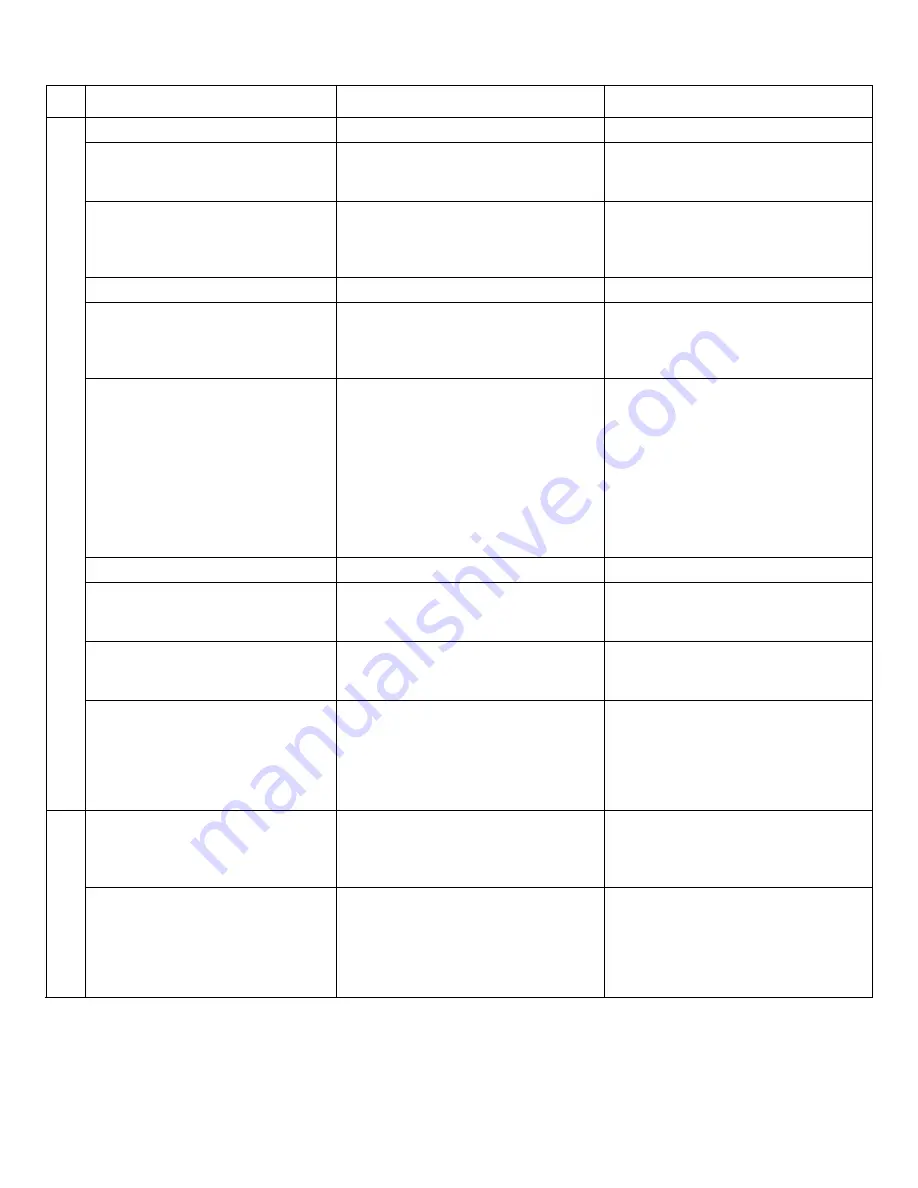
CAP-600
35
TROUBLESHOOTING
SYMPTOMS CAUSES REMEDIES
Flywheel rotation in wrong direction Incorrect connection of motor terminal
Re-arrange terminal connection.
Overheating of bearings
1. Insufficient lubrication.
2. Bad lubrication system.
3. Crankshaft bearings to tight.
1. Add lubrication oil.
2. Remove and examine the system.
3. Readjust load on bearings.
Flywheel rotation slows down
1. Heavy lubrication oil.
2. Drop in voltage.
3. Belts
slipping.
1. Refill with lighter lubrication oil.
2. Contact power company or install
a transformer.
3. Tighten
belts
Severe vibration
Bent crankshaft
Remove & Replace
Abnormal noise
1. Loose valve assembly.
2. Piston hits cylinder cover.
3. Worn connecting rod bearing.
1. Tighten valve bolt and lock nut.
2. Check piston & rod assembly for
excessive wear.
3. Replace bearing.
Pressure cannot be built up or only
up to a certain extent
1. Worn valve plate.
2. Valve springs have lost their
temper.
3. Dirt on the valve plate.
4. Leaks from safety valve.
5. Leaks from bolt holes.
6. Uneven valve seat surface.
7. Excessive blow by on piston rings.
8. Bad packing (gasket to thick).
9. Excessive air leaks.
1. Repair or replace valve plate.
2. Replace valve springs.
3. Remove and clean it.
4. Repair or replace safety valve.
5. Tighten the nuts even with
packing.
6. Remove and lap the surface.
7. Replace with new ones
8. Replace packing (gasket).
9. Eliminate air leaks.
Inaccuracy of pressure gauge
Pressure gauge damaged.
Replace.
Excessive oil consumption
1. Worn piston ring
2. Worn
piston.
3. Worn
cylinder.
1. Replace.
2. Replace.
3. Replace.
Slipping of belts
1. Working pressure too high.
2. Improper belt tension.
3. Worn
belt.
1. Lower working pressure.
2. Adjust belt tension.
3. Replace with new ones.
WHEN COMPRESSOR CAN BE STARTED
Overheating of electric motors
1. Overloading of motor due to
excessive working pressure
(higher than stipulated pressure).
2. Burnt
piston.
3. Burnt bearing metals.
4. Drop of voltage.
1. Lower working pressure.
2. Rebuild
compressor.
3. Rebuild
compressor.
4. Contact power company or install
a transformer
Unit will not start
1. Breakdown of electric current.
2. Line
failure.
3. Malfunction of motor
1. Contact power company.
2. Examine the line. Replace with
new wiring.
3. Contact motor manufacturer.
WHEN COMPRESSOR
CANNONT BE STARTED
Fuse tends to blow
1. Incorrect size.
2. Wrong
connections
3. Overloading of motor.
4. Overloading of motor due to leaks
of outlet valve.
5. Crankshaft too tight.
1. Replace with correct size.
2. Change
connections.
3. Eliminate the loading.
4. Remove and repair outlet valve.
5. Remove crankshaft and examine
it for cause.
CURTIS-TOLEDO
CUSTOMER SERVICE (314) 383-1300
Summary of Contents for CA series
Page 12: ...CAP 600 12 AIR COOLED SINGLE STAGE MODELS ES 05 ES 10 ES 20 ...
Page 20: ...CAP 600 AIR COOLED SINGLE STAGE MODEL ES 150A 18 ...
Page 22: ...CAP 600 AIR COOLED SINGLE STAGE MODEL ES 150B 18A ...
Page 24: ...CAP 600 20 AIR COOLED TWO STAGE MODELS E 11 E 23 ...
Page 30: ...CAP 600 AIR COOLED TWO STAGE MODEL E 25 25A ...
Page 34: ...CAP 600 26 AIR COOLED TWO STAGE MODEL E 35 ...
Page 36: ...AIR COOLED TWO STAGE MODEL E 57 E57A CAP600 28 ...
Page 39: ...CAP 600 31 VALVE PLATES DESIGNS FOR E 57 COMPRESSOR ...
Page 47: ...CAP 600 NOTES 39 ...