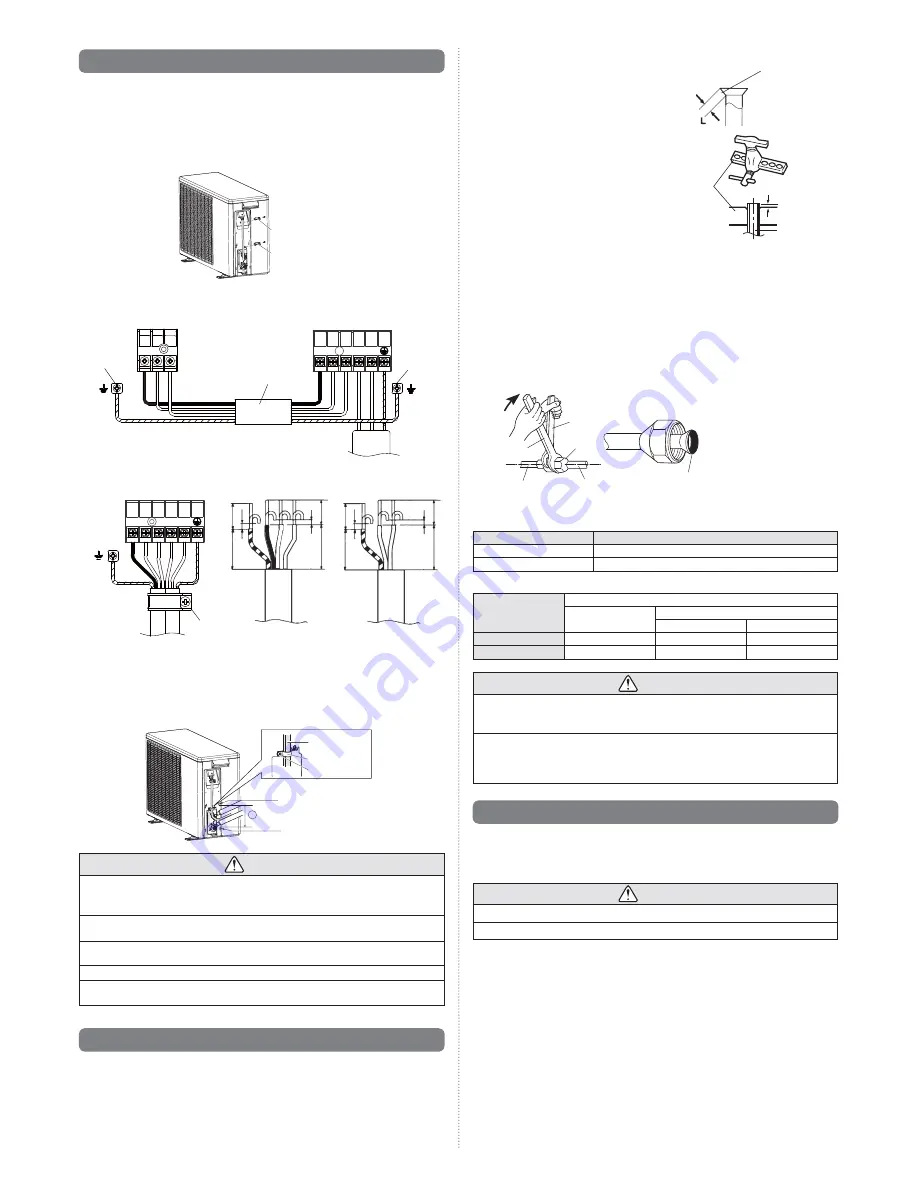
En-3
5.2. Outdoor unit wiring
(1) Remove the outdoor unit Switch cover A, B.
(2) Remove the outdoor unit Cord clamp and Nylon clamp.
(3) Bend the end of the cord as shown in the
¿
gure.
(4) Connect the end of the connection cord fully into the terminal block.
(5) Fasten the sheath with a cord clamp.
(6) Fasten the sheath with a nylon clamp.
(7) Install the Switch cover A, B.
Cord clamp
Nylon clamp
N
L
3
2
1
1 2
3
Outdoor unit terminal block
Indoor unit terminal block
Connection cord
Earth screw
Earth screw
Power supply Cord
N
L
3
2
1
25mm
1
2mm
5mm
5mm
12mm
20mm
Cord clamp
Earth
screw
20mm
1
2mm
5mm
5mm
12mm
20mm
Connection Cord
Power supply Cord
Connection cord wiring
Run the connection cord to the rear of the outdoor unit within the
A
range of the arrows
shown in the figure.
(The Switch cover B becomes difficult to install.)
A
Connection and
Power supply cord
Nylon clamp
Screw
HOLE
HOLE
CAUTION
Match the terminal block numbers and connection cord colors with those of the indoor
unit.
