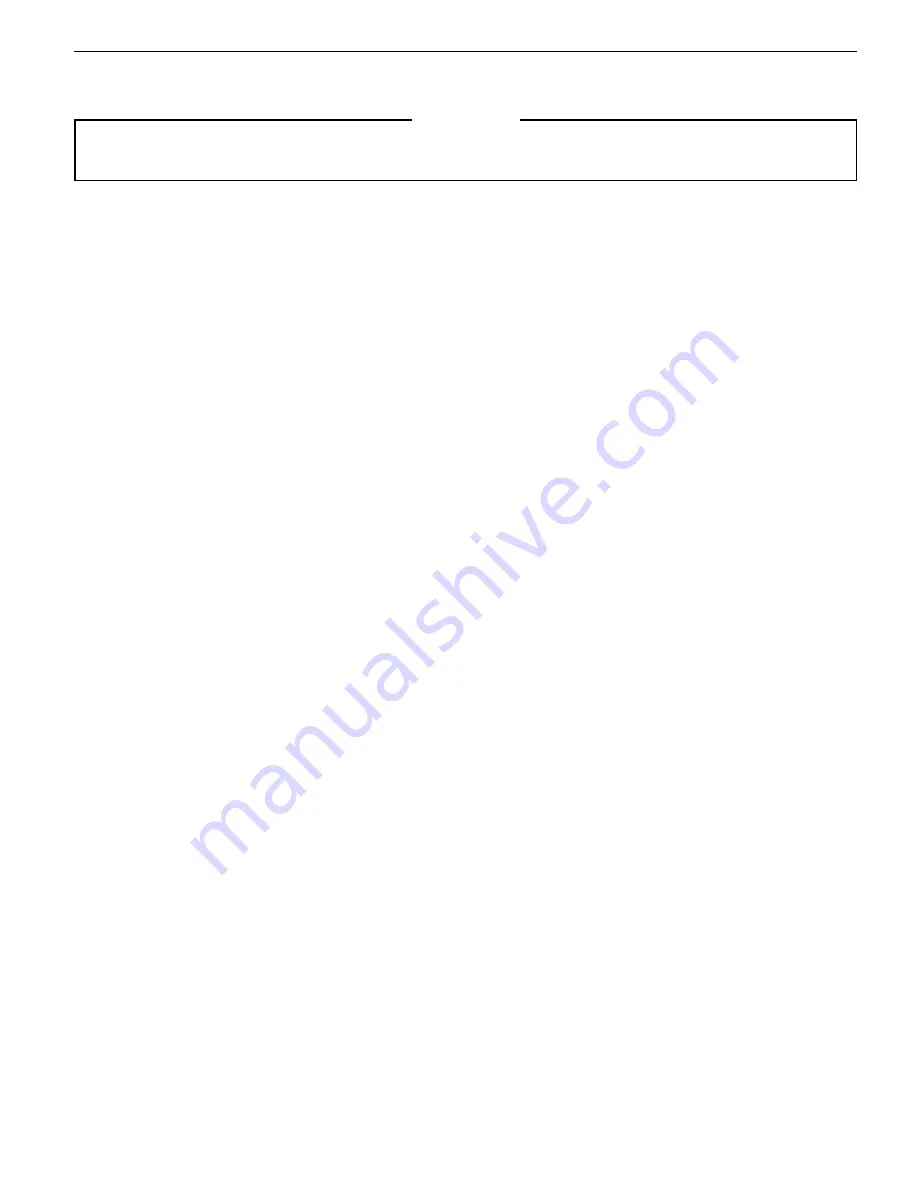
9
EQUIPMENT REQUIRED
1. Voltmeter
2. Ammeter
3. Ohmmeter
4.
E.P.A. Approved Refrigerant Recovery System.
5.
Vacuum Pump (capable of 200 microns or less vacuum.)
6. Acetylene Welder
7.
Electronic Halogen Leak Detector (G.E. Type H-6 or
equivalent.)
8.
Accurate refrigerant charge measuring device such as:
a. Balance Scales - 1/2 oz. accuracy
b. Charging Board - 1/2 oz. accuracy
9.
