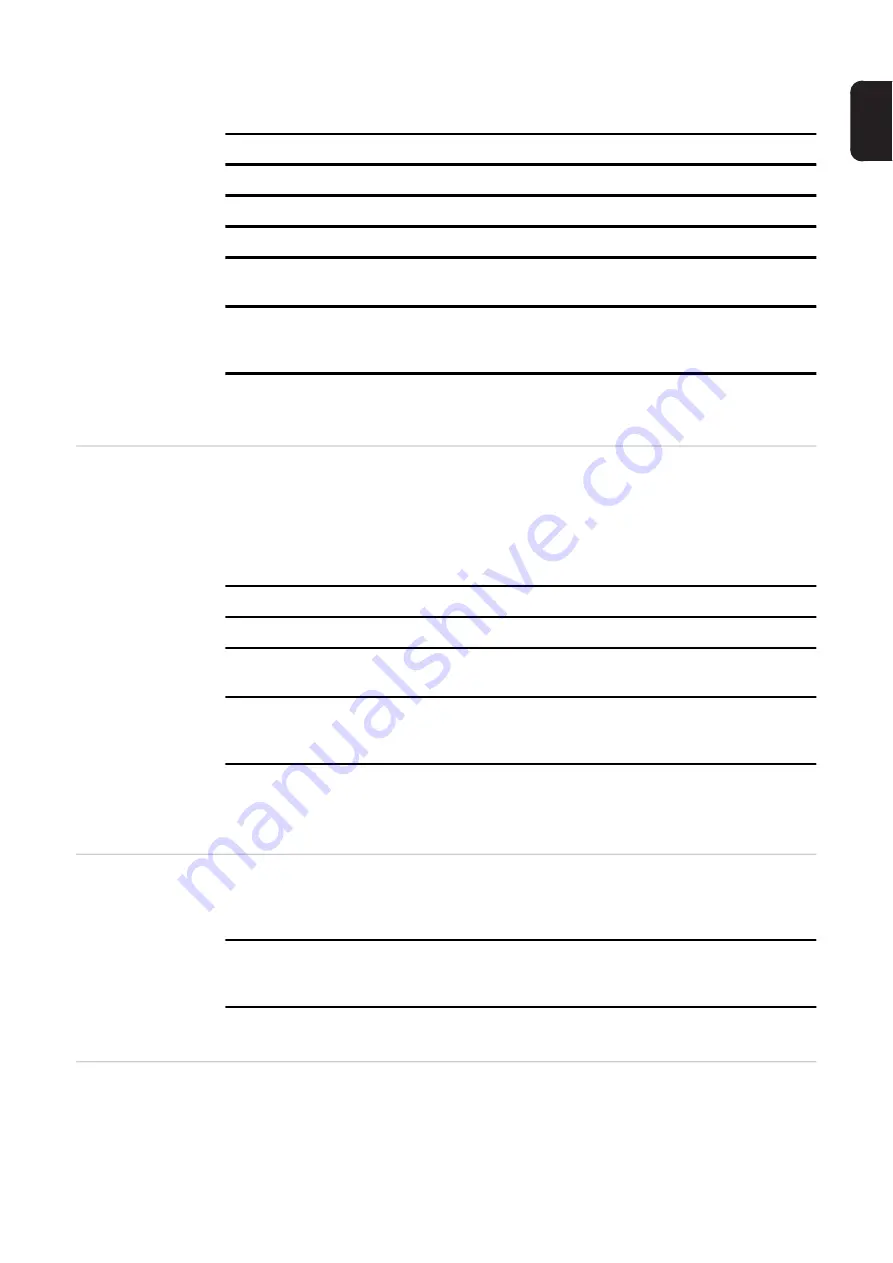
11
EN
Operating the device on a grid without a ground conductor and in a socket without a ground
conductor contact will be deemed gross negligence. The manufacturer shall not be held
liable for any damage arising from such usage.
If necessary, provide an adequate earth connection for the workpiece.
Switch off unused devices.
Wear a safety harness if working at height.
Before working on the device, switch it off and pull out the mains plug.
Attach a clearly legible and easy-to-understand warning sign to the device to prevent any
-
one from plugging the mains plug back in and switching it on again.
After opening the device:
-
Discharge all live components
-
Ensure that all components in the device are de-energised
If work on live parts is required, appoint a second person to switch off the main switch at
the right moment.
Meandering weld
-
ing currents
If the following instructions are ignored, meandering welding currents can develop with the
following consequences:
-
Fire hazard
-
Overheating of parts connected to the workpiece
-
Irreparable damage to ground conductors
-
Damage to device and other electrical equipment
Ensure that the workpiece is held securely by the workpiece clamp.
Attach the workpiece clamp as close as possible to the area that is to be welded.
If the floor is electrically conductive, the device must be set up with sufficient insulating ma
-
terial to insulate it from the floor.
If distribution boards, twin-head mounts, etc., are being used, note the following: The elec
-
trode of the welding torch / electrode holder that is not used is also live. Make sure that the
welding torch / electrode holder that is not used is kept sufficiently insulated.
In the case of automated MIG/MAG applications, ensure that only an insulated wire elec
-
trode is routed from the welding wire drum, large wirefeeder spool or wirespool to the wire-
feed unit.
EMC Device Clas
-
sifications
Devices in emission class A:
-
Are only designed for use in industrial settings
-
Can cause line-bound and radiated interference in other areas
Devices in emission class B:
-
Satisfy the emissions criteria for residential and industrial areas. This is also true for
residential areas in which the energy is supplied from the public low-voltage mains.
EMC device classification as per the rating plate or technical data.
EMC measures
In certain cases, even though a device complies with the standard limit values for emis
-
sions, it may affect the application area for which it was designed (e.g. when there is sen
-
sitive equipment at the same location, or if the site where the device is installed is close to
Summary of Contents for WF 15i n.S.
Page 2: ...2...
Page 4: ...4...
Page 17: ...General...
Page 18: ......
Page 21: ...Controls connections and mechani cal components...
Page 22: ......
Page 29: ...29 EN OPT i WF Stand ard control panel 1 9 8 5 6 10 11 12 2 3 4 7 14 13...
Page 33: ...Installation and commissioning...
Page 34: ......
Page 39: ...39 EN 1 2...
Page 45: ...45 EN 1 2 1 2...
Page 52: ...52...
Page 53: ...Troubleshooting maintenance and disposal...
Page 54: ......
Page 61: ...Technical data...
Page 62: ......
Page 66: ...66...
Page 67: ...67 EN...