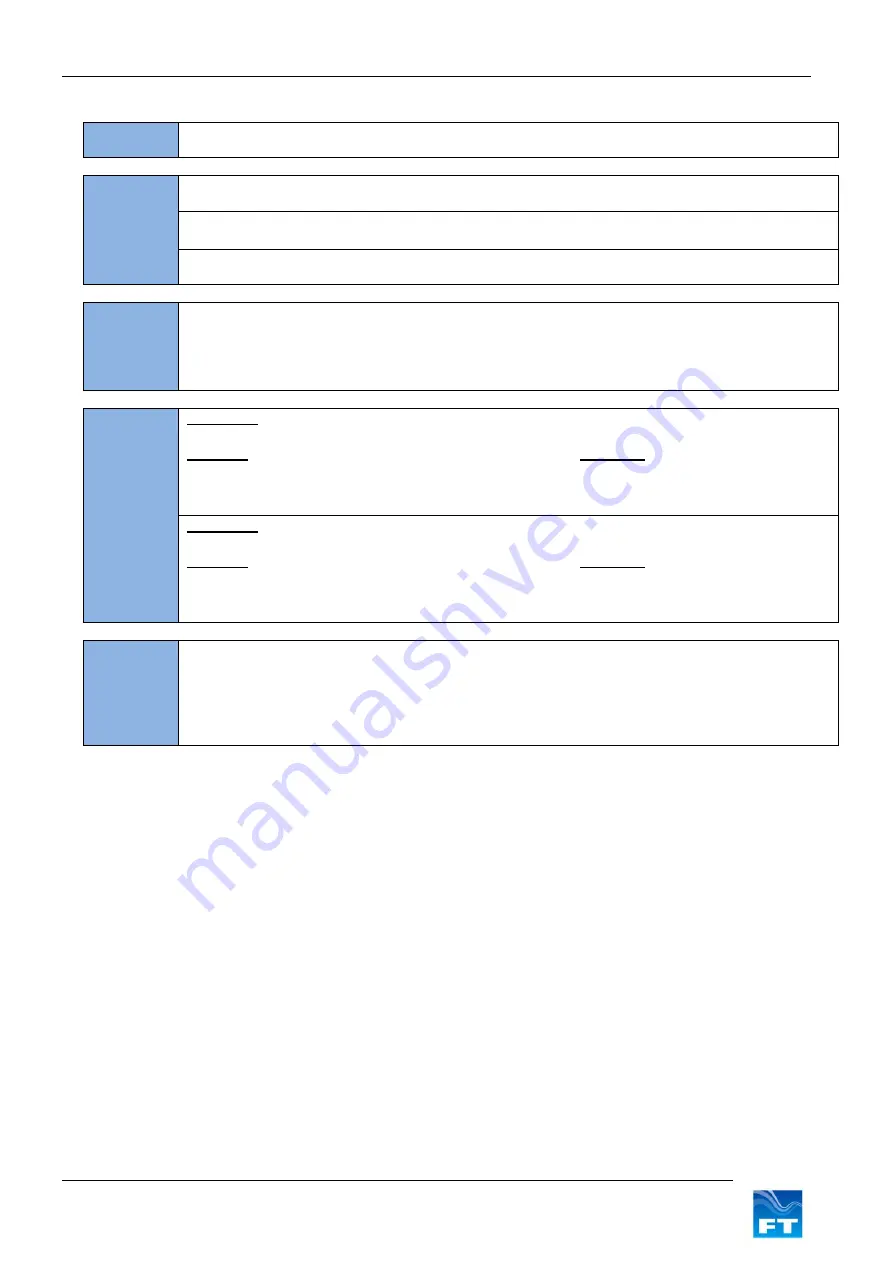
Section 6
Parameter Settings
46
FT205EV Wind Sensors
– User Manual
6.4.4
AT.3 Set or Query the Acoustic Temperature Filter Length
Command
Parameter
AT (filter length)
Command
Syntax
SET Sensor:
$<listenerID>,ATF<filter length>*<checksum><cr><lf>
$aa,ATFxxc*hh<cr><lf>
QUERY Sensor:
$<listenerID>,AT?F*<checksum><cr><lf>
$aa,AT?F*hh<cr><lf>
Sensor output:
$<talkerID>,AT=<filter length>*<checksum><cr><lf>
$aa,AT=xxc*hh<cr><lf>
Parameters
<filter length>
00S to 50S,
01M to 10M
Time constant of the acoustic temperature filter in seconds (S) or minutes
(M). Supported settings are 00S (to disable the filter), then ten second
increments from 10S up to 50S, then one minute increments from 01M to
10M. (Factory Default Setting = 01M)
Examples
Example 1
Set the filter time constant to 40 seconds. Verify that the command has been accepted.
Message
Comment
$01,ATF40S*//<cr><lf>
Set 40s time constant
$01,AT?F*//<cr><lf>
Query filter time constant
$WI,AT=40S*4D<cr><lf>
Sensor response
Example 2
Set the filter time constant to 2 minutes. Verify that the command has been accepted.
Message
Comment
$01,ATF02M*//<cr><lf>
Set 2 minute time constant
$01,AT?F*//<cr><lf>
Query filter time constant
$WI,AT=02M*55<cr><lf>
Sensor response
Description
Use this command to alter the time constant of the acoustic temperature filter. The filter can be
disabled by setting the time constant to zero (00S). Valid time constants are ten second steps
from 10S to 50S and then one minute steps from 01M to 10M.