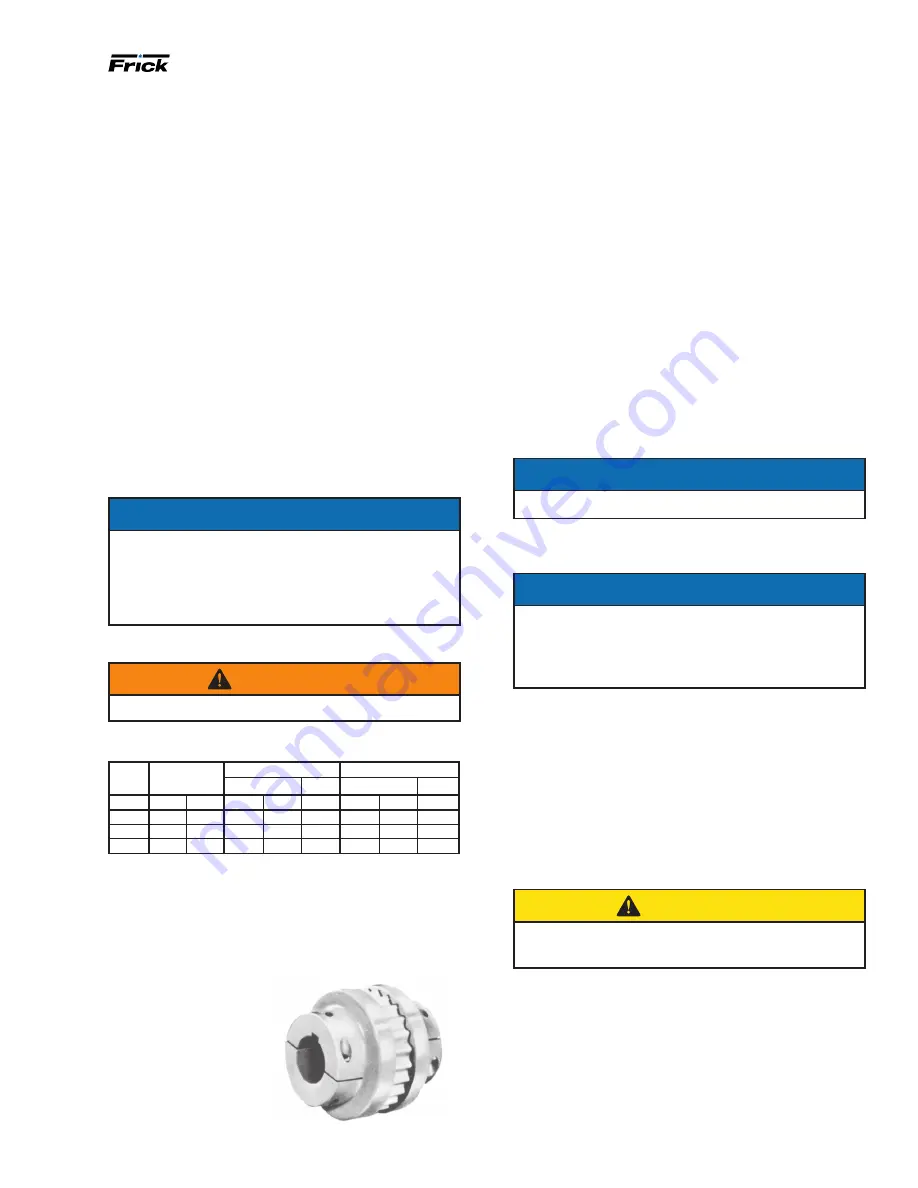
070.610-IOM (JUL 21)
Page 7
RWF II Rotary Screw Compressor Units
Installation
Install the
locknut until it is snug. Make sure that all bolt
threads are clean and lightly oiled. Do not torque any lock
-
nuts at this time. Now pivot the unitized flex disc until the
other bushing holes in the flex disc are in line with the bolt
holes in the spacer. Install the rest of the spacer bolts at
this time. The remaining bolts for this end of the coupling
can be installed through the hub bolt holes and flex disc
bushing holes.
