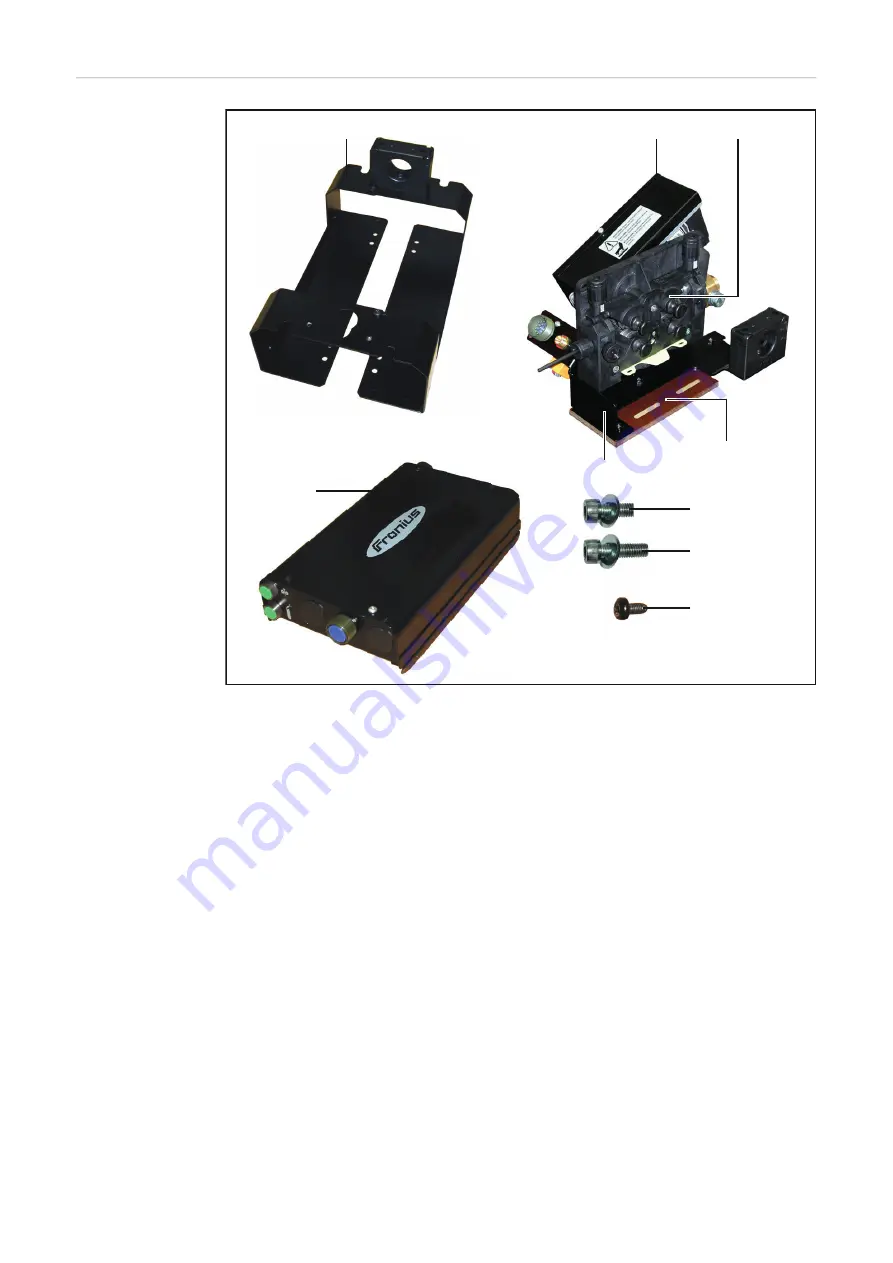
18
Scope of delivery
Lieferumfang VR 1500-M
(1)
1 x controller mounting bracket
(2)
1 x drive cover
(3)
1 x drive plate with feeder rolls 1.0 mm / trapezoid groove
(4)
1 x drive plate bracket
(5)
1 x insulation plate
(6)
1 x Controller
(7)
4 x hexagonal socket head screw M6 x 16 + washer
(8)
2 x hexagonal socket head screw M6 x 25 + washer
(9)
4 x screws Extrude-Tite M5 x 10