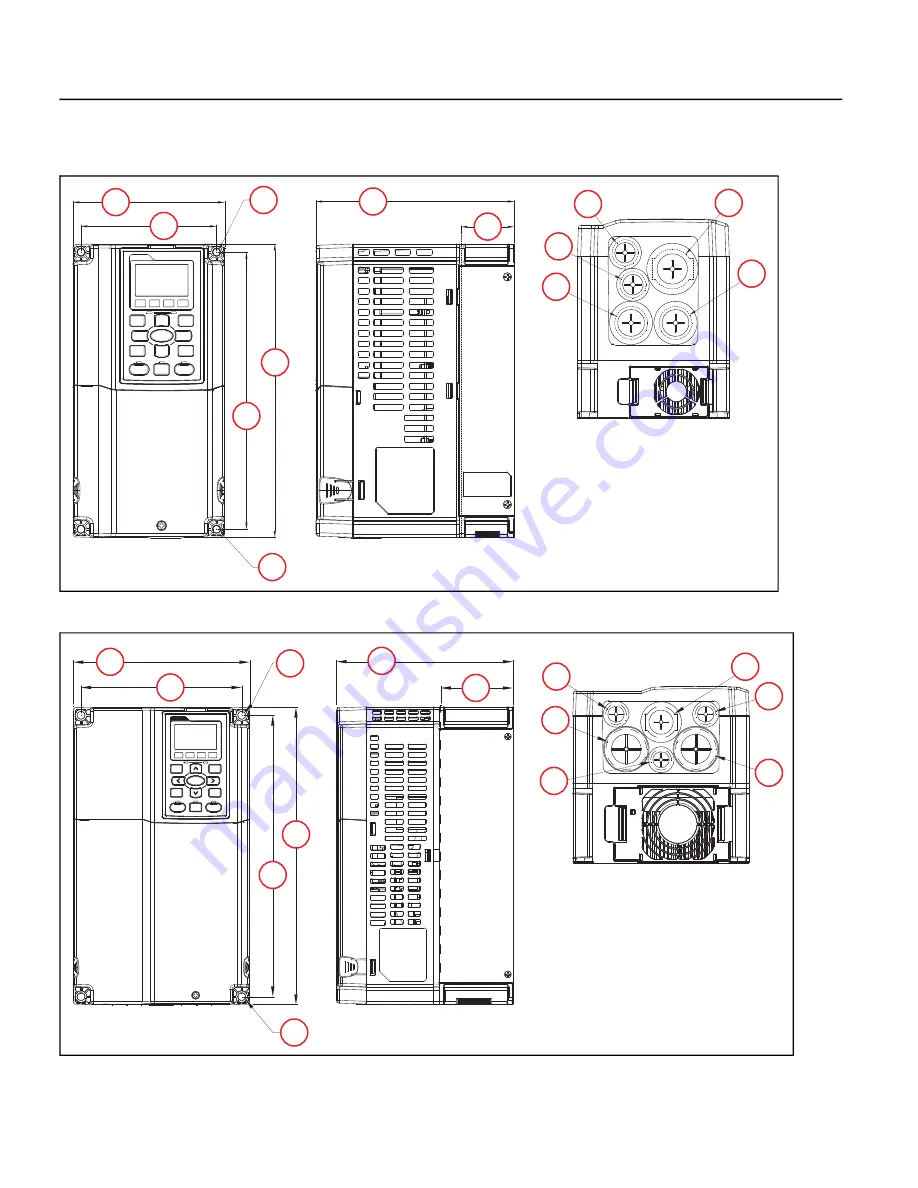
PHYSICAL INSTALLATION
Drive Dimensions
28
Drive Dimensions
Frame A
Frame B
1
2
3
4
5
5
7
8
9
6
8
10
10
1 - 130 mm (5.12 in)
2 - 116 mm (4.57 in)
3 - 250 mm (9.84 in)
4 - 236 mm (9.29 in)
5 - 6.2 mm (0.24 in)
6 - 170 mm (6.69 in)
7 - 45.8 mm (1.8 in)
8 - 22.2 mm (0.87 in)
9 - 34 mm (1.34 in)
10 - 28 mm (1.10 in)
1
2
3
4
5
6
7
8
9
5
8
8
10
10
1 - 190 mm (7.48 in)
2 - 173 mm (6.81 in)
3 - 320 mm (12.6 in)
4 - 303 mm (11.9 in)
5 - 8.5 mm (0.33 in)
6 - 190 mm (7.48 in)
7 - 77.9 mm (3.07 in)
8 - 22.2 mm (0.87 in)
9 - 34 mm (1.34 in)
10 - 43.8 mm (1.72 in)
Summary of Contents for CERUS X-DRIVE CXD-003A-4V
Page 2: ......
Page 3: ...CERUS X DRIVE INSTALLATION AND OPERATION MANUAL Firmware Version 1 2 Franklin Electric Co Inc ...
Page 96: ...OPERATION Protection Features 96 ...
Page 112: ...ADVANCED APPLICATION OPTIONS Multi Drive Configurations 112 ...
Page 124: ...COMMUNICATIONS BACnet Communication 124 ...
Page 128: ...ACCESSORIES Optional Extension Cards 128 Frame D Frame E Frame F ...
Page 129: ...ACCESSORIES Optional Extension Cards 129 Frame G Frame H ...
Page 132: ...ACCESSORIES Optional Extension Cards 132 ...
Page 234: ...PARAMETER REFERENCE TABLES Parameter Descriptions Motor Menu 234 ...
Page 250: ...GLOSSARY 250 ...