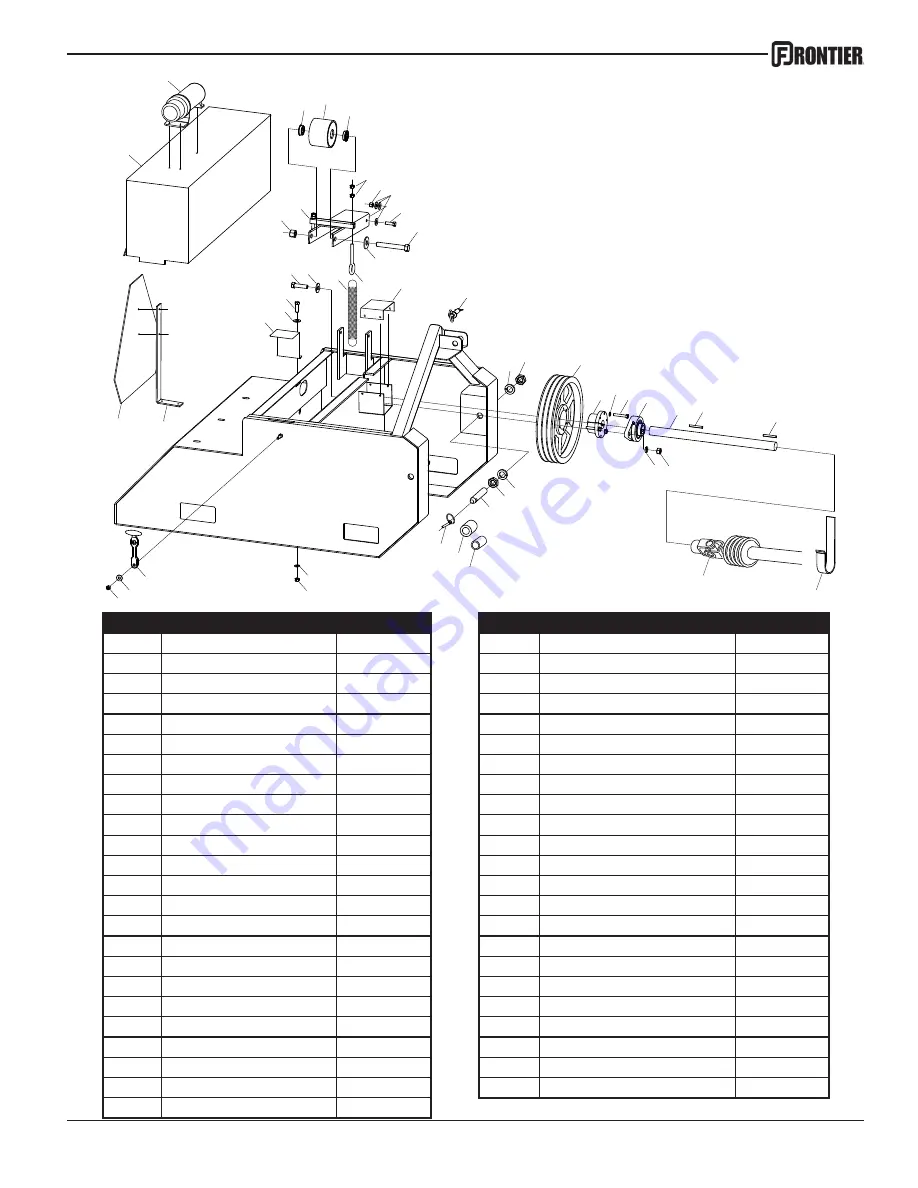
15
2
3 4
3
5
6 7
8
9
10
11
12
13
14
14
15
15
16
17 1819 20
21 22
23
24
25
26
27
29
28
30
31
32
33
36
37
38
39
40
41
42 43 44
45
46
35
34
1
Ref#
Description
Part#
Ref#
Description
Part#
1
Belt Shield
5PQ902025
24
Nut, 1/2
5PQ000940
2
Owner’s Manual Canister
5PQ503050
25
Lock Washer, 1/2
5PQ000840
2a
Operator’s/Parts Manual
5PQ990102
26
Complete PTO Shaft
5PQ900139
3
Insert Bearing
5PQ900150
27
PTO Shaft Cradle
5PQ900862
4
Idler Roller
5PQ902023
28
Lift Arm Pin w/ Nut & Washer
5PQ900110
5
Nut, 3/8
5PQ000915
29
Quick Hitch Bushing, 1” OD
5PQ903145
6
Locknut, 3/8
5PQ003000
30
Quick Hitch Bushing, 1.25” OD
5PQ903146
7
Flatwasher, 3/8
5PQ001035
31
Lynch Pin
5PQ500219
8
Bolt, 3/8 x 1-1/4
5PQ000275
32
Lock Washer, 3/8
5PQ000820
9
Bolt, 5/8 x 4-1/2
5PQ000645
33
Nut, 3/8
5PQ000915
10
Flatwasher, 5/8
5PQ001075
34
Rubber T-Handle
5PQ400092
11
Eye Bolt, 3/8 x 3-1/4
5PQ902001
35
Flatwasher, 5/16
5PQ001030
12
PTO Guard
5PQ900857
36
Nut, 5/16
5PQ000910
13
Hitch Pin
5PQ903143
37
SMV Triangle
5PQ507166
14
Lock Washer, 7/8
N/A
38
SMV Mounting Bracket
5PQ900861
15
Jam Nut, 7/8
N/A
39
Jack Shaft Shield
5PQ900019
16
Pulley, 12” 3-Groove
5PQ900113
40
Flatwasher, 3/8
5PQ001035
17
Pulley Bushing w/ Bolts
5PQ900115
41
Bolt, 3/8 x 1
5PQ000270
18
Lock Washer, 5/16
N/A
42
Bolt, 1/2 x 2
5PQ000452
19
Bolt, 5/16 x 2
N/A
43
Flatwasher, 1/2
5PQ001055
20
Flange Bearing, 1-1/4
5PQ900112
44
Tension Spring
5PQ900162
21
Jack Shaft
5PQ900041
45
Locknut, 5/8
5PQ000972
22
Key, 3/8 x 3/8 x 2
5PQ400857
46
Idler Arm
5PQ902024
23
Key, 1/4 x 1/4 x 2
5PQ400587
WC1105 Base Assembly
Summary of Contents for wc1105
Page 1: ...WOOD CHIPPER O P E R A T O R S M A N U A L WC1105 5PQ990102 8 08 2012...
Page 2: ......
Page 16: ...14 Illustrated Parts Breakdowns...
Page 21: ...19 NOTES...
Page 22: ...20...
Page 23: ......
Page 24: ......