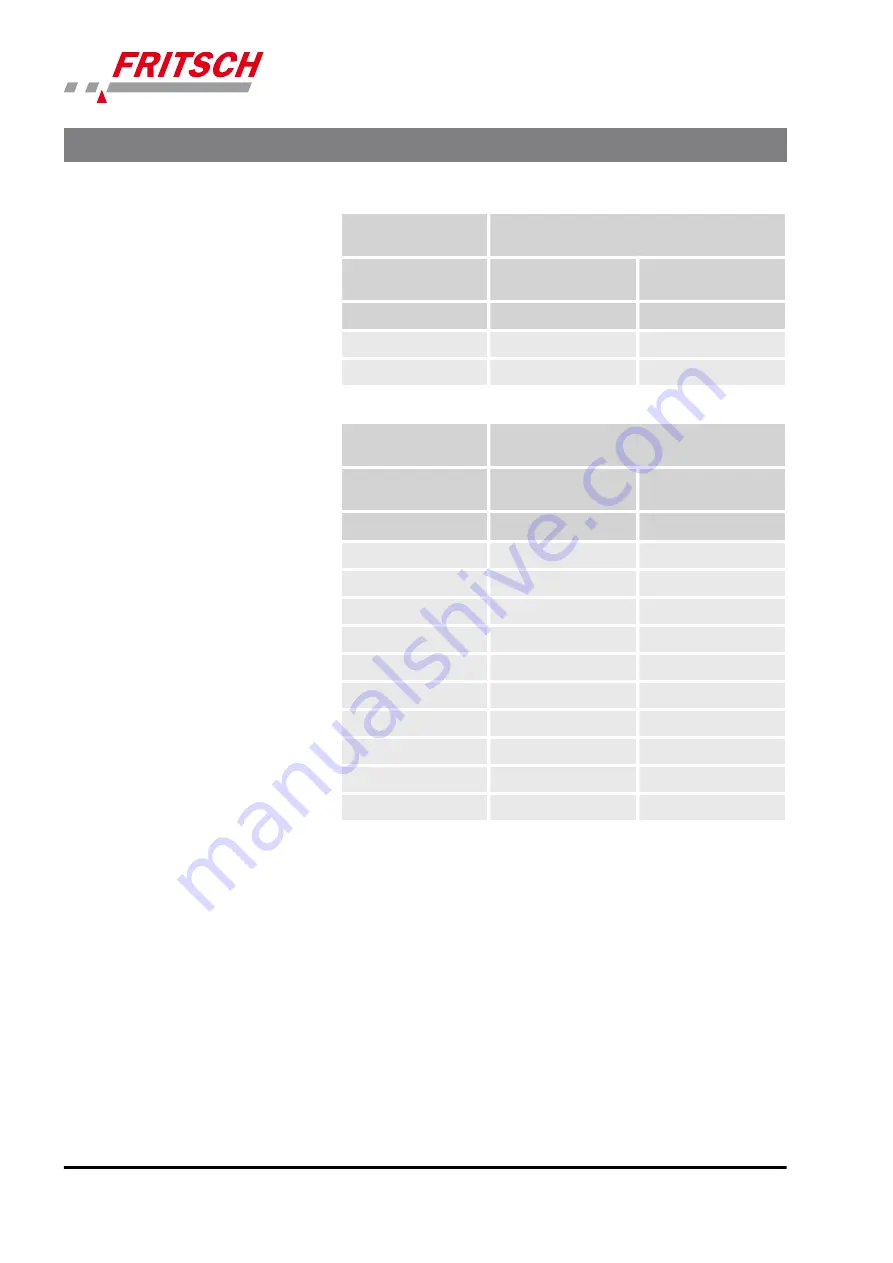
Bulk volume for test sieves with a diameter
of 400 mm
Nominal mesh width
w
Feeding volume
Maximum sieve res-
idue
µm
approx. cm
3
approx. cm
3
500
200
100
710
240
120
Bulk volume for test sieves with a diameter
of 400 mm
Nominal mesh width
w
Feeding volume
Maximum sieve res-
idue
mm
approx. cm
3
approx. cm
3
1.0
280
140
1.4
320
160
2.0
400
200
2.8
480
240
4.0
700
350
5.6
800
400
8.0
1000
500
11.2
1600
800
16.0
2000
1000
22.4
3200
1600
Using the device
- 24 -