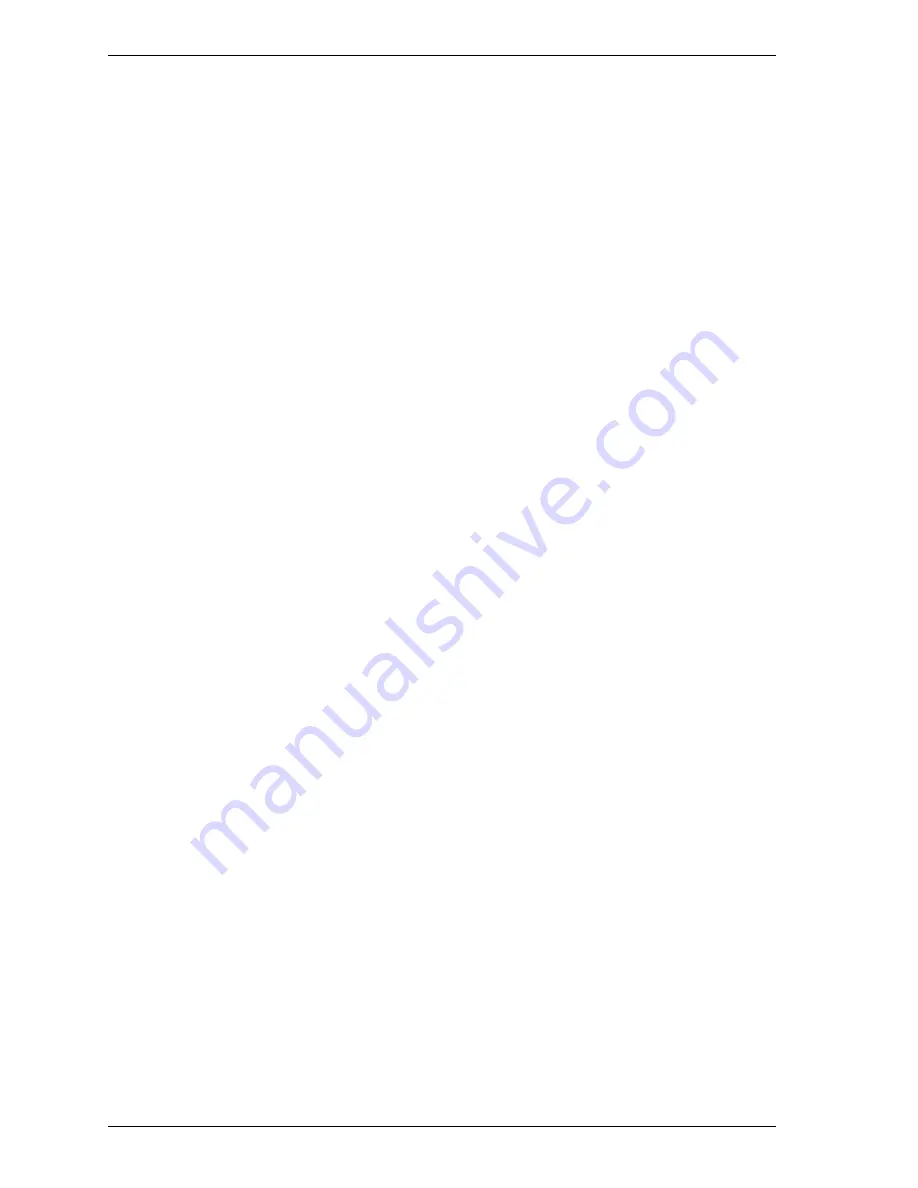
Theory of Device Operation
4.5 Self-calibration
The disk drive occasionally performs self-calibration in order to sense and
calibrate mechanical external forces on the actuator, and VCM torque. This
enables precise seek and read/write operations.
4.5.1 Self-calibration contents
(1) Sensing and compensating for external forces
The actuator suffers from torque due to the FPC forces and winds accompanying
disk revolution. The torque varies with the disk drive and the cylinder where the
head is positioned. To execute stable fast seek operations, external forces are
occasionally sensed.
The firmware of the drive measures and stores the force (value of the actuator
motor drive current) that balances the torque for stopping head stably. This
includes the current offset in the power amplifier circuit and DAC system.
The forces are compensated by adding the measured value to the specified current
value to the power amplifier. This makes the stable servo control.
To compensate torque varying by the cylinder, the disk is divided into 13 areas
from the innermost to the outermost circumference and the compensating value is
measured at the measuring cylinder on each area at factory calibration. The
measured values are stored in the SA cylinder. In the self-calibration, the
compensating value is updated using the value in the SA cylinder.
(2) Compensating open loop gain
Torque constant value of the VCM has dispersion for each drive, and varies
depending on the cylinder that the head is positioned. To realize the high speed
seek operation, the value that compensates torque constant value change and loop
gain change of the whole servo system due to temperature change is measured and
stored.
For sensing, the firmware mixes the disturbance signal to the position signal at the
state that the head is positioned to any cylinder. The firmware calculates the loop
gain from the position signal and stores the compensation value against to the
target gain as ratio.
For compensating, the direction current value to the power amplifier is multiplied
by the compensation value. By this compensation, loop gain becomes constant
value and the stable servo control is realized.
4-8
C141-E254
Summary of Contents for MHX2250BT
Page 1: ...C141 E254 01EN MHX2300BT MHX2250BT DISK DRIVES PRODUCT MANUAL ...
Page 4: ...This page is intentionally left blank ...
Page 8: ...This page is intentionally left blank ...
Page 10: ...This page is intentionally left blank ...
Page 12: ...This page is intentionally left blank ...
Page 42: ...This page is intentionally left blank ...
Page 54: ...This page is intentionally left blank ...
Page 59: ...4 3 Circuit Configuration PCA Figure 4 2 Circuit configuration C141 E254 4 5 ...
Page 74: ...This page is intentionally left blank ...
Page 86: ...Interface Figure 5 2 Example of the circuit for driving Activity LED 5 12 C141 E254 ...
Page 256: ...This page is intentionally left blank ...
Page 278: ...This page is intentionally left blank ...
Page 282: ...This page is intentionally left blank ...
Page 284: ...This page is intentionally left blank ...
Page 292: ...This page is intentionally left blank ...
Page 294: ......
Page 295: ......
Page 296: ......