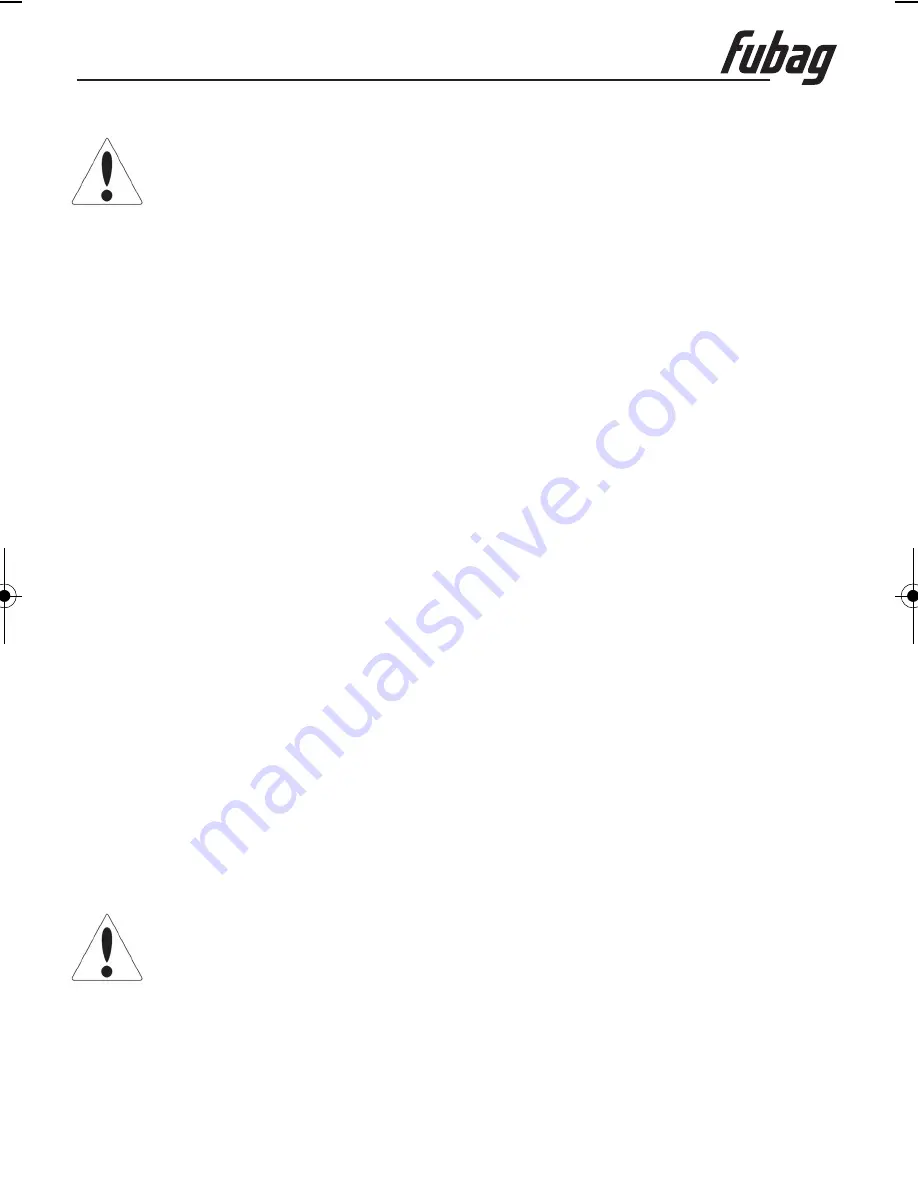
O
m
perator's
anual
WARNING! BEFORE USING THE WELDING MACHINE READ THE INSTRUCTION
MANUAL CAREFULLY!
FOR QUALIFIED AND SPECIALLY TRAINED PERSONS
ONLY AFTER PROPER READING OF THIS MANUAL IS ALLOWED TO USE AND TO
MAINTAIN THIS WELDING MACHINE.
The detailed description, safety rules and all required information necessary for proper operation
and maintenance of FUBAG welding machine are provided below. Keep this instruction manual by
machine and refer to it by any doubts concerning safety operation, maintenance storage and
handling of FUBAG welding machine.
1. Safety peration
o
-
-
-
-
-
-
-
-
-
-
-
-
-
-
-
It is highly recommended always to follow the safety rules. Wear protective clothes and
special means to avoid injuries to eyes and skins.
Use the welding mask or special protective glasses while working with the welding
machine. Only by viewing through the filter lens on the welding mask your eyes are
secured by your operation.
Prevent the sparks and spatter from harming your body.
Under no circumstance allow any part of your body to touch the welder's output bipolarity
(torch and work piece).
Do not operate under water or more humid place.
Fumes and gases produced when welding are hazardous to health. Make sure to work in
places where there are exhaust or ventilation facilities to keep fumes or emissions away
from the breathing zone.
Please remember to keep arc rays away from the other nearby people when welding. This
is only due to the interference from arc rays.
There will be high temperature when welding work piece, so please don't directly touch on it
No touching on the output connection or any other electrification parts while welding.
No touching on the electrification parts after turning on the power. Cut off the power supply
after operation or before leaving the welding site.
No welding in the dangerous site where easily get an electrical shock.
No welding for the container loaded inflammable or explosive materials.
Safe measures should be adoptted while operating in high place to avoid accident.
No entering the welding site for persons not concerned.
Welders possible have electromagnetism and frequency interference, so keep away people
with heart pace or the articles which can be interfered by electromagnetism and frequency.
WARNING.
The welder voltage is always higher, so the safety precaution should be taken
before repair to avoid accidental shock. Switch off the power supply before each type of
maintenance work. The untrained people are not allowed to make maintenance of the
machine.
www.fubag.ru
- 1 -
Summary of Contents for INMIG 200 Plus
Page 15: ...www fubag ru O m perator s anual 5 1 10 Troubleshooting...
Page 17: ...www fubag ru FUBAG FUBAG 1 17...
Page 18: ...10 40 50 15 1 0 300 www fubag ru 1 8...
Page 21: ...www fubag ru 21 5 S...
Page 22: ...www fubag ru 22 6 H 0 7 10 40 50 IP21 X 1 2 I I 1 U 2 U...
Page 23: ...www fubag ru 23 MIG MAG 220 380 1 2 1 5 2 1 220 INMIG 200 36...
Page 24: ...www fubag ru 24 1 2 3 1 2 IG...
Page 26: ...www fubag ru 26 10 20 MIG 20 14 GAS ON 14 GAS OFF S P O T 14 SPt ADJ V V V V...
Page 27: ...www fubag ru 27 14 12 12 V b 22 0 6 0 8 0 9 1 0 1 2 15 19 2 4 SPOT b...
Page 28: ...www fubag ru 8 2 20 14 GAS ON 14 GAS OFF U b 1 0 15 MMA b V V...
Page 29: ...www fubag ru 9 2 c VRD VRD VRD 10 12 7 20 22 18 TIG b TIG 9 2 5 25 55 90 O O...
Page 30: ...www fubag ru 30...
Page 31: ...www fubag ru 31 10 15 15...
Page 32: ...www fubag ru 32 11 12 3 1 1 1 1 1 1 1 1 25 55 90 LIFT O O C C...