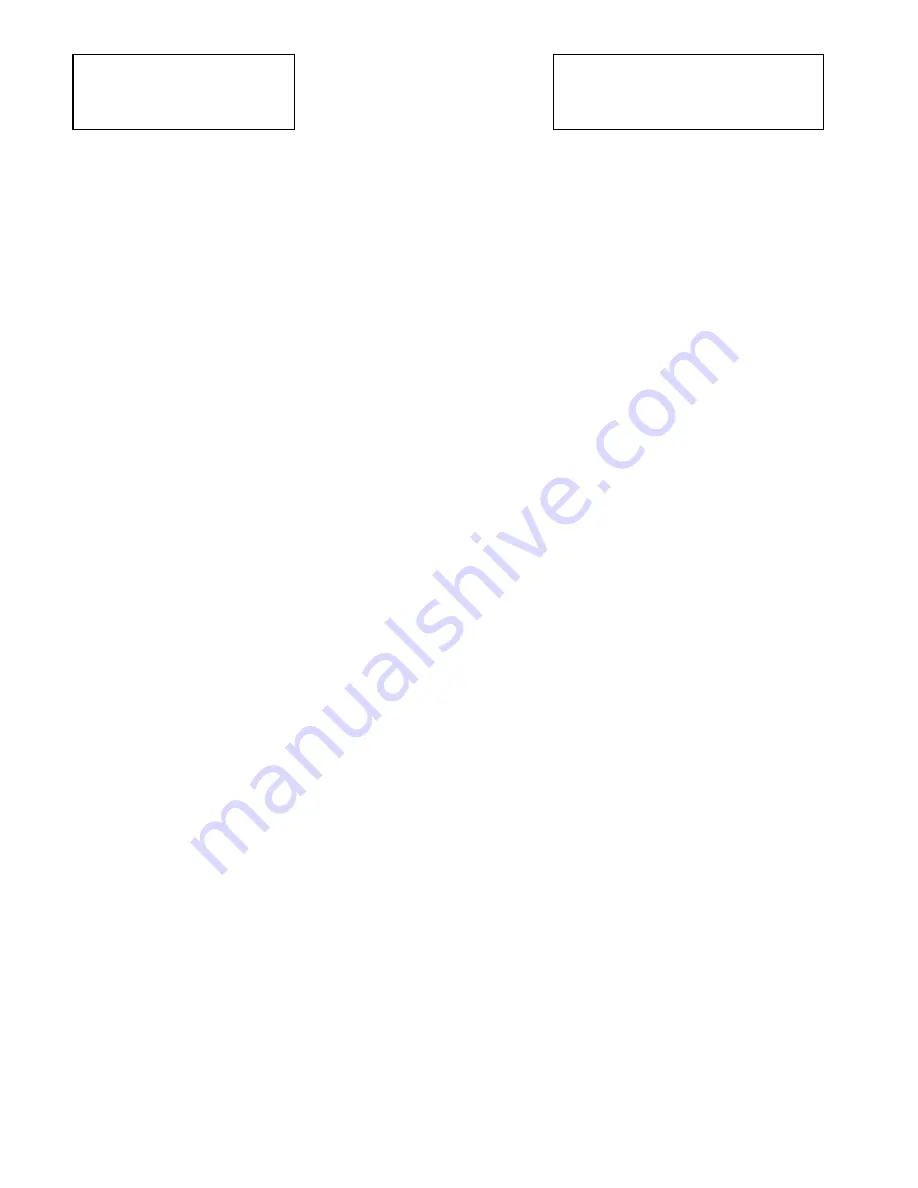
FSD International
Commander 115 TC
Pilot Operating Handbook
- 48 –
Copyright© 2008 by FSD International. All rights reserved.
For use with Microsoft Flight Simulator only. Not to be used for real-world aviation.
WING FLAPS
Long span single slotted wing flaps are provided Wing flap position is controlled by a three-position
switch mounted immediately to the left of the right control wheel. Flap position is displayed on an
electrical indicator I mounted above the flap switch. Power from the electric motor is transmitted to
the flaps through a jackscrew connected to a torque tube, and from the torque tube to the flaps
with push-pull rods. To extend the wing flaps, the wing flap switch must be depressed and held
DOWN until the desired degree of extension is reached After the desired flap extension is obtained,
releasing the switch allows it to return to the center OFF position. When flap retraction is
necessary, place the switch up. The switch will remain in the UP position without manual assistance
due to an over-center design within the switch. With the flaps extended in flight, placing the flap
switch UP will retract the flaps in approximately 7 seconds. Gradual flap retraction can be
accomplished by intermittent operation of the flap switch to UP. Normal full flap extension in flight
will require approximately 7 seconds. After the flaps reach maximum extension or retraction, limit
switches will automatically shut off the flap motor; however, when the flaps reach the fully
retracted position. the wing flap switch should be returned to the center-off position. An additional
limit switch is installed on the flap motor drive to activate the gear warning system when flaps are
extended 25 degrees or more with the landing gear retracted No appreciable change in elevator
trim is required over the full flap extension range, however, minor changes in trim may be required
depending on airspeed and airplane loading. Normally there will be a slight nose down trim change.
LANDING GEAR
The airplane is equipped with a retractable hydraulically operated, tricycle landing gear that
includes a steerable nose wheel and self-adjusting disc brakes on the main landing gear wheels.
Landing shocks are absorbed in the nose gear by a conventional oleo strut assembly, and by an
oleo strut connecting rod arrangement connected to the trailing arm of the main landing gear. Nose
wheel steering is controlled by a cable-pulley system attached to the nose gear and to the
rudder/brake pedal and is actuated by depressing the rudder/brake pedals from either pilot's
position. The single-disc, dual piston, hydraulic brakes are operated by individual master brake
cylinders attached to the rudder/brake pedals. The brakes are actuated by applying toe pressure to
the top of the rudder/brake pedals. The airplane is also equipped with a parking brake system
which operates from the master brake cylinders and is actuated by a parking brake control knob. A
shimmy damper is attached to the fixed and movable portions of the nose gear strut to provide a
dampening action on the gear. An emergency extension valve, located on the left side of the center
console, is used for emergency extension of the gear. This valve bypasses hydraulic fluid directly to
the reservoir, allowing the gear to drop by gravity; gear extension is assisted by down springs. The
emergency gear extension knob is spring-loaded to prevent accidental operation and must be
pulled out and then pushed down to operate.
The main landing gear retracts inward and upward into wheel wells in the lower side of the wing.
The nose landing gear retracts aft and upward into the wheel well. Mechanically operated doors
connected to the landing gear by link assemblies open and close during the extension and
retraction cycle. A flat surface on the fixed portion of the nose gear keeps the landing gear
centered when the gear is retracted. Retraction and extension of the landing gear is controlled by
an electro-hydraulic power pack that is actuated by the position of the landing gear selector switch
mounted on the instrument panel. When the landing gear selector switch is placed in the UP
position, the landing gear retracts until the gear up pressure switch is actuated. When the gear up
pressure switch is actuated, the hydraulic power pack pump is shut off and all three gears are
retained the up-lock position by a hydraulic pressure lock. A loss of 250 PSI hydraulic pressure will
energize the hydraulic power pack and buildup pressure to the pressure switch setting.