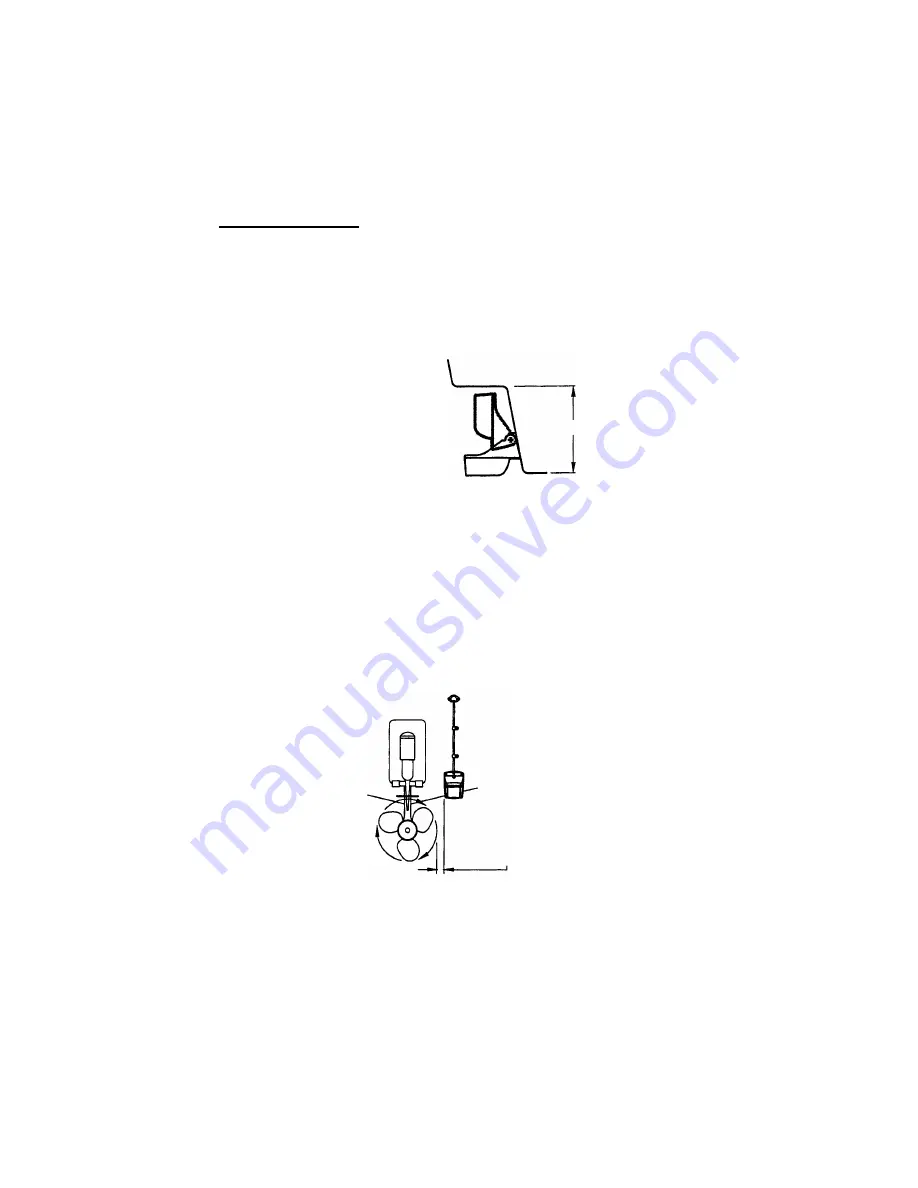
14
• Straight edge
• Marine sealant
• Pencil
• Zip-ties
• Water-based antifouling paint (mandatory in salt water).
Mounting location
To ensure the best performance, the sensor must be submerged in aeration-free and
turbulence-free water. Mount the sensor close to the centerline of the boat. On slower
heavier displacement hulls, positioning it farther from the centerline is acceptable.
Allow adequate space above the bracket for it to release and rotate the sensor up-
ward.
Height required at mounting location
Note 1:
Do not mount the sensor in an area of turbulence or bubbles: near water in-
take or discharge openings; behind strakes, struts, fittings, or hull irregularities; behind
eroding paint (an indication of turbulence).
Note 2:
Avoid mounting the sensor where the boat may be supported during trailering,
launching, hauling, and storage.
Note 3: For single drive boat,
mount on the starboard side at least 75 mm (3") be-
yond the swing radius of the propeller.
Mounting location on single drive boat
Note 4: For twin drive boat,
mount between the drives.
Height
Height without
speed sensor
191mm (7-1/2")
Height with
speed sensor
213mm (8-1/2")
75 mm (3")
minimum beyond
swing radius
Summary of Contents for DFF1
Page 1: ...NETWORK SOUNDER DFF1 OPERATOR S MANUAL www furuno com MODEL ...
Page 2: ......
Page 36: ......
Page 37: ......
Page 42: ...This page is intentionally left blank ...
Page 43: ......