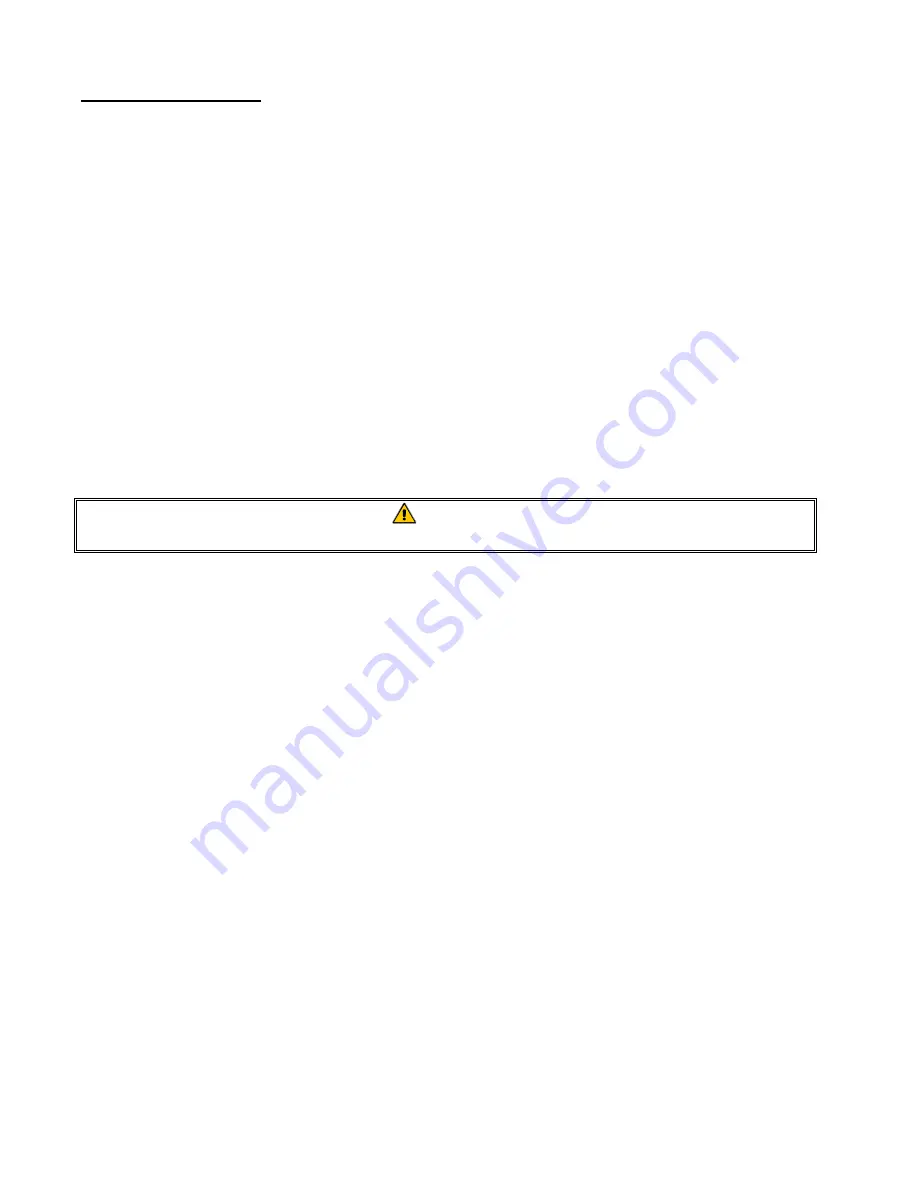
1-14
ALL OTHER VALVES
4.
Carefully unscrew the valve from the manifold.
NOTE:
Some models may have the valve
attached to the manifold by means of a pipe union. In such cases, remove the valve by
uncoupling the union.
5.
Remove all fittings from the old gas valve and install them on the replacement valve, using
Loctite
®
PST56765 or equivalent pipe thread sealant.
6.
Reconnect the gas valve assembly to the fryer using Loctite
®
PST56765 or equivalent pipe
thread sealant, and reattach the flexible gas line(s), enrichment tube(s), and the vent tube (on
non-CE units). Reconnect the high-limit thermostat wires and drain safety wires to the valve.
7.
Reconnect the fryer to the gas supply and open the cut off valve. Apply a solution of soapy
water around each connection to check for gas leaks. Eliminate any that are found.
8.
Reconnect the fryer to the electrical power supply and check for proper operation.
1.6.8 Replacing a Burner Assembly
DANGER
Drain the frypot or remove the handle from the drain valve before proceeding further.
1.
Disconnect the unit from the electrical and gas supplies.
2.
Remove the combustion air blower by following the instructions in Section 1.6.6.
3.
Remove the four nuts from the air plenum assembly and pull the assembly straight out toward
you until it clears the burner tubes.
NOTE:
On a dual-vat fryer, it will be necessary to remove the drain valve handles before the
plenum can be removed.
NOTE:
If the flexible oil return lines are blocking the plenum, carefully bend them upward
enough to clear the plenum.
4.
Disconnect the ignition cable from the ignitor by grasping its boot and pulling gently toward
you. Disconnect the flame sensor wire from the ignitor by gently pulling its push-on terminal
from the terminal strip on the ignitor.
5.
Disconnect the flexible gas lines from the burner orifice and the enrichment tube from the ignitor
assembly.
6.
Remove the four ¼-inch nuts securing the outer front covers to the frypot assembly.
7.
Remove the sheet metal screws at the top of the outer front covers and pull the covers straight
out toward you until clear of the mounting studs.
Summary of Contents for FOOTPRINT H50
Page 24: ...1 19 Disassembling A Frypot Full vat Illustrated Spacers Spacer 10 2 3 4 5 6 7 8 1 11 9...
Page 47: ...1 42 1 11 2 Pro H50 55 Series Fryer Single Full vat 805 1675...
Page 48: ...1 43 1 11 3 Pro H50 55 Series Fryer Single Dual vat...
Page 49: ...1 44 1 11 4 Pro H50 55 Series Fryer Single CE...
Page 50: ...1 45 1 11 5 Pro H50 55 Series Fryer Single FAST ready...
Page 52: ...1 47 1 11 6 3 FPPH 250 255 450 455 Transformer Filter Box 8051340C...
Page 53: ...1 48 1 11 6 4 FPPH 350 355 Transformer Filter Box...
Page 54: ...1 49 1 11 7 Modular Basket Lift 100 120V 1 2 4 3 5 6 12 7 8050518E...
Page 67: ...2 11 2 5 Drain Filtration and Oil Return System Components 2 5 1 Filtration System Components...
Page 69: ...2 13 2 5 2 Drain Valves and Associated Components...
Page 79: ...2 23 2 6 Electronics and Electrical Components for Controllers Page 2 10 2 6 1 Component Boxes...
Page 86: ...2 30 2 7 2 Dual Vat Frypot Components...