Erroneous wiring may cause burning of the electric parts.
Connect the connection cords
¿
rmly to the terminal block. Imperfect installation may
cause a
¿
re.
Always fasten the outside covering of the connection cord with the cord clamp. (If the
insulator is chafed, electric leakage may occur.)
Securely earth the power cord.
Do not use the earth screw for an external connector. Only use for interconnection
between two units.
5.3. Connecting the piping
CONNECTION
(1) Install the outdoor unit wall cap (supplied with the optional installation set or pro-
cured at the site) to the wall pipe.
(2) Connect the outdoor unit and indoor unit pip-
ing.
(3) After matching the center of the
À
are surface
and tightening the nut hand tight, tighten the
nut to the speci
¿
ed tightening torque with a
torque wrench. (Table 1)
FLARING
(1) Cut the connection pipe to the necessary
length with a pipe cutter.
(2) Hold the pipe downward so that cuttings will
not enter the pipe and remove the burrs.
(3) Insert the flare nut onto the pipe and flare
the pipe with a
À
aring tool.
Insert the flare nut (always use the flare nut
a t t a c h e d t o t h e i n d o o r a n d o u t d o o r u n i t s
respectively) onto the pipe and perform the
À
are
processing with a
À
are tool.
Use the special R410A
À
are tool, or the conventional (for R22)
À
are tool.
When using the conventional
À
are tool, always use an allowance adjustment gauge and
secure the A dimension shown in table 2.
BENDING PIPES
(1) When bending the pipe, be careful not to crush it.
(2) To prevent breaking of the pipe, avoid sharp bends.
Bend the pipe with a radius of curvature of 70mm or over.
(3) If the copper pipe is bend the pipe or pulled to often, it will become stiff. Do not
bend the pipes more than three times at one place.
Tighten with two wrenches.
Torque
wrench
Wrench (
¿
xed)
Flare nut
Indoor unit pipe
Connection
pipe
To prevent gas leakage, coat the
À
are
surface with refrigerator oil.
Table 1
Flare nut size and tightening torque
Flare nut
Diameter (mm)
✕
Torque (N•m
)
6.35 mm dia.
17
✕
16 ~ 18
9.52 mm dia.
22
✕
32 ~ 42
Table 2
Pipe outside diameter
Pipe outside
diameter
A (mm)
Flare tool for
R410A, clutch type
Conventional (R22)
À
are tool
Clutch type
Wing nut type
ø 6.35 mm (1/4")
0 to 0.5
1.0 to 1.5
1.5 to 2.0
ø 9.52 mm (3/8")
0 to 0.5
1.0 to 1.5
1.5 to 2.0
CAUTION
Fasten a
À
are nut with a torque wrench as instructed in this manual. If fastened too
tight, the
À
are nut may be broken after a long period of time and cause a leakage of
refrigerant.
During installation, make sure that the refrigerant pipe is attached
¿
rmly before you run
the compressor. Do not operate the compressor under the condition of refrigerant piping
not attached properly with 2-way or 3-way valve open. This may cause abnormal pres-
sure in the refrigeration cycle that leads to breakage and even injury.
5.4. Air purge
Always use a vacuum pump to purge the air.
Refrigerant for purging the air is not charged in the outdoor unit at the factory.
Close the high pressure side valve of the gauge manifold fully and do not operate it during
the following work.
CAUTION
Refrigerant must not be discharged into atmosphere.
After connecting the piping , check the joints for gas leakage with gas leak detector.
(1) Check if the piping connections are secure.
(2) Check that the stems of 2-way valve and 3-way valve are closed fully.
(3) Connect the gauge manifold charge hose to the charging port of the 3-way valve (side
with the projection for pushing in the valve core).
(4) Open the low pressure side valve of the gauge manifold fully.
(5) Operate the vacuum pump and start pump down.
(6) Slowly loosen the
À
are nut of the 3-way valve and check if air enters, then retighten
the
À
are nut.
(When the
À
are nut is loosened the operating sound of the vacuum pump changes
and the reading of the compound pressure gauge goes from minus to zero.)
(7) Pump down the system for at least 15 minutes, then check if the compound pressure
gauge reads -0.1 MPa (-76 cmHg, -1 bar).
(8) At the end of pump down, close the low pressure side gauge of the gauge manifold
fully and stop the vacuum pump.
(9) Slowly loosen the valve stem of the 3-way valve. When the compound pressure
gauge reading reaches 0.1-0.2 MPa, retighten the valve stem and disconnect the
charge hose from the 3-way valve charging port.
Check if [L] is
À
ared uniformly and
is not cracked or scratched.
Die
A
Pipe
9319205007_IM_EN.indd 3
12/29/2010 9:16:49 AM