parameters with higher
level as one performs scroll key. Furthermore, the level 3 parameters will
never be displayed on the front panel. Hence the user can assign level 3
to those unused parameters and assign level 0 to those most frequently
used parameters according to his requirements. Then the unused
parameter will never appear on the display to avoid confusion and the
display sequence of parameters is reconfigured.
To configure level for each parameter one can follow the flow chart in
section 6.4 by pressing and keys to reach ,
then perform key to get the desired parameter. The display indicates
the level of the parameter. Now one can change the level value for that
parameter by using up key or down key. Finally press and hold
3.2 seconds or longer, now the new level value is entered. If the
level value is unchanged the above operation for entering can be omitted.
For example: If ASP1, RAMP are configured as level 0, PB, TI, TD are
configured as leve 1, and the other parameters are configured as level 3,
the scrolling sequence of parameters will be as follows:
5.7 TUNING THE CONTROLLER MANUALLY
* To ensure that all parameters are configured correctly
* Set PB to zero. Set HYST to the smallest ( 0 °C or 0.1 °F )
* Set the setpoint to the normal operating process value ( or to a lower
value if overshoot beyond the normal process value is likely to cause
damage) and use normal load conditions.
* Switch on the power supply to the heater. Under these conditions, the
process value will oscillate about the setpoint and the following
parameters should be noted:
(1) The peak to peak variation (P) of the first cycle in °C or °F ( i.e. the
difference between the highest value of the first overshoot and the
lowest value of the first undershoot ).
Normal Cycle time
Cycle time too long
(oscillates)
The follow table provides cycle time recommendations to avoid premature
relay failure:
Note: For an ON-OFF control ( by setting PB = 0) the cycle time selection
may be ignored.
Output Device
(OUT1 or Cooling Output)
Cycle Time
( CYC or CCYC )
Load ( resistive)
Relay
20 sec or more
recommended
10 sec. minimum
2A / 250VAC
or contactor
5 sec. minimum
1A / 250VAC
Solid State Relay Drive
1- 3 sec.
SSR
Linear Current / Voltage
0.1 sec.
Phase control module
5.5.3 FAIL-SAFE Configuration
FAIL-SAFE is a Tool Program used to define an ON or OFF status of failure
for Output 1 (OUT1), Alarm 1 Output (ALM1). Press and ,
then release both keys until FAIL-SAFE is viewed in the display windows.
Then press scroll key to obtain the desired output which is shown in the
display. Now press and hold up or down key to change the status which
is shown in the display. Note that if the desired value is different from the
original one, a long scroll (pressing scroll key 3.2 sec.) has to be operated
to enter the new value before proceeding to the next Tool Parameter . If
the FAIL-SAFE status is not critical for a process as the controller fails, the
configuration of this section can be omitted.
5.5.4 LOCK Parameter
According to the flow chart shown in section 6.4, one can reach LOCK
PARA and obtain LEVEL ( ~ ) which is shown in the display
and the Lock status ( LOCK or FREE ) is shown in the display. For example,
if we select LOCK for , and press scroll key 3.2 seconds to enter the
selection, then all the parameters configured in level 2 can not be changed.
A LOCK message will be indicated in display if one attemps to change a
locked (protected) parameter.
PID+FUZZY
Verifying period
PID Control
Teaching Period
ON-OFF Control
Setpoint
Value
PB,TI,TD
Obtained
Auto-tune
finished
OFST Value
Obtained
Process
Value
SV
ASP1
RAMP
PB
TI
TD
Page 8