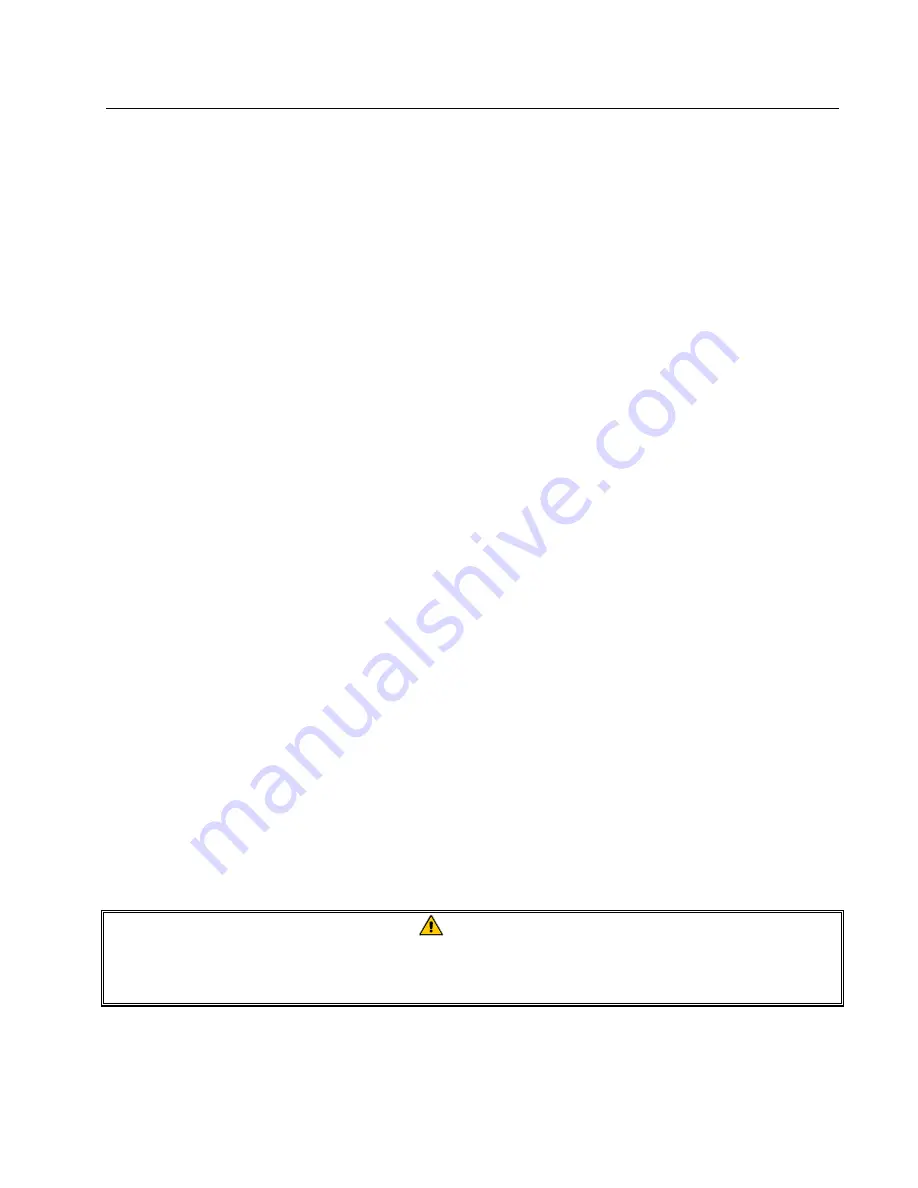
YFG255 SERIES GAS RETHERMALIZERS
CHAPTER 1: SERVICE PROCEDURES
1-15
1.6.2 Improper Burner Functioning (cont.)
If popping occurs only during peak operating hours, the problem may be incorrect or fluctuating gas
pressure. Verify that the incoming gas pressure (pressure to the gas valve) is in accordance with the
appropriate CE or Non-CE requirements listed in the Installation and Operation manual that came
with the rethermalizer, and that the pressure remains constant throughout all hours of usage. Refer
to Adjusting Burner Manifold Pressure in Section 1.4 if burner manifold pressure is suspected of
being incorrect.
If popping is consistent during all hours of operation, verify that the pilot is properly positioned
above the burner orifice and that the pilot pressure is correct. Correct pilot pressure is indicated by a
flame 1 to 1½" long. Also verify that ignitor is properly adjusted (electrode tip 1/8" from pilot hood
corner).
Clogged burners and/or burner orifices are also likely causes of delayed ignition. Clogged burners
are indicated by uneven flame or partial flame on the burner face. Clogged orifices are indicated by
no flame.
Another cause of popping is an insufficient air supply or drafts that are blowing the pilot flame away
from the burner. Check for "negative pressure" conditions in the kitchen area. If air is flowing into
the kitchen area, this indicates that more air is being exhausted than is being replenished and the
burners may be starved for air.
If the rethermalizers gas and air supplies are okay, the problem most likely is with one of the
electrical components. Examine the ignition module for signs of melting/distortion and/or
discoloration due to excessive heat build-up in the rethermalizer. (This condition usually indicates
improper flue performance.). Also, examine the controller for the same conditions. A melted or
distorted ignition module is automatically suspect and should be replaced, but unless the condition
causing excessive heat in the rethermalizer is corrected, the problem is likely to recur.
Next, ensure the ignition wire is tightly connected at both ends and examine it for obvious signs of
damage. Again, if damage is due to excessive heat in the rethermalizer, that problem must also be
corrected.
Check for proper operation by disconnecting the wire from the ignitor, inserting the tip of a
screwdriver into the terminal, and holding it near the frame of the rethermalizer as the power switch
is placed in the "ON" position. A strong, blue spark should be generated for at least 60 seconds.
DANGER
MAKE SURE YOU ARE HOLDING THE INSULATED HANDLE OF THE SCREWDRIVER
AND NOT THE BLADE. THE SPARKING CHARGE IS APPROXIMATELY 25,000
VOLTS.
Ensure the gap setting of the ignitor is correct (electrode tip 1/8" from pilot hood corner).
Burners lighting on the left side only
may be caused by a trailing pilot problem or improper burner
manifold pressure.