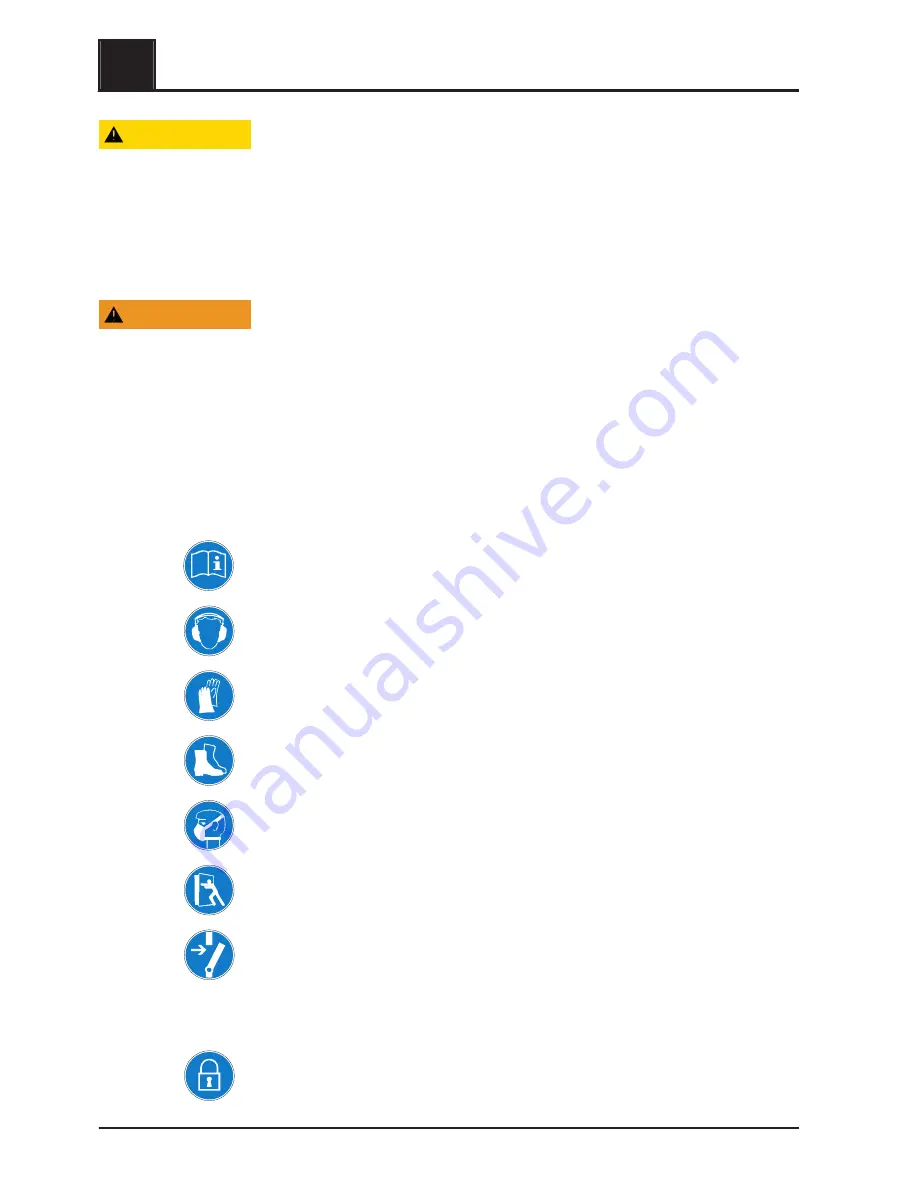
CAUTION
ADJUSTMENT OF THE FLUE DRAFT HIGHER THAN 0.12 INCHES WATER COL‐
UMN (30 Pa) COULD CAUSE A FIRE TO BURN OUT OF CONTROL AND AN UN‐
SAFE CONDITION!
❒ Maximum permitted setting: 0.12 inches WC (30 Pa)
Ideal setting: 0.04 inches WC (10 Pa)
2.4 Safety markers
WARNING
Danger if signage is illegible!
❒ Ensure that all safety, warning and operating instructions are always in a clearly
legible condition.
❒ Replace damaged stickers and signs immediately.
➥ Over time stickers and signs can get dirty or otherwise unrecognizable which
means that dangers cannot be identified and the necessary operating informa‐
tion cannot be observed. This poses a risk of injury.
The following stickers are located in the work area. They refer to the area immediately
surrounding where they are affixed.
2.4.1 Mandatory signs
Refer to the operating instructions
Only use the indicated system once you have read the operating instructions.
Wear hearing protection
This sign indicates that hearing protection must be worn in the area concerned.
Wear protective gloves
This sign indicates that protective gloves must be worn in the area concerned.
Wear safety shoes
This sign indicates that safety shoes must be worn in the area concerned.
Wear a dust mask
This sign indicates that a dust mask must be worn in the area concerned.
Keep the doors closed
Keep the doors closed during operation.
Turning off the main switch
Switch off the main switch and take precautions to prevent accidental switching on be‐
fore carrying out work to the system
Switch off the main switch for the fuel infeed and take precautions to prevent acciden‐
tal switching on before entering the fuel storage room.
Securing the main switch
Switch off the main switch and secure with a padlock when carrying out maintenance
work to the boiler.
2
Safety
Safety markers
18
Froling GesmbH | A-4710 Grieskirchen, Industriestraße 12 | www.froeling.com