High Pressure Gauge - (0 - 400 lbs.)
10.
Low Pressure Gauge - (30 - 150 lbs.)
11.
Vacuum Gauge - (0 - 1000 microns)
EQUIPMENT MUST BE CAPABLE OF:
1.
Recovery CFC’s as low as 5%.
2.
Evacuation from both the high side and low side of the
system simultaneously.
3.
Introducing refrigerant charge into high side of the
system.
4.
Accurately weighing the refrigerant charge actually
introduced into the system.
5. Facilities for fl owing nitrogen through refrigeration tubing
during all brazing processes.
HERMETIC COMPONENT REPLACEMENT
The following procedure applies when replacing components
in the sealed refrigeration circuit or repairing refrigerant leaks.
(Compressor, condenser, evaporator, capillary tube, refrigerant
leaks, etc.)
1.
Recover the refrigerant from the system at the process
tube located on the high side of the system by installing a
line tap on the process tube. Apply gauge from process
tube to EPA approved gauges from process tube to EPA
approved recovery system. Recover CFC’s in system to at
least 5%.
2.
Cut the process tube below pinch off on the suction side
of the compressor.
3.
Connect the line from the nitrogen tank to the suction
process tube.
4.
Drift dry nitrogen through the system and un-solder the
more distant connection fi rst. (Filter drier, high side process
tube, etc.)
5.
Replace inoperative component, and always install a new
fi lter drier. Drift dry nitrogen through the system when
making these connections.
HERMETIC COMPONENT REPLACEMENT cont’d
6.
Pressurize system to 30 PSIG with proper refrigerant and boost
refrigerant pressure to 150 PSIG with dry nitrogen.
7.
Leak test complete system with electric halogen leak
detector, correcting any leaks found.
8.
Reduce the system to zero gauge pressure.
9.
Connect vacuum pump to high side and low side of system
with deep vacuum hoses, or copper tubing. (Do not use
regular hoses.)
10.
Evacuate system to maximum absolute holding pressure
of 200 microns or less. NOTE: This process can be
accelerated by use of heat lamps, or by breaking the
vacuum with refrigerant or dry nitrogen at 5,000 microns.
Pressure system to 5 PSIG and leave in system a
minimum of 10 minutes. Release refrigerant, and proceed
with evacuation of a pressure of 200 microns or less.
11.
Break vacuum by charging system from the high side with
the correct amount of liquid refrigerant specifi ed. This will
prevent boiling the oil out of the crankcase, and damage
to the compressor due to over heating.
NOTE:
If the entire charge will not enter the high side, allow the
remainder to enter the low side in small increments while operating
the unit.
12.
Restart unit several times after allowing pressures to stabilize.
Pinch off process tubes, cut and solder the ends. Remove
pinch off tool, and leak check the process tube ends.
SPECIAL PROCEDURE IN THE CASE OF COMPRESSOR
MOTOR BURNOUT
1.
Recover all refrigerant and oil from the system.
2.
Remove compressor, capillary tube and fi lter drier from the
system.
3.
Flush evaporator condenser and all connecting tubing with
dry nitrogen or equivalent, to remove all contamination
from system. Inspect suction and discharge line for carbon
deposits. Remove and clean if necessary.
4.
Reassemble the system, including new drier strainer and
capillary tube.
5.
Proceed with processing as outlined under hermetic
component replacement.
ROTARY COMPRESSOR SPECIAL TROUBLESHOOTING
AND SERVICE
Basically, troubleshooting and servicing rotary compressors
is the same as on the reciprocating compressor with only one
main exception:
NEVER, under any circumstances, charge a rotary compressor
through the LOW side. Doing so would cause permanent damage
to the new compressor.
IMPORTANT
ANY SEALED SYSTEM REPAIRS TO COOL-ONLY MODELS REQUIRE THE INSTALLATION OF A LIQUID LINE DRIER.
ALSO, ANY SEALED SYSTEM REPAIRS TO HEAT PUMP MODELS REQUIRE THE INSTALLATION OF A SUCTION LINE DRIER.
Sealed Refrigeration System Repairs