Install the unitized flex disc in the other end of the cou
-
pling. The unitized flex disc, as installed, should look flat
and parallel with the mating hub and spacer flanges.
Torque the disc pack locknuts as suggested in
.
The bolts should be held in place while the locknuts are
torqued.
3.
Center the coupling between the shafts. Ensure that
the keys are fully engaged in their keyways.
4.
Tighten the motor and compressor shaft clamping bolts
evenly. Torque to the recommended specification in
.
5.
Torque the keyway setscrews as recommended in
.
NOTICE
Only after the shaft clamping bolts are tightened to
their final torque can the keyway set screws be tight
-
ened. If the keyway set screws are tightened before
the shaft clamping bolts are tightened, then the hubs
can be cocked on the shaft.
CH Series coupling
WARNING
CH couplings are not to be used over 3600 rpm.
Table 4: CH Series coupling data
CH
series
Face
spacing
Clamp bolt
Keyway setscrew
Torque (dry) Size
Torque
Size
Size
in.
mm
ft-lb N.m
UNF
ft-lb N.m
UNC
9
1
7
⁄
16
36.5
55
74.6
3
⁄
8
-24 13
17.6
5
⁄
16
-18
10
1
11
⁄
16
42.9
130
176.3
½ -20 13
17.6
5
⁄
16
-18
11
1
7
⁄
8
47.6
130
176.3
½ -20 13
17.6
5
⁄
16
-18
CH coupling installation procedure
The CH Coupling is used in most applications. This cou
-
pling consists of two drive hubs and a gear-type Hytrel or
EDPM and neoprene drive spacer. The split hub is clamped
to the shaft by tightening
the clamp screws. Torque
is transmitted from the motor
through the elastomeric gear
which floats freely between
the hubs. Because of the
use of the motor/compres-
sor adapter housing on the
RWF II, no field alignment is
necessary.
1.
Inspect the shaft of the motor and compressor to en-
sure that no nicks, grease, or foreign matter is present.
2.
Inspect the bores in the coupling hubs to make sure
that they are free of burrs, dirt, and grit.
3.
Check that the keys fit the hubs and shafts properly.
4.
Slide one hub onto each shaft as far as possible. It may
be necessary to use a screwdriver as a wedge in the slot
to open the bore before the hubs will slide on the shafts.
5.
Rotate both hubs so that the keys are 180° opposed.
6.
Hold the elastomeric gear between the hubs and slide
both hubs onto the gear to fully engage the mating teeth.
Center the gear and hub assembly so there is equal en
-
gagement on both shaft
s. Note that the hubs may over-
hang the ends of shafts.
Adjust the face spacing between
. Ensure that the keys are
fully engaged in their keyways.
7.
Torque the
clamping bolts in both hubs to the torque
value given in the
NOTICE
DO NOT USE ANY LUBRICANT ON THESE BOLTS
.
8.
Torque the keyway setscrew in both hubs to the torque
value given in the
NOTICE
Only after the shaft clamping bolts are tightened to
their final torque can the keyway set screws be tight
-
ened. If the keyway set screws are tightened before
the shaft clamping bolts are tightened, then the hubs
can be cocked on the shaft.
Oil pump coupling
Compressor units with direct motor/pump coupled pumps
need no pump/motor coupling alignment since this is
maintained by the close-coupled arrangement.
Holding charge and storage
Each
RWF II
compressor unit is pressure and leak tested
at the factory and then thoroughly evacuated and charged
with
dry nitrogen to ensure the integrity of the unit during
shipping and short-term storage before installation.
CAUTION
Care must be taken when entering the unit to ensure
that the nitrogen charge is safely released.
Figure 6: CH coupling